Accelerate Complex Chipmaking with Single-Device Tracking: A High-Performance Approach to Streamlining Data and Improving Control
February 24, 2022
Blog
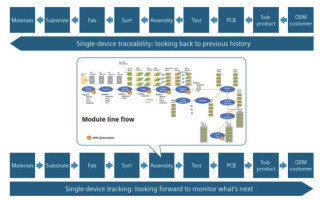
The new normal which swept in with the pandemic brought significant changes in the semiconductor industry that manufacturers and semiconductor fabs will likely be adjusting to for quite some time. Booming demand and prolonged shortages have put semiconductor production capacity at a premium. And demand is likely to outpace supply for the foreseeable future.
As a result, semiconductor manufacturers are feeling intense pressure to get more quality product out the door faster than ever. And customer demand for detailed traceability data is greater than ever. Chipmakers must deliver high quality and higher volumes of a more diverse product mix, which is made more difficult by processing that is often unique to each device in a lot.
Increasing product diversity increases the difficulty
Adding to the challenge is the increasing number of diverse applications that need complex multi-chip or multi-chiplet devices. This requires mixing products in a lot or chamber to perform different operations on each, which is crucial to maximizing utilization, especially for devices that go in small, inexpensive packages. Tracking the data for such complex products is no small feat, and chipmakers are finding that current tracking methods are no longer adequate to keep pace.
If you're making complex multi-chip devices, that's where single-device processing comes into play. Single-device tracking (SDT) is the most efficient way to manage production and deliver accurate data about every device and its processing history, especially when single devices are processed differently.
SDT has long been recognized as having the potential to solve traceability challenges. In fact, some chipmakers have attempted to take advantage of SDT’s potential by developing homegrown systems, but the reality is that these homegrown systems are incredibly complex to develop and notoriously difficult to maintain. Let alone having the ability to achieve the fast transaction times required to keep up with the demands of complex processes.
Most of the popular manufacturing execution systems (MES) available today are also not equipped to scale up to process the volume of data and the volume of complex transactions required. They typically slow complex operations to a crawl. It would take seconds, not the required milliseconds, for a typical MES to process data from each transaction for every device in a lot, which will not work for automated high-volume production.
To solve this issue, chipmakers really need a different approach that will transform SDT into a high-speed operation that will achieve significantly higher throughput.
It is essential to get more quality product out of the door faster. But how?
We understand that customers can’t sit and wait for chipmakers to build new production facilities to better meet their demands. There is an urgent need now for a practical, high-performance solution built into MES to support single-device tracking and traceability for high volumes and complex products at production speed.
Fortunately, today, newer high-performance solutions are available that optimize capacity, accelerate complex chipmaking, streamline data, and improve control. Also, with the integration of high-performance capabilities into MES, the semiconductor maker can control how each device goes through each process and record it at transaction speeds that were not previously attainable to provide high-speed single-device tracking and tracing.
Fig1. Modern semiconductor manufacturing execution system
Tracing vs. tracking
The difference between tracing and tracking is an important distinction to make in the current market, because the solutions needed for today’s customer demands require both.
Traceability is the capability to trace a device’s current status back to its point of origin.
To trace: you follow the completed path backward from its current point to where it began. For example, to trace where a device comes from on the wafer, you begin at the start of fab. Using maps, this is backward-looking genealogy.
Although customers demand traceability, which includes the exact process conditions that every device was exposed to at every moment in its manufacturing lifecycle, tracking forward motion is also essential for both data collection and semiconductor production. So, a semiconductor maker needs tracking in order to do processing on each device in a batch and also to provide all the data customers require.
Tracking uses maps to show what’s next for each individual device in the process.
To track: you follow the path forward from where a device currently is to where it should go next, like a map. Tracking allows different processing on each device at specific steps, allows the same processing at other steps, and records details and metadata associated with the individual die once cut and with the package once assembled. Using maps, this is forward-looking genealogy.
Firms making multi-chip modules (MCM), systems in packages (SIPs), central processing units (CPUs), and Insulated-gate bipolar transistors (IGBTs) need to track sub-devices. With varying batch sizes, tracking and monitoring each device through each step in the process is needed to provide complete traceability and genealogy.
Complex multi-chip devices can have low yields if assembly and testing are not fully process controlled. For multi-chip products, tracking and tracing with SDT are essential but the SDT must be connected to MES and equipment automation. And with the addition of high-performance technology, both tracking and tracing can be performed at the production pace needed by automated high-volume transactions.
Fig2. Single-device traceability requires single-device tracking, which can be complex at every step.
Why the need for higher performance?
For complex semiconductor products, current tracking methods can’t measure up. Sequential data writes for single-device tracking have become extremely inefficient. Companies can no longer afford for data processing to slow production and limit capacity. Nor can they afford to wait for parallel data writes, which bog down the application server, at the risk of not keeping data monitoring current.
When the MES is capable of performing high-volume single-device tracking the semiconductor manufacturer has more agility to control how each device proceeds through each process. This high-performance approach is the key to unleashing the many benefits of single-device tracking. Single-device tracking also allows you to include the metadata with single items. Even after a device is separated from the wafer, processed through splits and merges, binned and graded separately, it retains its history and can continue the process.
When you're tracking the overall device, and there is an issue of layers on layers where you can't reach the identifiers, you must have it mapped out clearly. This way you can still achieve traceability thanks to your map of what should happen going forward, so you can validate each step as it occurs.
Fig3. Relationships among carriers, lots and items are often complex.
A high-performance approach to rapid digital transformation
Anytime a parent loT needs to be broken down into 50 or more child transactions, the high-performance approach excels, because it uses bulk, not sequential, data writing. This digital advantage enables thousands of transactions to be written to the database using stored procedures. It performs these writes to the database rather than the application, so network chatter is minimized, but speed remains high. Using a flexible approach, it can write database actions, parameters, statements or values with extreme efficiency.
With so many high-performance capabilities integrated into MES, it’s easy to see how semiconductor companies can improve their ability to meet customer traceability needs, comply with SEMI standards, and increase throughput to a whole new level. And greater throughput is what every chipmaker needs today to get more quality product out of the door faster. Much faster.
Fig4. Standard speed of two-level start transaction comparison.
Alan is a 30-year veteran in the electronics and semiconductor space, having held executive engineering roles as well as directed strategy, planning, and development at OEM’s including Apple and Huawei.
From experience with directing startup teams of 5 employees to divisions of 200+ with a $50M+ budget, Alan is well equipped to assist partners with their digital transformation goals in the fast-paced electronics and semiconductor industry.
Alan is also accustomed to the challenges of advancing innovation with a deep technical background in telecommunications, electrical and software engineering, and hands-on expertise in cloud computing. He has driven key technology advancements within the EDA industry during his leadership roles at Mentor, Cadence, and Synopsys.
Alan is also active in professional organizations including IEEE, ACM and GSA.