Laminates play a key role in the embedded product development cycle
September 16, 2015
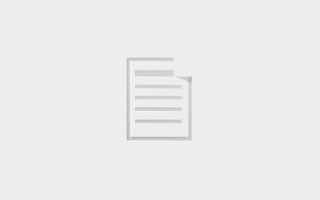
When we think of embedded products, we tend not to think too far down into the depths of the technology used to create them. The obvious elements are...
When we think of embedded products, we tend not to think too far down into the depths of the technology used to create them. The obvious elements are the ICs and their inherent hardware technology and the software in the form of application development tools and RTOSs that make these products functional. What’s rarely touched upon is the role of PCB laminates in embedded products. Laminates are ubiquitous in terms of all the products into which they’re incorporated, but also hidden in terms of their functionality and importance.
An upcoming Semico Impact conference, called Boards, Chips and Packaging: Designing to Maximize Results, will address many of these topics (and others). Two important points to keep in mind are that certain laminates are applicable for a number of different products; and certain laminates, because of the specific materials science incorporated into them, are geared toward one specific product or technology sector.
Today, there are four key product areas where materials are chosen: RF/microwave; the build-up market (cell phones and tablets); general electronics; and the high-performance (“big iron” Internet) products. For each of these markets, different aspects of these products drive the laminate evaluation and selection process. For instance, for RF/microwave products, two different pieces must be addressed – transmitters and receivers.
Transmitters are characterized by PCBs, which have high voltages and currents and receivers that never have high voltages or currents. From the broad perspective, the PCB elements, which drive RF/microwave product development, include low layer count, low loss (and, in some cases, dielectric breakdown voltage, or DBV), low cost, and hybrid designs developed with FR-4 laminate systems. What’s not important for these products (but are important to other product areas) are skew and the need for very thin dielectrics.
Included under the umbrella of RF/microwave technologies are the rapidly evolving autonomous automotive products. Today, most automotive applications are 0.005″ or 0.010″ cores. For these applications, FR-4 is increasingly being used for hybrid designs for cost control considerations.
Other application areas for RF/microwave products include LNB for satellite TV; numerous antenna applications; base stations; power amplifiers; and automotive radar systems. In terms of laminates best suited for RF/microwave products, Isola offers products such as I-Tera MT; I-TeraMT RF (capable up to 24-GHz-type designs and good for automotive designs); AstraMT (used for 77- to 81-GHz applications) and Terragreen, a halogen-free material.
In contrast to RF/microwave, products that affect the much bigger market areas, like cell phones and tablets, are driven by different technology and market factors. The most important market dynamic in build-up products is cost. This is and will continue to be the dominate market driver for these products.
In terms of technology drivers, build-up products require very thin dielectrics and spread glass for laser drilling and they aren’t usually concerned about loss or skew. For these products, Isola offers DE156, which is a halogen-free laminate and IS300MD, a recently introduced low-loss and low-DK product that’s also halogen free and is robust for build-up products, sequential lamination, and stacked vias (when they’re required).
General electronic products span a vast number of devices used for a variour purposes. These products have high layer count designs; they require lead-free assembly; the designs are CAF sensitive; they incorporate sequential lamination; they have stacked vias; and they must provide superior interconnect stress testing (IST) performance. Isola 370HR is a preferred laminate for these products. Other laminate choices include the company’s I-Speed, 185HR, FR408HR and IS415.
When it comes to high performance products which are most readily represented by the “big iron” Internet products, the predominant challenges, from a laminate perspective, include loss (represented as Tan(f)) and skew.
Laminate evolution
Somewhat similar to the Darwinian principle of the survival of the fittest, laminates have evolved as product needs have changed. In years past, the primary issues of concern included Tg (glass transition temperature); Er/DK (relative dielectric constant); Tan(f) (loss tangent); DBV (dielectric breakdown voltage); and water absorption. The lead-free movement has leveled the playing field such that Tg, DBV and water absorption characteristics are about the same across all of the new laminates so they’re no longer problems nor are they differentiators when it comes to laminate evaluation and selection. Some industry pundits will claim that er/DK continues to be an issue, but results from test boards built using new laminate products prove that this isn’t the case. As previously noted, for high performance products, Tan(f) or loss, continues to be a factor.
Tan(f) is important because it’s a measure of how much of the energy in an RF or high-speed digital signal is lost in a PCB’s dielectric. When a material is referred to as being “high speed,” it’s this property that’s being referenced. For all high-speed/high-performance products, the lower the loss, the better. In comparison to frequency, the higher the frequency, the more loss there is in any given material. This becomes an issue of concern in terms of how much of the energy in an RF signal is lost or absorbed in the PCB material.
In almost all instances, technology product drivers have resulted in changes to laminates. As a history lesson, we can examine the issue of water absorption. Two laminates were notorious for this problem—polyimide and Cyanate Ester (CE). Polyimide was primarily used in the aerospace industry as well as in down the hole in oil wells. Its primary benefit was its temperature characteristics. When Cyanate Ester came along, it was chosen because the Tg was 245 °C, so it was easier to process than polyimide. Unfortunately, both of these laminates suffered from the same problem—water absorption.
When laminates absorb water, they fail leakage tests. For polyimide, boards built with this material required conformal coating. This meant an extra step in the fabrication cycle as well as higher cost. And, although Cyanate Ester had a better Tg than epoxy-based laminates, it absorbed water at a greater rate than polyimide. For today’s high-speed digital product implementations, neither polyimide nor Cyanate Ester is a valid choice.
The lure of a new laminate
As with any other commodity, engineers and fabrication shops will often make the move to a new laminate because it’s reputed to be the best solution or because everyone else is using it so it must be good. Unfortunately, these selection criteria aren’t necessarily valid. Sometimes, the data available on the new laminate may not be current nor are its inherent properties well understood. In other instances, new laminates are changed as a matter of choice. The main take-away is that jumping to a new material just because it’s new or different isn’t always the ideal move.
On the other hand, refusing to consider new materials because they’re feared to be the wrong choice can be just as limiting. In evaluating new laminates, consider the following factors:
- Do I have a problem that the new laminate solves?
- Can my fabricator successfully build it?
- There are serious risks in terms of schedule and cost hits if this is the case.
- Will the material perform as specified?
- Is the material readily available?
Another consideration is the ability to access samples and manufacturing data from fabricators. It’s critical to know the fabricators ability to get selected materials from laminate suppliers. Where those fabricators fall in the food chain can be a critical part of your getting the material you need when you need it.
All in all, the evaluation and selection of the right laminate material is as important an element in the product development cycle as designing the product itself. Since most companies won’t have laminate experts as part of their core group of engineers, it’s important that these companies become educated as to the role that laminates play in the product cycle. The types of laminates best suited for their products and the characteristics of those laminates will be crucial in attaining a product that’s well designed and works right the first time.
Kella Knack has served as editor of Printed Circuit Design, LAN Computing, and ASIC&EDA magazines. She is also the editor of “Right the First Time, A Practical Handbook on High Speed PCB and System Design, Volumes 1 and 2.” She serves as a consultant to the industry.