Five Senses of an Industrial Factory
July 17, 2023
Blog
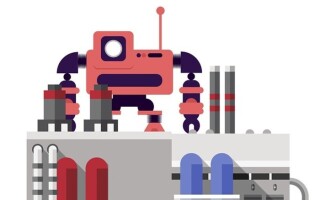
A well-considered strategy to run and monitor an industrial factory is critical to its safe and profitable operation. In addition to strong policies and procedures, surveillance of security and safety of buildings, operating equipment, staff, logistics, and availability of real-time response to any emerging problem are at the heart of reliable and successful factory operation.
The “Industrial Internet of Things,” “Industry 4.0,” or simply “smart manufacturing,” are terms that have emerged in recent years. These reflect technological advances and breakthroughs in microelectronics and micromachining leading to the development and adoption of high-performance, intelligent, and cost-effective sensors. These sensors have contributed immensely to the transformation of industrial factories. They are critical in producing and collecting data. The sensors have impacted every step of factory operation and enabled changes to every facet of effective manufacturing.
Sensors are the cornerstone of a safe, efficient, and productive industrial plant. Combined with innovative software solutions, these sensors support collecting and analyzing of data to make plants safer and more efficient. Operators and technicians can assess and diagnose the health condition of plant and equipment. From this, they can take appropriate steps to prevent potential safety issues and minimize downtime.
A modern industrial plant is a complex operation and companies often monitor many aspects to ensure a safe and productive environment. Real-time monitoring and sensing critical parameters at a plant is paramount to the execution of a successful plant strategy.
The most successful state-of-the-art smart factories are finding automation, machine learning (ML), and artificial intelligence (AI) to be essential building blocks. These blocks help the factory collect data through sensors by monitoring processes, products, and assets. Then, they analyze the data first, to build a knowledge base that allow the factory and machinery to make timely and sound decisions. These decisions can then help improve efficiency, reduce cost, and increase productivity. Figure 1 illustrates a block diagram of a modern factory with critical components.
Figure 1. Sensors in a factory collect and analyze data to support sound decisions.
The latest innovative sensors, equipped with machine learning capabilities, can sense and analyze many parameters and make smart decisions from this effort.
Vibration
Keeping equipment operational is crucial to maintaining optimal throughput and productivity of the plant.
Vibration monitoring of machines can provide critical information about its operational conditions. Vibration monitoring, as part of condition monitoring and predictive maintenance, can help minimize line-down time via early detection and treatment of potential problems.
Operators can deploy sensors to capture vibration data. They can use software tools and analytical methods such as Fast Fourier Transforms (FFT) to first establish an operating baseline by analyzing the frequency components of equipment vibration. Once defined, constant vibration sensing and analysis can detect anomalies. Figure 2 shows the pyramid of steps involved in vibration monitoring.
Figure 2. A pyramid of vibration monitoring highlights the various stages of machine-learning model development throughout the factory.
Sensor suppliers, like ST, have developed sensors that can capture vibration frequencies up to several kilohertz of bandwidth [1]. Smart, open, and accurate, these sensors are cost-effective and consume very little power, making them suitable for many applications. Ideally, the sensors are advanced devices with three axes of freedom to capture vibration independent of the mounting position or orientation of the device. Features embedded in these sensors can simplify vibration-monitoring algorithms (Figure 3).
Figure 3. Sound, temperature, and vibration monitoring of an electric motor in operation can identify potential areas of concern before failure.
Balance
Balance — the vertical and horizontal position of a machine — is often an important specification in its use and can directly impact its performance. Unintended deviation from the ideal balanced position, such as might be due to vibrations or jostling, can cause problems that might lead to production shutdowns. To avoid imbalance failures, an operator might typically monitor the machine’s position in real-time. Performed by a worker, this task is costly and inefficient.
Improvements in MEMS (Micro-Electro-Mechanical Systems) technology in recent years have opened the door to tiny high-performance, high-precision sensors that can collect data that dedicated algorithms analyze for real-time position monitoring [2]. These sensors — static inclinometers, for example — can measure the gravity components that a tilt algorithm would use to determine the orientation angle of the machine. On the other hand, a dynamic inclinometer can monitor the balance of the machine in the presence of dynamic motion. Dynamic inclinometers can determine changes in orientation at a high rate and can measure how fast the machine is moving in three dimensions (Figure 4).
Figure 4. Dynamic inclinometers are effective in monitoring the position and movement of an industrial robot.
Sound
The sound a machine generates during operation can be a major characteristic of declining performance. Moreover, as the frequency of that sound can extend into the ultrasonic range, it isn’t always audible to humans. Sound anomaly, detected by appropriate sensors, is an important indicator for operators to monitor.
Early-stage leak detection in pipes delivering chemical gases, for example, is critical to avoiding catastrophic damage. Because the sound from a leak usually starts in the ultrasonic range, a factory should choose a dedicated sensor to sense these ultrasonic acoustic waves.
The latest MEMS microphones offer the performance and cost advantage for sensitive ultrasonic sound detection. These microphones can also support voice-command applications [3]. Key advantages of MEMS microphones are easy system integration, small size, high signal-to-noise ratios, robustness, reliability, and affordability. MEMS microphones are well suited to applications aiming to detect compressed fluid leaks, vacuum leaks, steam trap failures, bearing condition monitoring, electrical arcing/tracking, fan and motor unbalance.
Figure 5 shows the trajectory of a typical machine’s condition over time and how those changes can be identified and detected. Noise in the ultrasound range is often the first signal that indicates that the machine’s condition is starting to change.
Figure 5. Ultrasound, vibration, and heat detection are among the most critical changes when monitoring equipment operation.
Operators can also use sensing and monitoring solutions equipped with MEMS microphones and speech recognition algorithms to operate and control equipment via voice command.
Heat
All factory equipment is designed to operate within a predefined temperature range. Friction from failing mechanical components in a machine typically generates undesired heat that can further damage equipment parts. As Figure 5 shows, heat in the failure trajectory of a machine is very close to its final failure stage. In a worst-case scenario, this heating could lead to sparks and fire that can destroy assets — potentially even the factory.
Infrared cameras and temperature sensors are useful to create thermal profiles. Accurate and affordable temperature sensors are available and can be installed on the equipment to monitor the operating temperature range [4] in real time during operation. Then, sudden increases in the equipment’s temperature would lead the sensor to generate an interrupt signal. That signal is a clear indication of a potential problem and would alert staff to take necessary measures to avoid equipment failure.
Sensing Presence
Presence detection — of people and/or equipment — can provide key information for enterprise resource-planning (Figure 6c). Sensors can efficiently detect the number and location of people and the operating machines in a factory to optimize energy consumption and increase safety and security.
A presence detector consists of hardware and software tools and can be an expensive investment in a modern factory. The number and type of presence detection sensors will ultimately determine the features in the solution. Knowing the use cases for presence detection helps companies justify the development cost as part of an overall enterprise resource-planning solution.
Intelligent HVAC control and automated lighting shutoffs use presence detection to optimize energy use and enable significant savings (Figure 6b). There are already proposed solutions to reduce energy consumption, including by using multiple thermal imagers [5].
Thermal imaging using infrared detection is an innovative solution for presence detection [6]. Figure 6a shows the high-level design structure of this solution. Sensors able to operate in the 5μm to 20μm wavelength range of the electromagnetic spectrum can detect human presence by accurately sensing the amount of infrared radiation emitted from an object in the sensor's field of view. The information collected by the sensor can then be digitally processed by dedicated circuits embedded inside the tiny chip. The device offers the programmability to monitor motion, presence, or over-temperature conditions. Without a lens, it can detect human presence up to 4 meters away.
Figure 6. High-level structure showing innovative IR sensor for occupancy and presence detection.
A successful presence detector fuses algorithms to process the sensor data with artificial intelligence algorithms to meet the demands for a 21st century factory.
Future Trends
Deploying sensors in an industrial plant allows continuous collection of real-time data to monitor the operational status and condition of products and equipment.
In the most efficient factories, companies are using sensors to optimize efficiency, increase productivity, improve safety, and advance security. Still, in addition to sensors, companies need to continue adding comprehensive software tools for data analytics. Dedicated solutions will process and analyze sensor data using artificial intelligence to build models that can make operational and production decisions. Technologies and solutions for edge and cloud computing will play a critical role in implementing enterprise resource planning and execution solutions.
References
- IIS3DWB - Ultra-wide bandwidth, low-noise, 3-axis digital vibration sensor - STMicroelectronics
- IIS2ICLX - High-accuracy, High-resolution, Low-power, 2-axis Digital Inclinometer with Embedded Machine Learning Core - STMicroelectronics
- IMP23ABSU - Analog bottom port microphone with frequency response up to 80kHz for Ultrasound analysis and Predictive Maintenance applications - STMicroelectronics
- STTS22H - Low-voltage, ultra-low-power, 0.5 °C accuracy I2C/SMBus 3.0 temperature sensor - STMicroelectronics
- A Novel Occupancy Detection Solution using Low-Power IR-FPA Based Wireless Occupancy Sensor. Aravind K. Mikkilineni et al., Energy and Buildings, 2019
- STHS34PF80 - Low-power, high-sensitivity infrared sensor for presence and motion detection - STMicroelectronics