Intelligent Sensor Module at the Edge Reduces System Power by 80%
February 21, 2023
Blog
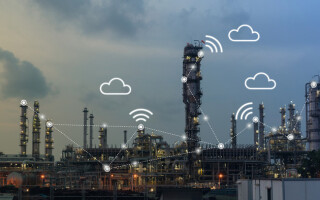
The latest Artificial Intelligence (AI)-based solutions at the edge of an industrial application rely heavily on real-time data from multiple sensors. Naturally, the features, capabilities, and types of sensors in a system depend on the requirements of each application.
Complex applications execute comprehensive algorithms that require data from multiple sensors. As the number of sensors in an Internet of Things (IoT) solution increases, so does the power consumption of the system. In addition, adding sensors increases the latency risk for applications demanding the system process data fast and efficiently.
To overcome these challenges and to extend the operation time of sensor nodes, embedding AI capabilities in the silicon die of the sensor is proving to be very effective. Moreover, this innovative approach addresses some drawbacks of cloud computing. The approach builds tiny sensors with intelligent computing power that can simultaneously run multiple algorithms and process sensor data with minimal communication to the external processor. Instead, the sensor lets the processor sleep until appropriate results are available in the sensor’s data memory. Then, the sensor notifies the external microcontroller of the available data that can be transmitted for use in target use cases.
The first generation of intelligent sensors included a machine-learning core designed to train AI models implemented inside the sensor. The model would generate results based on real-time sensor data. The second generation of intelligent sensors added embedded processing power to run several algorithms for AI solutions without latency. These sensors help extend the operation time of system modules with limited power budget.
Extending the capabilities of these second-generation intelligent sensors leads to a processor in a sensor, like that shown in Figure 1. This approach, which ST has pioneered in its Intelligent Sensor Processing Unit (ISPU), can simultaneously process multiple AI algorithms at the edge for critical time-sensitive applications that require real-time inertial sensor inputs.
Figure 1. Sensor containing an Intelligent Sensor Processing Unit (ISPU)
The latest intelligent sensors with an embedded processing unit are systems-in-package modules with a few sensors, an ISPU, and interrupt generators that can be programmed for different applications. These solutions also feature an on-chip sensor hub to allow additional sensors to be connected to the module.
This new intelligent module approach represents the start of a new era of powerful sensors that support real-time applications that rely on sensor data. The processing unit embedded with these sensor modules is an ultra-low-power, high-performance programmable core that developers can use for signal processing and AI algorithms while consuming significantly lower power than an external processor.
The true innovation lies in the optimized ultra-low-power hardware circuits for real-time execution of the algorithms for any wireless sensor node, ranging from small equipment or accessories to enterprise solutions for Industry 5.0, including anomaly detectors, asset trackers, or factory automation equipment, among others.
There is a wide discrepancy between the current consumption of an ISPU and a general-purpose Cortex-M0 microcontroller. Figure 2 shows that a six Degree-of-Freedom (6-DoF) sensor running with a sensor-fusion algorithm on a general-purpose microcontroller consumes 1000µA versus only 200μA with an ISPU, an 80% reduction in current consumption. We used the STMicroelectronics ISM330IS for this measurement [1]. The data from a 3-axis accelerometer and 3-axis gyroscope embedded in the intelligent sensor module drove the sensor fusion used in this measurement. There sensors were operated at 104Hz output data rate.
Figure 2. Current Consumption comparison between the ISPU and a general-purpose microcontroller.
Developers can best utilize this intelligent sensor module to run algorithms using internal and external sensor data. This module can connect up to four external sensors when operating in sensor-hub mode. Moreover, synchronizing the sensor hub trigger signal with the accelerometer/gyroscope data-ready signal ensures all sensor data are time synchronized.
Future Trends
Embedded AI inside a sensor offers several benefits, which include substantial savings of system power, along with much lower latency and bandwidth requirements. Coming generations of sensors will likely combine three major features to best leverage AI techniques. These are sensing, autonomous intelligence, and connectivity. Beyond these, sensors will provide raw data and have more advanced and powerful AI-focused capabilities for at-the-edge processing. AI-era sensors will also have the autonomy to decide which sensor data should be processed and used to deliver the outcomes of events taking place in real time. While offloading work from the main processor, this will further reduce latency and privacy breaches. Moreover, applications will use the outputs of AI-powered sensors to make decisions and take actions without the need for any additional external processing.
Reference