IoT is showing up in the strangest places
August 26, 2014
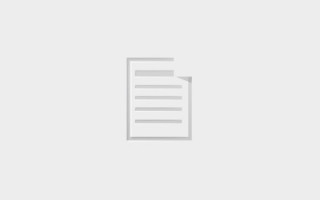
IoT is everywhere, and the networked world is moving ever more rapidly into an efficient, energy-saving, and fault-predicting environment - which is a...
IoT is everywhere, and the networked world is moving ever more rapidly into an efficient, energy-saving, and fault-predicting environment – which is a good thing. Wireless sensors may be the next IoT horizon (not unlike in-tire pressure gauges connected to an internal car system). Such devices are being designed into sensing systems that can predict the failure of inaccessible rotating components.
In Europe, designers are fitting wireless sensors into wheel bearings and gearboxes on railcars. The aim is to reduce catastrophic failure accidents or the cost of needless bearing replacements, without using unreliable hardwired monitoring systems operating in the harsh environment underneath a rail vehicle. Vibration energy harvesting powers the sensor systems, eliminating problems of predicting battery life or their replacement.
As rotating components degrade, they show symptoms that indicate the progression of the wear. The initial symptoms are vibration, followed by noise, temperature increase, smoke, and then failure. The railcar sensor systems provide vibration data for long-term failure prediction and temperature data for short-term monitoring.
An additional potential advantage of an encrypted, secure wireless system is that it can be designed for remote viewing, displayed on a web-based platform to enable convenient access by remote staff. Software translates the temperature and complex vibration data into a simple indication of the health of each component being monitored. Data can be displayed to provide a snapshot of the current state of health of the rail fleet, allowing trending data to be displayed to show the rate of degradation. Email alerts can warn an operator of any out of tolerance conditions, providing an early identification of a potential failure.
Fault prediction is a key technology for ensuring the safe operation of any piece of large equipment. Intelligent fault-prediction systems based on the Internet of Things will improve the product efficiency and scientific predictive maintenance is going to become vital for large key industries. Of course, in equipment monitoring and diagnostics, it’s important to distinguish between a sensor failure and a system failure. Careful design might involve measurement redundancy, state prediction, sensor measurement validation, mitigating drift in calibration, and sensor degradation.
In power plants, automated vehicles, aircraft, and other machinery, large numbers of sensors are already used for monitoring and control to enable operators and systems to perform supervisory control tasks. Diagnostics systems employing smart algorithms can use these sensor readings to assess a system’s state, detect abnormal states, and identify the root cause of that abnormal state so the operator can be advised about corrective actions to prevent significant damage to the system. Many of these sensor systems will be Internet-enabled to produce more efficient and reliable equipment.
British-born Alan Lowne is the CEO of Saelig Co. Inc., an importing distributor of test and measurement products. Before starting Saelig, he was an electronics design engineer for Eastman Kodak.