Motor Drive Challenges in Service Robotics Design
February 08, 2019
Story
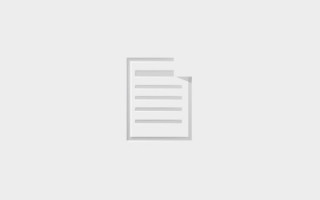
A look into power MOSFET and package technologies for best performance of drives in service robotics applications.
A perfect storm of circumstances such as market readiness, technology maturity and delivered value is fostering the spread of robots in industrial and the consumer segments. Important contributors to this development are advances in semiconductor technologies that allow for mobility with excellent power efficiency and small size. This article looks at how power semiconductors allow more effective, reliable and multi-dimensional service robot designs.
Small size to fit within work/living environments is a priority in most service robot designs, as is energy efficiency to yield long battery life. Both goals also call for excellent thermal management for reliability both in industrial applications and to provide a positive consumer experience in terms of product lifetime.
After reviewing how power electronics fit in the overall architecture of robotics systems, we will turn to the use cases and benefits of different drives technologies for robotics with a focus on MOSFETs, packages and high switching frequency solutions such as gallium nitride (GaN).
Common system architecture in service robotics
The most common architecture for robots features a central processing unit (CPU), power/battery management unit, battery chargers, wireless communication (COM) modules, human machine interface (HMI), sensors, and drives modules (brushed and brushless motors), as illustrated in Figure 1. While some robots do not include all components discussed here, this is a good system overview and identifies areas where power semiconductors are tightly integrated with microcontroller and even security/authentication components
While the main CPU/MCU is the central brain and carries most of the intelligence of the system, a typical design will include additional MCUs related to the power architecture. These execute instructions, and report status to the main CPU.
Most service robots are battery driven to enable flexibility in movement. These robots feature on-board chargers for direct connection to the AC grid. A charger is included in the robot to generate a high voltage DC level that the power management unit will process further down. Wireless charging capability is particularly useful for systems required to work continuously and so need to charge while operating.
A power/battery management unit takes care of the overall condition of the battery (including health and safety aspects), and also protects it against system overvoltage or overcurrent. In the battery module, security – including authentication– is a key factor to be considered. Batteries also rely on general purpose microcontrollers to implement auxiliary functions like metrology or monitoring in the battery system. Apart from a battery management unit, a power management unit supplies power to the different components in the robot by controlling the required voltage rails – 12V, 5V or 3,3V – in a stable manner for the rest of modules. This may be accomplished with buck converter controllers or linear regulators (fixed and adjustable).
Power rails of course drive the multiple components seen on the left side of the block diagram. This component mix includes:
- - Communications modules, usually Wi-Fi or Bluetooth-based, support connections to other robots or control units. In many cases, a local controller is responsible for the communication process, working as a gateway between the robot’s main controller and the external world.
- - Human-machine interfaces are achieved with either a simple display or even a high-resolution display, as well as LEDs used to provide information or feedback to the user. If the robot is provided enough intelligence to be able to interact verbally with the user, audio in and voice output devices are required.
- - Sensor systems are increasingly varied. Position sensors (Hall sensors, encoders), and speed, angle or current sensors are used in drives. If the robot needs a precise understanding of its environment, further types of sensors are required such as radar sensors for motion sensing (distance and direction), barometric pressure sensors, and 3D image sensors for object recognition.
Finally, drive modules are part of a common system architecture. When accurate positioning, high speed or quiet operation are required the designer will choose a brushless DC (BLDC) motor together with a set of position sensors. Otherwise, if a low performing motor control (slow, low accuracy) is enough, the designer will select a lower cost brushed motor. There also are numerous applications in which both brushed and brushless motors co-exist to meet performance and cost efficiency goals.
Addressing switching and conduction losses
A way of optimizing the battery life in robots is to increase efficiency of the various required motor drives and thus reduce power losses. Both conduction and switching losses are in focus. Continuous innovation to improve figures of merit of MOSFETs with special focus on reduced RDS(ON) (drain to source ON resistance) and gate charge (capacitance) of the MOSFET contribute to designer’s ability to minimize both types of losses.
Depending on the control method, different losses are observed. When synchronous rectification is used, the low-side MOSFETs are turned on if the current freewheels through their body diodes. This dramatically reduces the conduction losses of the body diode (PLoss = IF x VF), as the RDS(ON) value of the MOSFETs gets lower and lower with new generations. However, the low-side diode is still one of the main sources of losses. To address this issue, MOSFETs such as the Infineon BSC010N04LSI have integrated Schottky diodes that reduce the forward voltage, therefore minimizing the power loss in the diode.
Figure 2 shows a power loss breakdown measured in a three-phase inverter using block commutation PWM (6 steps) with synchronous rectification and a 18 Vsupply voltage. The selected MOSFET for the comparison is BSC010N04 in both LS and LSI (integrated Schottky) versions. The candle diagram clearly shows that both conduction (‘Cond-‘) and switching (‘SW-‘) losses have an important role in both high-side (‘HS’) and low-side (‘LS’) MOSFETs. There are three main findings related to this:
- Switching losses are negligible in the low-side MOSFET as soft-switching is granted.
- Conduction loss in low-side diode is by far the most dominant source of losses.
- LSI (Fast Diode) version of MOSFET with integrated Schottky diode reduces the conduction loss by approximately 25 percent. This reduction depends on system conditions such as current level.
Switching losses are strongly connected to switching frequency. Common frequencies in robotic inverters range from 10 kHz to 40 kHz. The higher the switching frequency, the higher the losses. Best-in-class low RDS(ON) and low-charge MOSFETs significantly reduce both types of losses; however, losses are inevitable and also heat will always be produced in the power switches. Thus, thermal management is one of the key challenges in drives designs. This is particularly true when considering high power density devices, for example in small robotic arms.
Infineon’s DirectFET™ package, shown in Figure 3, is a dual-side cooling package with direct connection between the metallic package and the silicon die inside that directly connects to the PCB on the bottom side, minimizing thermal resistances to the exterior. These packages efficiently distribute heat from the junction to the bottom of the PCB, and from the top through the metal package into the air or an optionally used heat sink for more rigorous cases. The package lowers thermal by more than 50 percent compared to a D2Pak device. It has an extra low profile that is ideal for space constrained designs like those found in robotics applications and battery packs.
High switching frequency drives solutions
Engineers now can take advantage of the properties of gallium nitride (GaN) devices in their applications. Lower on-resistance results in lower conduction losses than silicon alternatives, less capacitance resulting in fewer switching losses, and improved body diode reverse recovery make GaN devices an excellent choice for high switching frequency power applications. Increasing the switching frequency can help to improve the performance of a drive by reducing, for example, the torque ripple. In other applications such as power supplies, this technique can be used to reduce the size of magnetic components effectively.
As switching frequency increases, controllers have to be adapted. PWM resolution must be considered to ensure that the complete loop stays within the required accuracy. Microcontrollers like XMC4100 family have high resolution PWM modules to support high resolution loops even when switching frequency increases. Also, the processing capability of the microcontroller must be considered when switching frequency raises. Assuming a cycle-by-cycle control, less time is then available to finalize new duty cycle calculations. Infineon offers a broad portfolio of controllers with a wide range of performance from XMC1000 family ARM®-Cortex™-M0 at 32 MHz to XMC4000 family ARM®-Cortex™-M4F at 144 MHz and AURIX™ when a higher level of functional safety and performance is required. Increasing the control loop execution frequency leads to better dynamics of the motor, resulting in more accurate control.
More demanding motor control applications are supported with MCUs featuring a MATH co-processor dedicated to motor control applications like XMC1300 or XMC1400. The MATH co-processor includes both a CORDIC unit for trigonometric calculations and a division unit. This co-processor reduces the execution time of control loops compared to standard implementation (hardware versus software calculation), as seen in Figure 4, which compares the execution time of cosine and division functions - often utilized in motor control algorithms like field-oriented control (FOC).
Summary
The design parameters of drives for the next generation of robotic solutions and devices are challenging. Engineers can choose from different semiconductor solutions to fine-tune their designs and meet technical parameters such as switching frequency and thermal resistance. To build a well-optimized system, designers have to minimize the losses – both conduction and switching losses – and optimize the thermal management.
MOSFETs with integrated Schottky diodes can reduce the forward voltage resulting in minimal power loss in the diode. Engineers can also take advantage of new package designs like DirectFET™ that offer optimized thermal management. Finally, new wide bandgap solutions like GaN devices will establish the foundation of higher switching frequency drives, helping both in the accuracy and footprint aspects.
More information about the range of Infineon devices for drives and robotics related solutions is available at www.infineon.com/service-robotics.