Extra Power Also Means Extra Heat
May 17, 2019
Blog
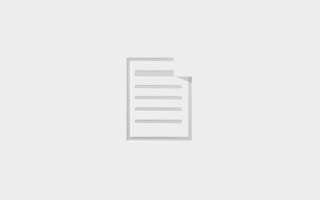
There are methods to determine how much of an issue heat is in your system, and some of them are quite complex.
Power is an important factor when you’re designing or acquiring a system for industrial or transportation applications. In many instances, particularly the transportation example, ample power simply may not be available. But power also translates to heat, and that is often a bigger sticking point than the power itself. Space can be a big constraint in, for example, transportation systems, which includes intelligent transportation, inflight entertainment, transport automation, and ticketing systems.
Oftentimes, developers and integrators don’t think about the heat issue until too late in the design process. The days of simply adding a first or second fan are long gone, as systems have become so packed with components, extra space is hard to come by, not to mention the reliability factor. In addition, many of today’s components, like the microprocessors, consume more power than in the past and hence throw off ample heat that must be dealt with.
Power dissipated by today’s CPUs runs from milliwatts at the low end up to hundreds of watts at the high end. And those lower power devices are often reserved for mobile/portable applications. Similarly, a system filled with solid-state drives (SSDs) can consume just a few watts, while a large, high-performance rotating disk drive could be 10 or 20 W per drive, or more.
Sometimes there’s an easy solution, like moving components around or putting vents in the proper places to provide good airflow. However, it is not always that easy and can be compounded by the fact that sometimes the system has to fit a fixed space and be sealed from outside elements. It’s more likely that you’ll need some dynamic allocation of resources, like turning things on and off when needed or not, to really solve the problem.
There are methods to determine how much of an issue heat is in your system, and some of them are quite complex. This could include doing a complete thermal analysis through simulation. Then there’s the brute force method of simply designing the system using good design techniques and hoping that everything works out OK.
The board designer can model for various thermal responses including all the modes of heat transfer, namely conduction, convection, and radiation. Radiation view factors, which are needed for radiated energy flow calculations, provide various options in terms of component selection and placement. In addition, the materials and components can be varied based on the ambient temperatures of the environment.
If you don’t consider yourself to be an expert of such thermal-analysis tools and techniques, or you don’t have the time and/or resources to implement the complete thermal analysis, then you should probably consult an expert. As an industry-leading provider of embedded computer solutions, WINSYSTEMS qualifies as that expert, as they invest significant engineering resources into testing, board layout, passive heat sinks, and other design techniques and parameters to produce systems that maximize reliability, longevity, and energy use.
One family of embedded computers that checks all the boxes in terms of low power and thermal management is WINSYSTEMS’ SYS-ITX-P-3800 series. The platforms pack an impressive feature set into a small form-factor Pico-ITX design (5.71 x 3.46 x 1.3 in.). The single-board computers are based on the Intel E3800 processor family, which provides the necessary CPU and graphics performance for most transportation-related applications, while allowing for dynamic power management.
A key specification for the SYS-ITX-P-3800 is its low power consumption, at less than 9 W in certain applications, which permits fanless operation in temperatures ranging from -20° to +70°C. It operates from a +12V DC input. The platform combines industrial connectors and I/O, including two 10/100/1000 Ethernet, four RS-232 serial ports, and four USB 2.0 ports.