Optimizing EVs with SiC and GaN Semiconductors
November 06, 2024
Sponsored Blog
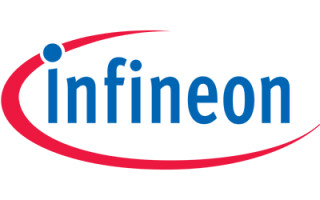
Electric vehicles (EVs) contribute to a greener, more sustainable future by eliminating NOx, CO2, and particulate matter (PM) emissions. To further optimize energy efficiency, performance, and range, many EV manufacturers adopt a holistic design approach, incorporating Wide Bandgap (WBG) semiconductors and focusing on the seamless integration and interoperability of key vehicle systems.
This article reviews the technical operating parameters and advantages of compound WBG Gallium Nitride (GaN) and Silicon Carbide (SiC) semiconductors. It also discusses the role of SiC in drivetrain power and traction inverters, highlighting optimization, consolidation, and emerging applications. Lastly, the article explores how SiC could further improve sustainability and reduce raw material costs by enabling EV manufacturers to refine externally excited synchronous machines (EESMs) and potentially replace permanent magnet synchronous motors (PMSMs).
Driving Higher Switching Frequencies
Featuring a larger band gap compared to conventional silicon, GaN and SiC safely operate at higher voltages, temperatures, and switching frequencies. Many automotive manufacturers use WBG semiconductors to optimize the energy efficiency and performance of EV drivetrains, on-board chargers (OBCs), and direct-current to direct-current (DC-DC) converters.
Incorporated into power switches, these semiconductors reduce conduction losses and minimize heat generation by lowering the resistance between the drain and source (RDS(ON)). They also streamline current flow through the channel—rather than the diode—during motoring and generator modes. To mitigate electrical losses that increase with higher switching frequencies, SiC and GaN support faster switching speeds of up to 40 V/ns.
While some applications may target frequencies up to 40 kHz, GaN can operate at frequencies in the MHz range, far exceeding the 10 V/ns baseline in conventional silicon-based switches. With its larger band gap (3.4 eV) and higher electron mobility, GaN excels in reducing gate and recovery charge, enabling high-frequency operation up to 10 MHz for EV systems such as OBCs and DC-DC converters. SiC’s wide band gap and high electron mobility support lower on-resistance and reduced capacitance, minimizing switching losses for EV power and traction inverters.
The Many Benefits of SiC-Based Inverters
EV power inverters convert battery DC to alternating current (AC) for traction motors, precisely adjusting motor speed by altering the AC frequency. When in generator mode, the inverter functions as a brake, capturing energy and transferring it to the vehicle's battery. SiC-based semiconductors can further optimize bidirectional energy flow during regenerative braking, extending EV range and reducing reliance on conventional mechanical brakes.
EV traction inverters leveraging SiC-based semiconductors optimally support critical driving functions such as hill hold, anti-lock braking, and torque vectoring. Notably, a four-motor system with advanced torque management and SiC semiconductors could potentially replace standard Electronic Stability Control (ESC) systems. With modern traction inverters already exceeding 98% efficiency, many automotive companies now focus on expanding traction inverter functionality, using SiC semiconductors to streamline system integration and interoperability.
Maximizing EV Sustainability with EESMs
EV manufacturers implement various drivetrain configurations to achieve specific performance goals, maximize battery life, and extend driving range. To further differentiate their vehicles and reduce reliance on costly rare earth materials, many automotive manufacturers now prioritize drivetrain integration and interoperability for electric motors, gearboxes, and thermal management systems. For example, advanced microcontrollers (MCUs) using WBG power devices more efficiently manage multiple tasks, consolidating functions and streamlining system integration.
Another potential use case for SiC is the continued refinement of EESMs. These machines, which use field windings instead of rare earth magnets, could significantly reduce raw material costs and bolster EV sustainability. Although EESMs currently deliver slightly lower maximum efficiency than PMSMs, they can achieve comparable or better real-world efficiency at typical operating points, depending on specific design and operating conditions. They also offer more precise control across applications, while their copper windings are easier to recycle compared to the embedded magnets in PMSMs.
Despite their potential, EESMs present several challenges for EV manufacturers, including an additional exciter circuit, implementing ASIL-D torque paths, and managing effects like cross coupling between the rotor and stator. All these factors increase system complexity, energy consumption, and integration costs.
To learn more about optimizing EVs with SiC and GaN semiconductors, visit Infineon’s WBG SiC/GaN semiconductors page or download our EV-WBG white paper.