LEVs Offer a Clean, Sustainable Transportation Option
July 06, 2023
Sponsored Blog
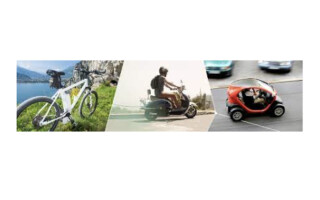
Light electric vehicles (LEVs) are part of the urban e-mobility megatrend, though not as commonly discussed in the media and technology sectors as EV passenger cars in the global setting. LEVs are generally smaller and lighter than traditional EVs, and are designed for personal transportation and include a range of vehicles, such as electric bicycles (e-bikes), scooters, motorcycles, rickshaws, and microcars (quadricycles).
LEVs make use of electric motors and are powered by batteries. They emit zero or near-zero emissions, making them environmentally friendly. They are also relatively affordable, especially when compared to larger electric vehicles. LEVs are often used as practical and convenient options for short-distance transportation, such as commuting to work or school, or running local neighborhood errands.
Don’t Confuse LEVs with EVs
As stated, the biggest differences between EVs and LEVs are their size and intended use, with EVs being larger and designed to travel much longer distances. In addition, EVs travel at higher speeds, making them highway legal in pretty much every country.
LEVs are becoming increasingly popular among younger generations and short distance commuters who are looking for eco-friendly and convenient transportation options. It is important to note that laws and regulations regarding the use of LEVs vary by location; some jurisdictions may require a license to ride/drive one while others may not. Interestingly, the regulations regarding LEV use can even vary between cities or regions within the same state or province. These regulations would likely include helmet laws, speed limits, registrations and licensing, and whether LEVs would be restricted to roads or dedicated travel paths like bike paths.
Key LEV Subsystems
The common subsystems across different variants of LEVs and the semiconductor components used within are:
- Motor inverter unit: power MOSFET, gate driver, microcontroller, and magnetic angle/current sensor
- Battery-management system (BMS): back-to-back power MOSFETs, battery authentication, cell balancing and monitoring IC, and microcontroller.
- HMI and control unit: handlebar control, and various buttons and microcontroller for instrumental cluster.
- Connectivity: Wi-Fi, Bluetooth, eSIM, and communication authentication IC
- Sensor system: radar for distance and presence detection, and user safety sensors
- Charging system: power MOSFET, gate driver, microcontroller used for ac-to-dc conversion and potentially wireless charging.
If we keep our focus on the motor control unit, products like Infineon’s OptiMOS™ 3/5 and StrongIRFET™ low- and medium-voltage power MOSFET families are suitable for enhancing this application. Features include a voltage range of 60 to 200 V and an ultra-low RDS(on), which are both required for high current carrying applications like LEVs. In addition, the newest OptiMOS™ 200 V power MOSFET is specifically designed for high-power LEV motor drive applications, offering a 6.7-mΩ RDS(on) in the TOLL package, providing the highest possible maximum power density.
The EiceDRIVER™ 160 to 200 V half-bridge gate driver IC is available in silicon-on-insulator (SOI), junction isolation (JI), and basic functional isolation offerings. These gate drivers are tailored for low- (24, 36, and 48 V) and medium-voltage (60, 72, 96, and 144 V) motor-inverter applications.
MCUs that are well suited for the LEV motor-control unit are the XMC™ XMC1400, XMC7000, TRAVEO™ II and AURIX™ families, depending on features and the desired functional safety class. The XMC1400 series is designed with a 32-bit Arm Cortex-M0, and can handle motor control in e-bike and e-scooter applications, with enough bandwidth remaining to potentially operate the LED lighting applications and HMI. Running at 48 MHz, it includes 128 kilobytes of flash, 16 kilobytes of RAM and offers two CAN interfaces.
On the highest end, the AURIX™ TC3x features TriCore technology suitable for up to ASIL-D applications. It pushes the performance level up a few notches by integrating up to 6 TriCore 32-bit processor cores running at up to 300 MHz. Additional features are LockStep capability, CAN interfaces, and embedded flash memory (up to 16 Mbytes).
Finally, for position sensing, Infineon offers its XENSIV™ TLE4961 integrated Hall effect latch that can operate from a 3.0- to 32-V supply, with all the expected protections built in. This can be combined with the XENSIV™ TLE5012B pre-calibrated magnetic angle sensor for steering angle measurement. Data communications are handled through SPI-compatible bi-directional synchronous serial communication (SSC).
Many other Infineon products can commonly be found in LEV subsystems, including CoolMOS™, CoolSiC™, and CoolGaN™ high-voltage power MOSFETs in the offline battery chargers and charging/battery swapping stations; AIROC™ Wi-Fi Bluetooth combo solutions in the connectivity module; PSoC capacitive sensing MCUs for the instrument clusters; and the OPTIGA™ Authenticate S security product for battery authentication.
The Future of LEVs
The future of LEVs looks bright, as there’s growing demand for convenient and eco-friendly transportation options. LEVs are a clean and sustainable transportation option, and the technology continues to improve, making them more affordable and allowing for longer travel distances with a more comfortable ride.