Customizing HMI solutions solves complex and varied needs in industrial automation
June 29, 2017
Blog
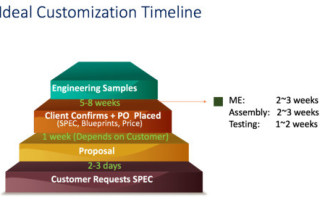
Industrial systems have been important enablers of increasing levels of automation functionality and complexity. These systems now feature advanced, standardized computing technologies and network...
Industrial systems have been important enablers of increasing levels of automation functionality and complexity. These systems now feature advanced, standardized computing technologies and network connectivity contributing to significant improvements in productivity, offering value-add features that can optimize factory floor operations.
While there have been considerable advancements in human-machine interface (HMI) technologies and systems that provide increased access to essential factory and operational data, there really is no one size that fits all when matching HMI features to industrial automation application requirements. That is because selecting the right panel PC design – from mounting options and screen size to the processor performance and I/O – becomes more and more important as automation capabilities are expanded to monitor and handle a larger variety of sophisticated tasks. In addition, there are specific regulatory compliance mandates and industry standards that need to be taken into consideration for market-specific applications such as in the energy, marine or food industries that make customization a must.
[Figure 1 | The needs of the automation industry are dynamic and diverse. Therefore, most companies prefer to procure an HMI or panel PC from a supplier that can offer them full customization, and better yet, with the lead time of an ‘off-the-shelf’ product, allowing them to meet their time-to-market goals.]
Ultimately, the ability to supply a completely customized panel PC expands the range of options for the design of lower-cost and higher-value industrial systems, which contributes to the viability and positive progress in the automation industry. This article outlines the most highly demanded features in the latest panel PC designs and how the evolution of HMI systems is best served when suppliers have the expertise to offer customizable options.
Customization meets automation trends
Analysts predict that industrial automation growth will be driven by Internet of Things (IoT) implementation across manufacturing industries. That will be coupled with increased R&D investments to satisfy rising demand for energy-efficient manufacturing operations, and growing emphasis on meeting regulatory compliances. As more companies look to implement IoT-enabled applications and Industry 4.0, there is greater demand for industrial systems and HMIs to integrate plant and factory floor operations with other business functions, such as logistics and customer service. Capabilities such as enhancing control and operational efficiencies, expanding interfaces and interoperability, networking, remote monitoring and increased access to data all provide a solid foundation to make IoT a reality.
Helping to further streamline manufacturing, HMIs also need to support the implementation of real-time data analytics into industrial automation processes. The shift toward smart factories connects previously isolated systems, making them the building blocks for the IoT. It is this high demand for interoperability of equipment that is driving the need for greater levels of technically advanced products.
Customizing an HMI design with next-generation processor and display touchscreen technologies allows companies to implement a connected, unified dashboard solution that helps them overcome the difficult and time-consuming task of manually analyzing and controlling production-line-level operations from varying platforms. Connected HMI systems are much more valuable when they provide the power to share data and monitor factory processes in real-time.
In addition, HMI systems are tasked with fulfilling demands for simplified, more intuitive operation. Breakthroughs in panel PCs include consumer-like, multi-touch interfaces.
[Figure 2 | Next-generation touch screens provide a high degree of accuracy and facilitate a much faster operator learning curve.]
For example, the use of projected capacitive (PCAP) touch panel technology is particularly well-suited for industrial automation. PCAP employs hardened or tempered glass that offers enhanced resilience to external environmental threats. This strengthened glass provides users with improved scratch, impact and shock resistance for increased durability.
The panel PC industry has progressed quickly, offering a marked increase in the number of devices that use touch panels and a broader range of new products and processes. Touchscreens offer streamlined and versatile control and functionality by replacing buttons and switches with software menus. This enhanced level of control also improves precision and accuracy in terms of production control. Furthermore, the increased computing performance available in today’s panel PCs supports complex and detailed data analysis and real-time control.
Supporting broader I/O requirements
HMIs that provide extensive I/O capabilities or expansion boards to facilitate customization of I/O are the features that allow today’s solutions to be the glue that controls machines and sensors, connections to the Cloud or to analytical software. Making use of extended I/O offered in today’s HMIs makes managing factory production more seamless and easier for the operator.
The increasing complexity of automation tasks and the amount of data to be accessed requires large-scale connectivity that connects every area of the organization. To support the broad range of interfaces found in industrial applications, today’s panel PCs must support connectivity matched to automation needs. Suppliers with advanced integration capabilities can provide comprehensive options for GbE; USB 3.0/2.0; and RS232, RS485, and RS422 communication ports. The growing use of wireless communications also makes it necessary that panel PCs support 3G/4G, LTE, WiFi, CAN, and RFID. Effective connectivity must also support a variety of edge devices where high processing power and expandable storage are needed to manage computationally intense data processing applications.
The growing popularity of using multi-screen technology requires that new panel PC designs provide support for video and graphics ports including Dual Channel LVDS displays. Certain designs may also necessitate application-specific expansions that can be handled by a single mini PCI Express socket now offered in newer panel PCs. Supporting expanding I/O needs, the latest panel PCs now offer broad operating system, performance, memory, and storage features.
Designed for longevity
The important characteristic that differentiates a commercial-grade panel PC from an industrial-grade panel PC in HMI applications is its ability to offer long-life operation, as most industrial systems operate non-stop for five to seven years or longer. This requires suppliers do extensive product testing to ensure extended operational life and reliability and to fully qualify an industrial-grade panel PC, which can take up to six months.
Customizing an HMI for the long lifecycles mandated in the industrial market is easier for a panel PC supplier that takes a modular approach. Modular panel PC designs provide configuration flexibility to meet a diverse range of application requirements that include the ability to select or upgrade processor performance, the display size, and type of touch panel technology, or to add to the backplane to satisfy the amount of I/O needed.
The brightness of the panel PC screen, as well as whether the system is fanned or fanless, are key issues in anticipating mean time between failures (MTBF) for an HMI system, where many customers request a MTBF of 50,000 hours. If the system is fanless and the screen’s backlight is more efficient, operators can enjoy a longer MTBF. For more robust operational demands, glass touch panels must meet additional shock and vibration requirements and provide comprehensive protection against dust and humidity or water. One solution is to embed the touch panel glass display into an aluminum casing. Another design recommendation for longevity is to seal the front of the panel PC, resulting in a more rugged industrial solution that offers a completely flat glass front surface. These options also give developers a range of solutions that meet various budget parameters. Additional choices enable more companies to adopt HMI applications for improved monitoring and control of factory floor data that helps achieve manufacturing productivity goals.
Depending on the application, panel PCs must operate in industrial temperatures that can range from -20 °C to 70 °C, which is much higher than the operating temperature in consumer products. Where reliable, non-stop performance is essential, it is best to select proven, rugged, and validated components that have been tested to meet protection against dust, dirt and electromagnetic compatibility (EMC). Standards-based solutions that also ensure technology investments are protected long term while cutting development costs for application-specific designs are a plus. OEMs and system developers are wise to seek experienced partners for panel PC customization.
Achieving market, application-specific goals
Greater cost effectiveness and continuous process improvements are possible with access to data that contributes to informed analysis in industrial organizations. HMIs that deliver a more comprehensive view of the production process can be used to bring in vital information from SCADA and manufacturing execution systems (MES) monitoring and control applications. These advanced HMIs make IoT a reality in the industrial sector, giving organizations the power to maximize productivity by installing the latest smart automation applications.
The high level of integration and standardized components found in the latest panel PCs ensures seamless and simplified interoperability with the other equipment on the factory floor and throughout the manufacturing organization. Panel PC multi-touch display technology features further enhance usability and the user experience making valuable single access points possible.
[Figure 3 | Custom panel PC design allows companies to better match application-specific needs and align with market trends. Selecting the right combination of I/O, connectivity, and processor features powerfully enables manufacturers to leverage the full benefits of IoT and Industry 4.0.]
Industrial markets often need to move quickly to implement automation systems that give them the right balance of performance, ruggedness, and functionality. That is why it is important to select a knowledgeable manufacturing partner with proven customization expertise that will help reduce risk and development time of interoperable and scalable hardware solutions.