Autonomous Vehicle Timing Means MEMS
February 13, 2019
Blog
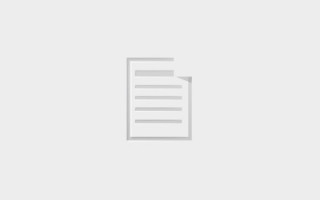
Engineering is always about tradeoffs, but autonomous vehicles are pushing that to the limit with conflicting requirements.
Engineering is always about tradeoffs, but autonomous vehicles are pushing that to the limit with conflicting requirements.
- These vehicles will generate copious amounts of data, both from the various forms of vision sensor as well as environmental sensors detecting temperature, pressure, and other critical parameters.
- Communication will be constant, using automotive Ethernet internally and 5G to talk to the world.
- They operate in an unforgiving environment, with constant vibration and shock. Temperatures can be extreme, both due to external weather and the internal engine temperature. Temperature changes can be rapid, both externally, with quick weather changes, and internally, for example, when the engine warms up. Moisture can materialize at any time due to rain or to driving on wet pavement.
- Automobiles put lives at stake. A car should always work, but if something goes wrong, it has to be able to behave well as it moves into a safe state.
- Cars are a consumer item; manufacturers are extremely cost-conscious, even as they demand high performance from their electronics. Chip footprints must be small to save area, and electronics must be manufacturable with high yields to keep prices in range.
One common thread runs through all of these requirements, and it’s one we usually take for granted: timing. In order for everything to work in lock-step, even if things go awry, those clock signals must operate without fail. Timing is now mission-critical, more than it has ever been before, placing extreme demands on the sources of that timing.
While quartz has been yesterday’s go-to for timing, now and into the future, MEMS technology provides the only timing sources robust and reliable enough to be used for autonomous driving.
It’s Brutal Out There!
Your cell phone may be complex, but compared to self-driving cars, it has it easy. It gets to travel in your pocket or your purse; if it’s shocked by a fall, it may not survive – and that’s what we (sadly) expect. Cars aren’t nearly so fortunate. Rough roads, speed bumps, and – heaven forbid – unplanned encounters with other vehicles or stationary objects will rough up the internals of the car – and those internals are expected to keep running. Temperatures – and temp changes – can be extreme. Electromagnetic interference, if not managed, can prevent reliable communication.
If anything fails under these harsh conditions, then the car must enter a safe state. But none of that can happen if the timing that coordinates everything fails as a result of environmental stress. This is a big part of what gives MEMS timing an edge: MEMS timing sources are much more robust than quartz sources. For example, MEMS timing devices from supplier SiTime can provide stability of 0.1 ppb/g (as compared to quartz’s 0.5 ppb/g). They can handle 50 kg of shock and 70 g of vibration. They survive temperatures (and rapid changes) from -55 to 125 °C (a wider range than quartz can deal with). And, with programmable edge rates (± 0.25 – 40 ns) and spread-spectrum capabilities of up to 4% (± 0.25%) – features unavailable with quartz, MEMS timing can reduce EMI by 17%.
Timing must also remain reliable over time. MEMS timing has proven itself to be extraordinarily reliable. Statistical measures of failures over the lifetime of a system have fallen below 1.6 defective parts per million (DPPM), with a failures-in-time (FIT) rate less than 1 (over a billion hours, or over 114,000 years mean time between failures, or MTBF). Using quartz leaves you with 20 – 50 DPPM and less than 50 million hours between failures. MEMS also suffers no activity dips, nor does it have issues with a cold start – both perennial quartz challenges. MEMS sources can also meet the AEC-Q100 requirements for testing, as compared to quartz, which meets only the AEC Q200 requirements.
Communication Within and Without
The automotive industry has settled on a form of Ethernet to handle communication within the vehicle. That includes functional communication both within and between various domains – the powertrain, the chassis, and the center stack, for example. Data rates may be at 10, 40, and/or 100 Gbps. Based on the Ethernet we’ve known in our home and office networks, it addresses several concerns that “normal” Ethernet raises.
- It has less RF noise, reducing interference between signals.
- It provides for microsecond latency for requesting and transmitting urgent sensor and other data.
- Bandwidth can be allocated to specific streams with specific latency requirements.
- Timing can be synchronized between components to allow, for example, simultaneous sampling of data.
5G, meanwhile, is poised to carry the burden of communicating externally to anything in range: other vehicles, local infrastructure, and cell towers. This “vehicle-to-X,” or “V2X,” system then takes on the very tight timing that 5G imposes: 10-ns latency on each end of the network, and frequencies into the double-digit gigahertz range.
This communication will encompass both the super-critical, like conversations between cars about who’s going where when, and the convenient, like streaming music, real-time or not. All must work reliably to ensure a safe, comfortable ride. MEMS timing sources provide the frequency and jitter performance necessary to keep both the internal and external networks running. Frequencies above 700 MHz, with stability at ±0.1 ppm (from -40 to 105 °C) or ±20 ppm (from -55 to 125 °C) support this performance.
By comparison, quartz clock sources come with fewer frequency options, all in large packages. They manage stability of only ±50 ppm from -40 to 125 °C. They also suffer from so-called “activity dips” and other anomalous behavior, making them less reliable in safety-critical applications.
Shrinking the Timing Footprint
Finally, the less space required by the timing sources, the better. That said, you have options depending on your priorities. For the ultimate in small packaging, MEMS is available in 2.0-mm x 1.6-mm DFN packages. If lead inspection is critical for less expensive manufacturing, then timing can be obtained in SOT23-5 packages.
MEMS timing also requires no load capacitors, and a single driver can drive multiple loads. Both of these characteristics stand in contrast to quartz. And quartz, by its very nature, must use larger packages.
Automotive Designs Turning to MEMS
Automotive applications are among the most demanding imaginable, especially when you consider that the pricing of chips must be compatible with consumer price points. They operate under extremely harsh conditions; they must maintain reliable communication inside and out; and they have to be able to collect, process, and distribute huge quantities of sensor data in order to keep functioning efficiently and safely.
The timing that controls all of these interwoven systems must be robust and reliable. It must provide high performance while creating the smallest possible footprint. These are all characteristics of MEMS timing. The transition from quartz to MEMS will be led, in part, by our eagerness for vehicles that will take us from here to there safely while we sit back and let the car do the driving.
Piyush joined SiTime in 2008 to pursue the vision of transforming the $6 billion timing industry. At SiTime, Piyush and his team are responsible for helping SiTime create and launch the industry’s best timing products, ensuring that customers have an exceptional experience with SiTime, managing the product lifecycle as well as all aspects of marketing communications and industry analyst relations. Since 2008, Piyush has helped grow SiTime from a pre-revenue startup to a fast-growing leader with over 90% share of MEMS timing.
Previously, Piyush was the VP of Marketing at Ikanos Communications where he was a key member of the team that drove Ikanos to success and a public offering. He launched his career at Cypress Semiconductor in applications engineering and marketing, where he defined and launched several category-leading products that generated hundreds of millions of dollars in revenue. Piyush earned Bachelor’s and Master’s degrees in Electrical Engineering from the University of Bombay and the University of Michigan respectively, and an MBA from the University of California, Berkeley.