Robotic exoskeletons: The key to human superpowers
November 03, 2017
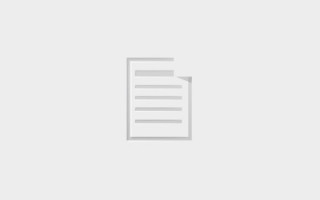
Ever wanted a superpower? How about super-strength or super-endurance? Or the ability to help paralyzed people to move again?
Ever wanted a superpower? How about super-strength or super-endurance? Or the ability to help paralyzed people to move again? While this may seem like the stuff of sci-fi, these are already realities – and super-speed isn’t far behind.
So-called "robotic exoskeletons" make this possible. These external skeletons – typically made of metal or another durable material – fit around the human body and move just like our arms and legs. The key difference is that a robotic exoskeleton can do so with greater force, precision, and speed.
Let’s have a look at some of these achievable superpowers.
Strength
With the help of a robotic exoskeleton, a human being can lift things that weigh several times their weight. Imagine how useful this could be in rescue and recovery scenarios, with workers able to release people trapped in collapsed buildings, for example. In the hands of a well-trained human operator, a robotic exoskeleton provides a blend of controllability and strength that makes it more efficient than traditional heavy machinery in such situations.
Endurance
Robotic exoskeletons don’t get tired in the same way humans do, meaning they’re able to repeat the same tasks for long spells. They can also make equipment virtually weightless to the human operator. This means a person using a robotic exoskeleton could carry out work using heavier equipment and for longer periods than they would otherwise be able to.
Using larger machinery can enable operators to complete tasks more quickly, while the precise control offered by the exoskeleton means they can also be more accurate in their work.
Robotic exoskeletons are programmable, meaning a human can train them in how to perform a particular task and then let the exoskeleton take over, with the human taking a supervisory role to make sure nothing goes wrong. Another option could be for the human operator to oversee a team of robots carrying out various tasks, with the human taking over at critical points where human expertise is required.
Speed
The speed at which robotic exoskeletons can work doesn’t need to be limited to what the human body is capable of. Repetitive actions, such as hammering or cutting, could be significantly accelerated.
More sophisticated movement, including running or climbing, will require more operator experience and training, however. The human operator’s brain may not be able to handle doing these sorts of things too fast. However, with appropriate practice, we could see super-speed athletes breaking all kinds of records.
Materials for robotic exoskeletons
The great thing about all these superpowers is that we don’t need fancy new materials to realize them. Stainless steel alloys will be entirely sufficient for many use cases, while lighter materials, such as carbon (high-tensile) steel, carbon fiber, chrome moly (chrome-molybdenum steel), aluminum, and titanium are all widely used in other areas.
Where strength and durability are the top priorities, steel will likely remain the go-to material. If more flexibility and responsiveness are required at the expense of some strength, chrome moly is a good choice. In reality, as with any complex machinery, it will be common to find a blend of materials within a robotic exoskeleton, tailored to the specific needs of the different parts.
The control system
For a robotic exoskeleton to move autonomously, responding in real time to human input – or even learning from human input – requires an extremely powerful control system. This will need to take sensor data around balance, external conditions, proximity to other objects and the state of the exoskeleton itself, process it, and then respond accordingly.
Learning mode, too, will pose challenges. In this scenario, you’ll need your algorithms to crunch through enormous amounts of data. Ideally, this should be stored locally on solid-state media – spinning disk hard drives aren’t ideal when exoskeletons are operating in severe conditions where vibrations will be standard.
Then there’s the processing power required to drive the various control motors. Analog Devices’ ADSP-CM40 mixed-signal controllers are a good option. A 240 MHz ARM Cortex-M4 processor, the CM40 is built for the sophisticated signal processing algorithms needed to control a robotic exoskeleton. And by using suitable motor control firmware, you can boost efficiency, cut down on wear and tear, reduce vibrations, and thereby lengthen your motors’ lifespans. Moreover, you’ll need algorithms that prevent a motor from burning out. But most importantly, you must protect the human operator by being able to predict whether a particular movement could place too much stress on a component or cause the operator to lose balance.
You’ve plenty of choices when it comes to motor control algorithms – which you choose will depend on your use case, because there are invariably trade-offs. Where strength is your essential requirement, high levels of torque could be more important than efficiency, meaning a brushless DC motor makes an ideal choice. Need speed and precision? Try a stepper motor. There are various motor control development kits, configuration tools and libraries available. Bill Schweber has written at length about choosing the right motor for your robotics project.
Connecting your robotic exoskeleton
One area we haven’t yet touched on is how all the controllers, actuators, and sensors send data to one another. As with the other design choices, this will depend on where and how your robotic exoskeleton is going to be used. In many cases, robustness will be key. Wireless may not always be suitable, particularly in noisy or hostile environments, meaning hard-wiring using robust connectors will remain prevalent. Fiber optic connectors are another possibility, enabling high-speed and extremely robust data transfer. Power cabling, connectors, and housing must be equally robust. Molex makes a range of connectors you can use for fiber optic and traditional data and control interfaces.
How we could use robotic exoskeletons
The lifesaving scenario we touched on above is just one of how robotic exoskeletons with super-strength, endurance, or speed could transform lives. They could also be used to fight fires or during floods, enabling emergency services workers to carry heavy equipment or to build dams to protect and bridges to evacuate flood victims. Chemical spills are another potential use case – provided you can protect the operator and electronics sufficiently (there will be situations that are potentially too hazardous for a human to enter into, in which case a remote-controlled robot, rather than an exoskeleton, could be used).
Another life-changing use case would be to use a robotic exoskeleton to enable an injured or paralyzed person to regain some degree of movement. Using intelligent control systems, the exoskeleton could learn how to autonomously perform certain actions from the human operator. Even walking and running could be partially autonomous, meaning the human needn’t control specific low-level movements.
Researchers are also examining how we could use brainwaves to control robotic movements. Combine this with deep learning algorithms and autonomous control, and you could create extremely high levels of brain-powered operator control. Granted, we’re not there yet, but this exciting possibility showcases just how transformational robotic exoskeletons could be to humanity.
Conclusion
The sorts of superpowers we’ve looked at here are available right now, thanks to state-of-the-art robotic exoskeletons and the technologies that underpin them. And this is only the beginning. Development of intelligent control systems will take these superpowers to another level, making humans super-strong and super-fast, able to save lives following disasters. Equally importantly, robotic exoskeletons could mean paralyzed or wounded people can regain some level of mobility.
The possibilities are truly exciting. Robotic exoskeletons have the power to change lives.