Your Senses Deserve More: Safer Driving with High-Definition Haptics
November 04, 2024
Blog
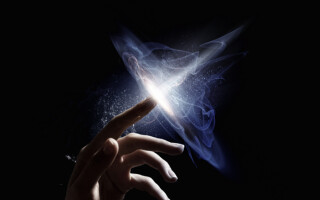
Since the introduction of large-screen center console displays in the Tesla Model S back in 2012, traditional mechanical vehicle controls and switches have increasingly been sacrificed in favor of integrated touch-screen user interfaces.
This approach has all the benefits of a software-based Human Machine Interface (HMI) and allows for clean interior design concepts, however, there are drawbacks to the growing consolidation of critical vehicle controls into center-stack touch-controls, which requires users to be engaged and looking at the display during use.[1]
Research shows that reaction times for drivers can increase by more than 50% when using touchscreen-based infotainment systems.[2] In the future, vehicle testing bodies such as Euro NCAP are planning to allocate points in their rating system for discrete buttons that control critical vehicle functions like hazard lights, to reduce cognitive load for the driver and keep their eyes on the road.[3] This presents a set of challenges for vehicle makers who have already replaced physical controls with touch-screen HMI:
- Users have become familiar with this “software-defined” approach. Wrestling them away from the touchscreen experience they know and love from their smartphone will require an equally immersive solution to change user habits.
- Reverting to mechanical buttons may go against the wishes of cabin designers, with either no practical space available to locate additional switches, or no desire to blot the landscape of clean minimalistic “shy tech” interiors with “button islands.”
- Given the cost pressures faced by the industry, with EV adoption slowing and fierce competition, the additional cost of adding discrete control elements might be difficult to justify versus other competing features.
Despite all these headwinds, there are technologies available that present a solution to these challenges.
Software Defined Vehicles
Some vehicle makers have already implemented touch controls, however, the transition from mechanical controls to virtual buttons has not always been smooth, with poor market reception of cost-optimized designs which were using the best technology available at the time. Automotive design cycles of up to 5 years also mean that new vehicles often lag consumer devices in terms of user experience, because the hardware is already out of date by the time the vehicle hits the car showroom, and the software is costly to update and maintain.
Car makers are investing heavily in this area and the advent of software-defined-vehicle architectures is allowing development and finalization of user-facing features on an accelerated cadence, much closer to the start of vehicle production. Over-the-air (OTA) feature updates also allow for optimization once the car is on the road, with new capabilities or performance tweaks to get the best out of the underlying hardware design.
As vehicles shift from being a product you buy to a device or service you use in a connected mobility ecosystem, users are demanding digitally native control interfaces to interact with their favorite applications - similar to what they would expect from a smartphone user experience. The recent introduction of a camera button on the smartphone is a sign of trends to come in automotive. Users want to have tactile control for taking pictures with smartphones so they can keep their eyes on the subject. The same applies in cars: drivers want tactile controls so they can keep their eyes on the road and their hands on the wheel.
Applying software-defined concepts to interior controls unlocks a whole new world of possibilities. Replacing simple mechanical buttons with a single function button click adds little value to the overall system. Virtual programmable surfaces on the other hand, can leverage centralized HMI processing to re-configure haptic feedback on the fly in different driving contexts. This increases the functional depth of each control button and reduces clutter which might otherwise lead to driver distraction.
This flexibility may help car makers adapt to safety guidelines for driver controls, such as those proposed by NCAP. With a software-based approach, regional variants can be easily managed, taking into consideration local market preferences for different types of control feedback or safety regulations and guidelines.
Anatomy of a Click
[i]As the title of this article suggests, we deserve more when it comes to recent haptics implementations in vehicle controls. This is not necessarily due to a lack of suitable technologies for automotive use, but rather down to the complexity of implementing consumer-level haptics performance in automotive applications which often have very different physical robustness requirements and associated use cases.
Figure 1 – Types of Mechanoreceptors
To understand how we can make the haptic experience safer and more immersive, we first need to understand the anatomy of haptic feedback. Starting with the biology, our human touch system has specific mechanoreceptors that can perceive vibrations up to 500Hz (RA2 Pacinian receptors) and textures when moving fingers across a surface (see Figure 1). The perceived strength or sharpness of these sensations is directly related to the way in which the actuator (the mechanical device which generates the feedback) can stimulate these receptors.
Figure 2 – Anatomy of a Click
The two key components of a click are the haptic strength or power, and the haptic quality (see Figure 2.) Not all haptics actuator technologies are natively capable of creating short, powerful click effects.
In fact, many systems on the road today employ open-loop haptics circuits, which send “blind” voltage pulses in one direction to the actuator. During design, these pulses are optimized to get the best performance possible by measuring the haptic feedback acceleration curve in the lab, and modifying the pulse waveform until the desired effect is achieved. Whilst this might work in a lab environment, in the real world, part-to-part variation in production and temperature variations in the field result in disappointing performance, which can result in a low-quality, undefined haptics feedback experience that is not using the full capabilities of our mechanoreceptors!
High-Definition Haptics
To generate a crisper, more defined feedback, similar to the experience users would expect from a laptop trackpad or smartphone, a method called Sensorless Velocity Control™ or SVC can be employed to generate HD Haptics effects that give our senses the experience they deserve! SVC uses advanced algorithms to monitor signals coming back from the actuator as it moves, to continuously adjust and compensate the drive and braking pulses to achieve the best possible “click” response. (See Figure 3.)
One of the many benefits of SVC is that it automatically applies overdrive and breaking to the click waveform pulses to achieve the customer's desired acceleration specification. It can also be used to enable consistent performance across manufacturing tolerances in high-volume production, and different ambient operating temperatures in real-world applications. This is especially important when control surfaces might have several different actuators, or the cabin has multiple control surfaces which must exhibit the same signature click. Making sure this click stays the same over the lifetime of the vehicle is also important. Actuators can age over time, resulting in changing load impedances, mechanical stiffness, and resonance frequency. This leads to poor click responses for active haptics systems employing open-loop designs. SVC can diagnose the health of the actuator over time and compensate for these aging effects by applying smart closed-loop signal processing to the driver output waveform, keeping the click “crisp” for automotive mission profiles.
Figure 3 – Sensorless Velocity Control (SVC)
From a commercial perspective, SVC also enables the use of smaller or lower-cost actuators without sacrificing performance, but most importantly, it enables a better overall user experience by making touch input feedback more natural and easier to perceive, reducing the cognitive load on the driver.
Simplifying Haptics Control
Figure 4 – Comparison of Haptics Subsystem Implementations
Implementing high-definition clicks using closed-loop control is not simple and requires complex systems that combine feedback sensors, advanced software algorithms, and low-latency DSP processing.
Figure 4 compares these traditional “discrete” haptics implementations to the benefits of the Cirrus approach using a 1-chip integrated driver solution, which combines all the necessary circuitry to drive a range of different actuator types effectively. It also implements SVC using on-chip voltage and current monitoring to actively sense and manage actuator performance, regardless of part-to-part variations in production and changing ambient operating temperature conditions.
In addition to the SVC capabilities, the CS40L5x series offloads low-latency waveform generation & synthesis tasks from the host processor to simply haptic effect generation. Without the need to store and stream hundreds of different haptic waveforms from memory, the host processor can use higher-level scripts to generate sequences of haptic effects for different UI contexts. This is a big benefit for resource-constrained devices, allowing the use of lower-cost microcontrollers, reducing software complexity, and speeding up development.
Future Possibilities
Existing active-haptics system implementations for control switches typically make use of a microcontroller running a local software stack, combined with discrete amplifiers to generate the voltage pulses that drive the transducer. The haptic effects are typically developed by the switch module supplier, based on guidelines from the vehicle manufacturer and “baked-in” to the switch software for the life of the vehicle. OTA software updates make it possible to re-configure the haptic effects, but this would require a change request to the switch module supplier to make the necessary software changes.
By leveraging advances in vehicle communication networks such as 10Base-T1S and remote-control concepts under discussion inside the Open Alliance[4], vehicle makers can choose to replace the local microcontroller in the switch unit with a remote-control software driver running on a central vehicle computer. The MCU in the switch unit is replaced with a simpler network transceiver with integrated I/O, connected via I2C or SPI to a haptics driver, as shown in Figure 5.
Because the Cirrus Haptics Driver integrates all the necessary signal processing and waveform generation functions to create a haptics event, no other local microcontroller is required.
Figure 5 – Remote Control using 10Base-T1S
Making the Switch
Cirrus offers a range of hardware and software tools to help engineers measure and evaluate the performance of the features discussed in this article, including SVC, in an integrated development environment. You can get more information about the Cirrus Logic CS40L5x haptics driver IC family and our comprehensive prototyping support services by contacting automotivehaptics@cirrus.com or your local Cirrus Logic sales representative.
Authors
Peter Hall - Business Development Manager, Automotive
Jorge Reynaga - Product Manager, Haptics
Miguel Sanchez - Applications Engineer, Haptics
[1] Matthew Avery, director of strategic development at Euro NCAP, told The Sunday Times newspaper: “The overuse of touchscreens is an industry-wide problem, with almost every vehicle-maker moving key controls onto central touchscreens, obliging drivers to take their eyes off the road and raising the risk of distraction crashes. Source: https://etsc.eu/cars-will-need-buttons-not-just-touchscreens-to-get-a-5-star-euro-ncap-safety-rating/
[2] Interacting with Android Auto and Apple CarPlay when driving: https://trl.co.uk/publications/interacting-with-android-auto-and-apple-carplay-when-driving
[3] See NCAP Rating Plan for 2026-2028 Page 8 under Driver Engagement: “Driving Controls is a new assessment element covering the ease of using the most important vehicle controls.” https://www.euroncap.com/media/79890/euro-ncap-rating-review-2023.pdf
[4] TC18 – Remote Control Protocol, Open Alliance Website: https://opensig.org/tech-committee/tc18-remote-control-protocol/
[i] “Properties of Four Types of Mechanoreceptors” downloaded from: https://mycourses.aalto.fi/pluginfile.php/910764/mod_resource/content/1/04%20-%20Activation%20Point.pdf originally printed in: Sensation and Perception, Seventh Edition Paperback – by E. Bruce Goldstein (Author)