Improve Autonomous Vehicle Testing with Split-Architecture Embedded Computers
May 25, 2022
Sponsored Story
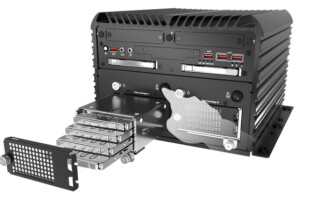
We can no longer say, “autonomous vehicles are coming.” Now, it’s “autonomous vehicles are here.”
The next phase of this technology is to continually test and improve the technology that’s used to deploy those autonomous vehicles. Obviously, the testing is needed to prove that they are safe under any and all road conditions.
With a fluid and complex technology like autonomous driving systems, the testing must be flexible enough to consider changes, potentially on the fly, yet strict enough so that the results have meaning in real-world applications at scale. There are a host of different ways in which that testing can occur.
Among the challenges for testing autonomous vehicles are that they may be in use for quite some time, under many different conditions and environmental challenges. So, the testing schemes must try to emulate tests “over time.” That’s not an easy thing to replicate.
Many tests are performed in the lab, and there’s just no substitute for actual behavior in the field. And in some instances, the vehicles learn and train in the field and adjustments are made in real time.
Cutting the (Wireless) Cord
Another challenge designers of autonomous-drive technology face is the speed and availability of wireless communications media. While 5G likely has the bandwidth to handle many tasks in real time, the rollout of efficient 5G with complete coverage has not yet occurred. Other slower media channels are not sufficient, except for data downloads or vehicle software upgrades, which can happen when the vehicle is stationary.
In addition, because the technology for autonomous drive is relatively new, components are changing on a regular basis, which further complicates testing. If the environment is not locked down, it’s nearly impossible to maintain valid data.
The end result of all this significant testing is that the amount of data that’s generated by the vehicles is enormous, easily into the terabytes. Trying to wirelessly download all that information can be a painstakingly long effort. To eliminate that long download period, Premio has come up with a solution that allows OEMs to simply take the data with them. In addition to eliminating the long wireless download, the solution maintains the safety and integrity of the data.
Premio’s RCO-6000 series of embedded computers are designed with a split architecture such that the memory subsystem can be removed and swapped for a new array to provide performance acceleration for inference and data capture workloads.
Called the cannister approach, the Premio RCO-6000 series EdgeBoost Node embedded computers enable quick and efficient data collection and transfer between the vehicle and a central repository, where the data can be collected, stored, and analyzed using AI workload information. The design that’s employed by Premio began as a custom project, but later evolved into a commercial product as more and more need for the technology arose. The RCO-6000-CML Series is the latest AI edge inference computer that uses Premio’s modular EDGEboost Node design to optimize performance acceleration and data capture for field testing autonomous drive applications.
NVMe SSDs Can Take the Shock
One key design element for the non-volatile memory (NVMe) cannister product is the ruggedization that’s needed for such an environment, while still having the ability to aggregate and store data very quickly. Using solid-state disks (SSDs) that are rated for high levels of shock and vibration, the data remains intact.
The architecture of the RCO-6000 series EdgeBoost Node embedded computers can be deployed in various configurations, depending on the specific application and what the end goal is. As shown in the figure below, the simplest configuration would be used just for data capture. Here, the canister would be removed, and taken to an external source for storage and analysis, usually combined with and compared to data from other instances (other vehicles or the same vehicle over time). The key benefit for this configuration is high-speed NVMe technology that provides reliable data capture that can be offloaded into a central location for even greater machine learning and AI workloads. In addition, the ability to support 100GbE network cards provides even greater bandwidth for data transmissions from the local device (edge) to a more central location (cloud).
The second configuration is for field testing, where the inferencing occurs on the spot with performance acceleration modules. Obviously, that canister is equipped differently than the model that’s just used to store information, as it handles lots of compute on the fly by dedicated PCIe lanes for hardware acceleration in GPUs, m.2 modules, and even an NVMe storage media.
The final configuration is the full-blown model that handles both inferencing and data capture. Keep in mind that in all three configurations, the canister can be easily removed so that the data can be brought back to the main processing unit for further analysis. In all three configurations, the architecture adds a physical security element, as the data remains within the canister, which can be stored and kept behind a physical lock and key.
As the figure shows, there are multiple configurations in which the RCO-6000 series EdgeBoost Node embedded computers canister can be deployed, depending on the application and the goals of the user. Each configuration includes the split architecture, allowing for easy data capture and removal.
Premio has already deployed a few hundred of the RCO-6000 series EdgeBoost Node embedded computers for a key OEM customer. Hence, lots of learning and has occurred from customer experiences in the data collection arena. In addition to the simplicity of transporting and safely storing data, it’s just as important to ensure the validity of the data, which is handled internally to the canister. The Premio experts are quick to admit that this design required rigorous testing during product development stage.
Note that the canister can be removed very simply by implementing an eject button. Premio provides a software utility to make this process easy for OEMs to include in their own user interface, which allows for OEM differentiation and customization with software development.
In practice, the canister can be connected with one of two different methods, either through a PCIe riser or through an NVMe hardware RAID controller. The former is used if the intent is to have a direct connection to the CPU’s PCIe lanes. Whereas, the latter approach would be used is hardware RAID is required.
While you may anticipate that such an approach would raise the power consumption to potentially unacceptable levels, that’s not the case with the RCO-6000 series EdgeBoost Node embedded computers. This notion comes from the fact that the embedded computer is likely powered by the vehicle itself. Through some smart power-efficient design, the Premio engineers were able to (mostly) negate that additional power consumption and stay true to an industrial-grade design by supporting wide-power voltage inputs.
Full-Function Embedded Computers for AI at the Edge
From a functionality perspective, the RCO-6000 series EdgeBoost Node embedded computers can be split into three main purposes (with the computers handling all three):
- Data capture: capture enough data to train an efficient model that’s capable of being deployed in a real-world environment. This requires all captured data to be written to the SSDs fast enough so no data is dropped.
- Test runs: Conducting test runs in the real world to test the models while simultaneously capturing data to see how efficient the models are. This requires a mixed of inference capabilities and fast storage.
- Final deployment: Once it’s a determined that a solution is mature enough, the final inference can then be deployed in mass production. This requires pure inference capabilities.
Scalable And Versatile I/O for Workload Consolidation
The RCO-6000 Series supports I/O brackets to enable high-speed connections with low-latency data transmission for advanced industrial applications at the rugged edge. With diverse modular configurations, the computer’s I/O flexibility allows workload consolidation for handling various digital and analog sensors. For example, daughterboard modules can be used to enable more I/O with GbE and USB, amongst other options.
High-Speed Network
A key challenge is to ensure that data can be captured fast enough so that nothing is lost. The RCO-6000 series EdgeBoost Node embedded computer handles that by including very high-speed NVMe SSDs and communicating over a 100-Gbit/s Ethernet network adapter.
Summary
One of the key deployment goals of the RCO-6000 series EdgeBoost Node embedded computers is to migrate the SSDs physically, without going through the arduous (and more common) method of forwarding data through a wireless network. Data can be offloaded in minutes by simply removing the canisters and, at the same time, new canisters can quickly be plugged in, allowing the vehicles to remain on the road, aside from the brief “pit stop.” Vehicle turn-around time to go back out in the field to capture more data is literally measured in (low single digit) minutes.
Premio’s in-vehicle computers are designed to operate in the harshest environmental conditions while delivering mission critical reliability in autonomous and remote edge deployments. The unique architecture significantly reduces down time, and is ideal for real-time local processing and inference analysis. Accelerate your autonomous-drive testing and deployments with Premio’s ruggedized in-vehicle canister-based embedded computers.