Human out-of-the-loop manufacturing
June 06, 2014
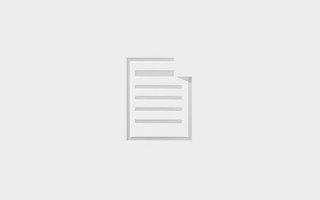
Increasingly complexity in product portfolios requires a new approach to manufacturing. Enter Product Line Engineering.
In an interview with Forbes magazine earlier this year, Wayne Usie of JDA Software discussed how omni-channel shopping and consumer expectations for product availability are rapidly transforming retail business models[1]. Usie explained how the evolving relationship between producers and consumers is effecting change in people, processes, and technology within enterprise, at times even resulting in the elevation of Chief Marketing Officers (CMOs) to leadership positions in company merchandising thanks to valuable insight into market trends. In the manufacturing sector, similar changes are also beginning to take hold.
To meet the expectations of industrial customers, OEMs are adding variation to their offerings, resulting in increasingly complex product lines. However, while more variation in product portfolios enables broader market coverage, it also creates challenges for typical manufacturing methods.
Traditional product line manufacturing begins with the Bill of Materials (BOM), and is driven by the philosophy that the right collection of parts must be assembled to exact a feature or capability from a given product variation. As a result, separate teams of engineers are responsible for selecting BOMs and developing product definitions for each manufacturable instance – from requirements engineering through architecture, development, and quality analysis – before passing the variation on to the factory line for production.
Where this model falls down in complex manufacturing is the human element, in that with each successive product variation the engineering assets required increase exponentially. In addition to being unscalable, these individual, product-centric silos of development also introduce the potential for error. Beyond the requirement to manually select BOMs for each variation during an intermediate phase of the overall manufacturing process, large teams of people are typically required to input data sets into spreadsheets or databases simply to identify and track components for various builds – all of this is in an effort to prevent manufacturing lines from coming to screeching halts, or worse, generating costly recalls. As production complexity and variation increase, new methodologies are needed to abstract and automate these processes.
The Product Line Engineering approach
An alternative to standard PLM practices is the advent of Product Line Engineering (PLE) approaches that “front load” much of the decision making to the initial concept stage of manufacturing. Within this PLE approach, product marketing personnel are tasked with creating a “feature catalog” from which product engineering defines a “bill of features” that automatically computes necessary BOMs, as opposed to engineers developing BOMs later on that are tailored to particular features. Not only does this methodology create transparency and centralize knowledge of feature definitions, but it also minimizes labor-intensive and error-prone BOM creation and component tracking, as feature profiles can be easily selected for different product variations.
An example of one such manufacturing architecture is the Gears Product Line Engineering Tool and Lifecycle Framework from BigLever Software, Inc. located in Austin, TX (www.biglever.com). As shown in Figure 1, the Gears product configurator maps out the features defined for different variations of a product, with the line engineers then designing to specifications outlined in the bill of features. As a Java-based software solution, Gears is Operating System-agnostic (OS-agnostic) and bridges with other applications to streamline development in a non-disruptive manner.
A pragmatic product future
Automation is no longer a luxury within industry; it is a requirement. Developing complex product lines now demands a pragmatic approach to manufacturing that can abstract processes to improve operational efficiency. Product Line Engineering is one step in that direction.