Sensors: The IoT Enablers
July 26, 2019
Blog
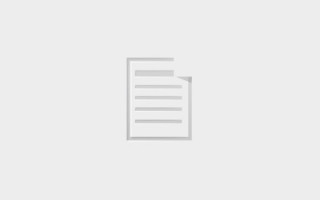
Sensors are the components that provide the actionable insights that power the IoT and enable organizations to make more effective business decisions.
As the Internet of Things (IoT) enables devices to make intelligent decisions that generate positive business outcomes, it’s the sensors that enable those decisions. As cost and time-to-market pressures continue to rise, sensors provide greater visibility into connected systems and empower those systems to react intelligently to changes driven by both external forces and internal factors.
Sensors are the components that provide the actionable insights that power the IoT and enable organizations to make more effective business decisions. It’s through this real-time measurement that the IoT can transform an organization’s ability to react to change.
For example, consider a fleet of garbage collection trucks that periodically empty trash bins. Most trucks have a consistent weekly route for emptying bins, whether they’re full or not, because the schedule does not account for how people use them. If an ultrasonic sensor is incorporated into the design of the trash bin, it can provide the waste management company with valuable data about how much trash is inside, and then optimize trash collection routes accordingly.
Similarly, in an industrial environment, the use and combination of different sensor modalities can improve responsiveness and flexibility, as well as increase overall uptime. In a factory, sensors can monitor vibration and temperature to gauge machine motor health, as well as guide materials around the shop floor as products are assembled. The possible applications are limitless.
Sensors Abound
Sensors detect or measure various physical parameters, each suited to different markets and applications. Considering there are 19 major categories of sensors alone, as well as additional categories for transducers and encoders, determining which sensor is best for your project can be a daunting task. Broadly speaking, sensors fall into the following categories:
Physical position and motion sensors. These sensors are ideal for proximity sensing, linear and angle sensing, and accelerometers for detecting motion and orientation (as in mobile phones, for example). Position sensors can also be used in motor-control and robotics applications.
Light sensors and scanners. These types of sensors can be incorporated into a wide range of applications, from simply knowing when to turn lights on and off in a building or a vehicle, to sophisticated machine vision systems for factory automation.
Fluid and gas sensors. For industrial process control environments, fluid and gas sensors measure parameters such as level, pressure and flow, and detect potential fault conditions.
Temperature sensors. In addition to supporting heating and ventilating systems in domestic, automotive and building automation environments, temperature sensors are also optimal for process monitoring and control in a variety of industries.
Force, shock and vibration sensors. These sensors provide invaluable data in industrial monitoring and control systems, as well as in-vehicle testing in automotive, transport and aerospace applications.
Ultrasonic sensors. These sensors are often used for distance measurement, particularly with robotics.
Electrical or current sensors. While electrical sensors optimize the efficiency of power-supply units or the performance of motor control systems, they also detect issues in motors and drive systems.
Magnetic sensors. These are ideal for providing position and revolution information in the harsh environments found in the automotive sector.
When designing “intelligent” systems, choosing the right sensor is critical, but there are key parameters common to many sensor applications to consider. These include:
Sensitivity. Defined as the slope of the output characteristic curve or, more generally, the minimum input of the physical parameter that will create a detectable output change.
Sensitivity error. A departure from the ideal slope of the characteristic curve.
Range. The maximum and minimum values of applied parameter that can be measured.
Dynamic range. The total range of the sensor from minimum to maximum.
Precision. The degree of reproducibility of a measurement.
Resolution. The smallest detectable incremental change of input parameter that can be detected in the output signal.
Accuracy. The maximum difference between the actual value (measured by a primary or good secondary standard) and the indicated value at the output of the sensor.
Offset. The output that will exist when it should be zero or, alternatively, the difference between the actual output value and the specified output value under some particular set of conditions.
Linearity. The extent to which the actual measured curve of a sensor departs from the ideal curve.
Hysteresis. The measure of how well a transducer is capable of following the changes of the input parameter irrespective of the direction from which the change is made.
Response time. The time required for a sensor output to change from its previous state to a final settled value within a tolerance band of the correct new value.
Dynamic linearity. The measure of a sensor’s ability to follow rapid changes in the input parameter.
Interfacing with Sensors
Other key factors involved in sensor selection are cost and the ease of interfacing the sensor output with the measurement and control electronics – generally provided by a microcontroller or processor. Interfacing sensors for IoT applications is relatively straightforward, as there are really only three types of output: analogue, modulated or digital. Modulated output uses a technique such as pulse-width modulation (PWM), for example. Digital output leverages industry standard digital interfaces like SPI or I2C.
For meeting the most stringent demands encountered in modern industrial applications, the Analog Devices Blackfin processor is based on a powerful, scalable, software-programmable 16/32-bit embedded architecture that blends a microcontroller unit (MCU) and digital signal processing (DSP) capabilities onto a single chip. Blackfin processors provide the ideal single-processor solution for applications where a convergence of capabilities is necessary, such as transducer-based measurement and control processes.
Sensors in Action
Sensors are key to effectively enhancing your IoT project, and selecting the right sensor is just as important as determining how it will share the data it collects. To maximize real-time responsiveness, local gateways will often process the raw data and relay instructions to nearby actuators and other equipment to keep the connected system running smoothly. In parallel, they will filter and organize data so that it can be processed by remote cloud analytics engines more easily. The cloud makes it easy for organizations to access high-performance computing on demand to deliver real-time knowledge and maximize the value of the incoming data.
An example of a cloud-based system for handling IoT data is Schneider Electric’s EcoStruxure. The solution consists of apps, analytics and services layers that have been tuned for industries including building management, data-center operations, industrial control, and energy-grid networks. As interoperability is key to supporting the diverse hardware and systems that are used in each of these four industries, EcoStruxure enables a breadth of device-agnostic applications, analytics and services for seamless enterprise integration.
EcoStruxure includes support not just for processing in the cloud but also in the edge-control layer, providing the critical ability to manage operations locally and support advanced automation and operator capabilities. Local servers will act as wireless gateways for the sensors that are closest to them. However, with support for low-power wide-area network (LPWAN) technologies such as Sigfox and LoRa, a single gateway can cover a very large area over several miles, enabling IIoT support for users in energy-grid and utility-supply applications, as well as agriculture.
Many industries can take advantage of the combination of XIOT sensors and the EcoStruxure cloud. In one application, sensors were installed in a utility’s ducts and drainage pipes to monitor whether valves used to help convey rainwater through the network are functioning as expected. No electrical connection was available, although photovoltaic panels could be used in some locations to power the sensor units.
In agriculture, limit switches fitted to mobile irrigation systems are now used to detect obstacles in the path of each machine and to know when each irrigation cycle is finished. Pressure sensors check for broken or leaking pipes and the data is relayed over LPWAN, so that a single cloud system can monitor the progress of irrigators operating over a huge area without requiring costly regular visits by human operators.
And remember our waste management example? When sensors provide real-time data on how full a trash bin is, organizations can leverage software to adjust the routes of different trucks dynamically and skip bins that do not need to be emptied. Simply adding one new type of sensor greatly improves responsiveness of the waste collection service. Adding location-tracking sensors to the trucks themselves makes it possible to redirect trucks in real time, all of which enable intelligent decisions that optimize the service, improve efficiency for the business and drive growth.
Sensors come in many forms, with applications for heavy industry to consumer devices. As connected devices continue to evolve and provide more advanced intelligence, sensors are the key to powering the IoT.