New Reference Design Simplifies Development of Silicon Carbide PFC Solutions
October 25, 2023
Sponsored Blog
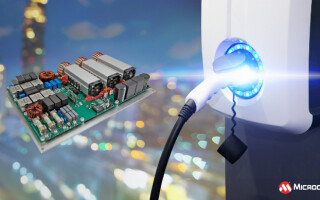
Developers of automotive, data center and power conversion systems face a number of challenges, including maintaining high efficiency across the output power range while minimizing line frequency harmonics to creating scalable, high-power designs with high power density.
Wide-bandgap Silicon Carbide (SiC) semiconductors solve these problems as part of PFC solutions that are particularly important in Hybrid Electric Vehicle/Electric Vehicle (HEV/EV) charger and high-power Switch Mode Power Supply (SMPS) systems.
SiC based PFC solutions can be brought to market more quickly and easily using a Vienna 3-Phase PFC Reference Design like Microchip’s 30 kW Vienna PFC that includes SiC power devices capable of delivering the highest possible efficiency. Microchip’s mSiC products are used on this reference design and includes Piecewise-Linear Electrical Circuit Simulation (PLECS) tool for simulating the circuit’s dynamic behavior prior to hardware design.
How SiC Transforms PFC Solutions
SiC technology enables new and improved PFC topologies. As an example, a SiC-based Vienna 3-Phase PFC offers important improvements over what can be done with a standard 3-phase boost converter including reducing voltage stress, lowering switching loss, increasing operating frequency and reducing common-mode emissions.
Microchip’s PFC reference design for implementing this Vienna 3-Phase topology includes 1200V mSiC diodes and 700V mSiC MOSFETs for 400V battery systems. These devices deliver high avalanche/repetitive Unclamped Inductive Switching (UIS) performance and 98.6% efficiency at 30 kW output. Other features include 3-phase 380/400 VRMS, 50 Hz or 60 Hz input voltage, 700V DC output voltage, and a 140 kHz switching frequency that reduces magnetics size.
The PFC reference design’s PCB layout is optimized for safety, low current and mechanical stress and noise immunity. It includes Microchip’s dual-core dsPIC33CH Digital Signal Controller (DSC) that is designed to support the power flow control of advanced topologies, as well as implementation of adaptive nonlinear algorithms for front-end PFC converters and isolated DC-DC converters. This DSC provides a digitally controlled current and voltage loop that reduces harmonics and eases upgrades, enabling it to be used for Processor-in-the-Loop (PIL) functionality during PLECS electrical and thermal modeling using ideal switches.
Other hardware tools for mSiC products are also available to help designers adopt SiC with Ease, Speed and Confidence. They include development/evaluation boards and reference designs for projects ranging from a 30 kW Dual Phase Shifted Full Bridge (PSFB) DC-DC converter, a 150 kVA 3-phase SiC Power Stack, 400/800VDC 10A-30A E-Fuse solutions, an SP6LI low inductance (<2.9 nH) power module, and a half-bridge digital gate driver for better controlling and protecting SiC MOSFET power modules.
SiC technology continues to demonstrate valuable benefits compared to silicon, and PFC designs are no exception. Our mSiC solutions, such as the 30 kW Vienna PFC, offer substantially lower voltage stress and switching loss compared with standard 3-phase boost converters, while also increasing operating frequency and reducing common-mode emissions. These designs are easier to build and bring to market using a reference design like Microchip’s PFC with high efficiency at the necessary output, a DSC for digital control, and PLECS modeling to thoroughly simulate the circuit’s dynamic behavior prior to initiating hardware design.