AI Enhances Industrial Machine Vision
August 02, 2023
Sponsored Blog
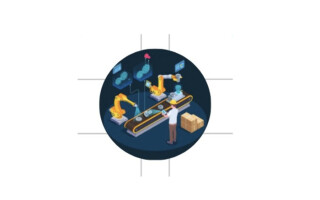
Machine vision, sometimes referred to as computer vision, is a subset AI that lets computers interpret and understand visual information from the world. It involves algorithms and systems that allow machines to "see" and comprehend images or videos, similar to how humans perceive and understand the visual world.
Machine vision has undergone a profound transformation in the area of quality control, ushering in a new era of manufacturing excellence. In this modern age of industrial inspection, these cutting-edge manufacturing and automation systems have the authority to approve or reject a line of parts rolling off the line. Powered by state-of-the-art deep learning technologies, they possess the ability to autonomously optimize the entire manufacturing process, curbing waste and reducing inefficiencies.
One primary goal of machine vision is to process and analyze visual data to extract meaningful information, make decisions, and perform specific tasks. These tasks typically include image recognition, object detection and tracking, and facial and gesture recognition. An important point here is that machine vision removes the human (and the human error) from the equation.
Machine Vison Challenges
There are obviously challenges involved in designing and deploying such a modern system. For example, designing hardware around a GPU could result in the desired performance, but might decrease reliability. In addition, the GPUs’ power consumption poses a predicament as GPUs tend to generate excessive heat, necessitating cooling fans, not a desirable scenario for a robust industrial environment.
The machine-vision process usually goes in this order: image acquisition, image pre-processing, feature extraction, image analysis, and decision making/action taking, based on the analysis.
The use of machine vision is common in factories to improve automation, quality control, and overall efficiency. Its uses tend to vary based on the specific needs of the and processes involved. The processes could include:
- automated product inspection, looking for defects and ensuring that all products meet pre-defined quality standards
- product sorting and/or counting, especially removing defective products
- robot guidance for specific applications, including picking up and placing objects or assembling components
- barcode/QR code reading
- safety and security, to monitor the movement of personnel and detect any hazardous situations
To make these processes possible, specialized components are needed, including high-resolution cameras, image processing hardware, specialized software and algorithms, and potentially additional sensors like lasers or depth cameras. These systems must have the ability to operate in real-time, allowing for immediate decisions and actions to be taken based on the visual data.
With the ability to handle AI inferencing and machine learning, the MiTAC MZI rugged system supports up to 16 Hailo-8 AI processors.
As stated, machine vision can have a profound impact on quality control within the factory. For that to occur, specific hardware must be implemented, along with software routines that fit the application. To that end, MiTAC’s portfolio of high-end products likely fits the bill for implementing machine vision in the factory. Specifically, the combination of the MZ1 plus dual MiAi-H8 cards is up to the task. First, the MZ1 is a rugged GPU computing platform that supports Intel’s 13th Gen Raptor Lake-S and 12th Gen Alder Lake-S Core-i processors, up to 125 W.
To support the machine-vision application, the platform can handle AI inferencing, machine learning, and deep learning. Support is included for up to 16 Hailo-8 AI processors, providing 416 TOPS of performance. Design work can be handled using the Hailo-8 SDK. Other features of the MZ1 include support for up to 64 Gbytes of DDR5 SO-DIMM memory, HDMI, DisplayPort, and VGA graphics capabilities, dual 2.5-Gigabit/s LAN, and 10 USB ports.
The MiAi-H8 expansion card pushes performance to a level of 208 TOPS.
As the companion component, MiTAC’s MiAi-H8 real-time and AI inference acceleration Xpansion PCIe card supports up to eight Hailo-8 AI processors for a performance level of 208 TOPS. It offers both active and passive cooling options. As needed for a factory floor, it’s an industrial-grade design with all solid capacitors and wide temperature support.
On more of a mid-range scale, designers might consider MiTAC’s MX1-D plus GFX combination, which exhibits capable performance, a powerful processor, OCP/OVP power protection, and an expandable design. The MX1-D is powered by Intel’s Coffee Lake C246 workstation chipset which can support Xeon and Core-i LGA1151 socket-type processors.
The MX1-D gets its flexibility from a rich array of I/O ports (dual Ethernet RJ45, eight USB, HDMI, DVI-I, DisplayPort, two COM ports, and more). Storage expandability is supported through three 2.5-in. high-density hard disk drives and two mPCIe (shared with mSATA) slots to accommodate SSD and wireless interfaces.
At the entry level, the combination of the MiTAC MP1 plus a VPU allow for use in industrial machine-vision applications. Specifically, the MP1-11TGS features Intel’s Tiger Lake processor. With its integrated iGPU, it brings AI capabilities when coupled with an AI/deep learning instruction set such as VNNI (Vector Neural Network Instruction). The result is improved inferencing workload performance. The system’s rich I/O offerings include 10-Gbit/s USB 3.1 (Gen2) ports, four serial COM ports, 2.5-Gbit/s Ethernet LAN, and wireless capability. The wide input voltage range (8 to 24 V) and a temperature from -40°C to +70°C are key for the industrial environments.