Rugged COM Express: Empowering high-performance automation for an increasingly connected world
October 25, 2013
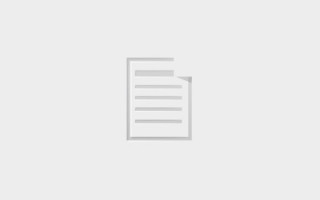
Industrial automation systems are performing more tasks and doing so more quickly, more accurately, and in harsher environments than ever before. They...
At the dawn of the “Industrial Internet,” the ante is being upped for modular embedded systems. More and more machines are being connected, many in remote and challenging environments such as oil and gas, locomotives, transportation, and ship-propulsion systems. To meet the demand for more data in less time, these systems must work faster and longer. Accelerating with the demand for data is the evolution of computer processors. But businesses can’t afford the downtime required to replace processors, or the expense of replacing the carrier board when upgrading the processor. According to a 2006 Department of Energy study, idle industrial machinery can cost as much as $800 per minute.
What’s needed is a modular embedded computing architecture that addresses these cost and downtime issues. Perhaps the most compelling of the modular architectures available today is COM Express. COM Express provides the requisite computing power for today’s increasingly connected world while also extending the lifespan of the underlying system. As chip technology evolves, users can switch out the module without adverse effect on the underlying hardware and assets – saving time and money. The modularity, simplicity, and reliability of COM Express technology help businesses remain competitive, profitable, and flexible.
Leveraging upgrades in processing power
COM Express-based technology was developed in 1994 by PICMG, a 250-company consortium that develops open specifications for high-performance computing applications. Today, the COM Express form factor comes in four sizes:
- Mini: 55 x 84 mm
- Compact: 95 x 95 mm
- Basic: 95 x 125 mm
- Extended: 110 x 155 mm
These different sizes of COM Express modules help businesses to remain competitive by maximizing the performance of critical infrastructure systems in an increasingly connected world in any conceivable industrial application.
The need for improved performance is evidenced by continuous new product introductions by processor manufacturers such as Intel, AMD, and others. Whether it is better threading, more cores, better graphics, lower power, or higher clock speeds, these companies continuously respond to demand for more and faster computing across the board – whether on the desktop or in embedded industrial systems. But replacing a complete subassembly or subsystem each time a compelling new generation of technology becomes available is time-consuming, expensive, and risky. And yet the need to leverage greater levels of processor power and performance is an imperative. Separating the processor module from the underlying carrier means that technology upgrade is painless and affordable.
Beyond this, the modular COM Express approach allows users the flexibility to deliver application-specific performance and power at an appropriate price level (Figure 1). For instance, a quad core i7-based processor module can be used on a specific carrier board for a high-value, high-criticality, high-performance application – while the same carrier board, with the same features and I/O functionality, can be deployed for a lower value, less critical, less demanding application with a lower-performance VIA Nano processor-based COM Express module; this results in lower development cost and faster time to market.
A modern locomotive is a perfect use case for this flexibility. There are nearly a dozen computer processors in today’s locomotives. While the processing requirements for these computers are different, most of them have similar I/O requirements. Using the same or a similar carrier board with different COM Express modules based upon the appropriate level of processor power for the application, depending on its profile, allows for price/performance balance.
The advantage of this level of modularity extends well beyond the initial deployment, however. In the longer term, upgrading the level of performance is simply a matter of replacing the processor module – not the entire subassembly. This saves money, and minimizes unforeseen impact on the way in which the module as a whole interacts with its surroundings.
In the locomotive example mentioned, the COM Express processor module can be upgraded without affecting the connection to the engine I/O residing on the carrier board – reducing costly and time-consuming recertification and testing. The modularity of COM Express gives a whole new meaning to “technology insertion.”
Because of this modularity advantage, COM Express can substantially extend the useful life of key elements within critical infrastructures – a valuable benefit for industrial applications such as oil and gas, energy, and transportation. This is especially true when it comes to leveraging commercial technologies – often referred to as Commercial Off-the-Shelf (COTS).
In the past, vendors often used special niche and proprietary components on their products. However, for many of these component vendors, the long-term commitment to ensuring the continuing competitiveness of these products – with its requirement for extensive investment in R&D – meant that such components often had relatively short useful lifetimes, and didn’t benefit from the support of well-funded programs to minimize the impact of obsolescence.
Commercial products, however – such as those from Intel and AMD – could be expected to benefit from a development road map that would see successive generations of products emerge into the market, each compatible with its predecessor and each capable of delivering new levels of performance. This constant “upping the game” presents a real opportunity for users of COM Express technology – and it is an opportunity that modular architectures leverage to the maximum, enabling the Internet of Things (IoT) to become a practicable reality.
Reliability for harsh environments
For COM Express to deliver real business benefit, it has to provide one other vital attribute: reliability. We are in the era of “always on” computing: The lights must never go out. And downtime means lost revenue. That’s a challenge in the harsh, hostile environments in which many critical infrastructure systems operate. Today’s connected world paradigm does not make a distinction between systems in stable environments such as offices and data centers, and systems deployed in harsh environments found in heavy industry, on factory floors, on drilling rigs, or on transportation systems.
These extreme industrial conditions require a ruggedized COM Express module (Figure 2). Specifically, they must operate in temperatures as low as -40 ºC and as high as +85 ºC – temperatures that are often found in oil and gas operations, for example. They must also withstand shock of up to 40g and extreme vibration from machinery or aircraft engines. Conformal coating is needed to resist the moisture, dust, and chemicals typical of industrial environments.
Designing, testing, qualifying, and manufacturing modular architectures for deployment in the hostile environments found in many critical infrastructure systems in industry is, therefore, a painstaking and rigorous process – but it is essential if maximum reliability and uptime are to be achieved. Modularity is helpful: By separating the processing module from the I/O carrier board, manufacturers can ensure that all the components on the processing module are specifically selected to meet application-specific extended temperature, shock, and vibration levels. It also becomes easier to test the module at maximum performance stress that can, for example, help the designers to reach an optimal heat sink solution with a uniform temperature profile early in the design cycle.
While considerable attention is paid to the design of processor modules as noted previously, the modularity of COM Express enables the development of carrier boards in parallel. Design and test engineers developing the processor module don’t have to wait until the entire carrier board is developed to verify the processor module design. This parallel – and even geographically dispersed – development can lead to lower time and cost of development while still providing a reliable solution for harsh industrial environments.
Reliable performance for today and the future
The flexibility to choose myriad differing price, power, and performance points makes the fully rugged COM Express modular architecture an outstanding choice for high-performance industrial automation applications for today’s connected world. Not only can rugged COM Express substantially lower lifetime total cost of ownership and extend the lifecycle of automation applications, they afford businesses the opportunity to harness the power and opportunity of the Industrial Internet while providing outstanding reliability.
GE Intelligent Platforms