The Tightening Prototype Schedule
January 09, 2023
Blog
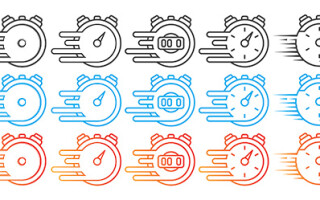
We all know the drill when it comes to developing a new product. You start with a review of the specs, then go into design review. You scope out the components that you’ll need, and then see if they are available and what the leads times are (note that this step is not nearly as straightforward as it was before the “chip shortage”).
You consult with the software design team to make sure that everyone is on the same page, and then you source some samples so you can begin the prototype design and start your board layout. Depending on the complexity of the board you’re working on, these steps can take anywhere from a few months to more than a year. Unfortunately, things don’t always go as planned.
The final step for the design team is to develop the prototype so it can be passed through for testing, to ensure that the board operates as expected and according to the original specs that were laid out. It’s also the time to do a full deployment of the software, making sure that no modifications are needed.
Prototyping ensures that all stakeholders in a product’s success have a clear picture of the (nearly) finished product. It allows software testing to occur on real hardware. And it lets the design team focus on the user interface. Implementing these steps concurrently results in a faster time to market and fewer design changes along the way.
Time to Prototype Is Key
That said, today’s competitive marketplace is driving the need to reach the prototype stage faster than ever before so products can get to market faster. This is particularly true for OEMs in the IoT space, where the technology seems move at a quicker pace, particularly when consumer technology might be involved.
There are advantages and disadvantages to getting to the prototype faster. On the one hand, the faster you can get the product out the door, the faster you can potentially earn revenue. On the other, moving at a faster pace can lead to sloppy work, insufficient testing, and having to potentially operate with different components than originally specified.
Rapid Prototyping
So, what should an OEM do when it finds itself in the position of having to deliver a prototype faster than they are comfortable with? One option is to employ rapid prototyping techniques, which gives you the ability to make adjustments to the prototype more quickly. For example, if a spec changes, or of a different component is desired, the faster you can get to the prototype stage, the faster those adjustments can be made. This option also allows for testing of systems that are intended for rugged applications, allowing the design team to take the prototype into a heat chamber and set up on a vibration table. Rapid prototyping also allows for non-mission-critical changes, like a different board size or shape, different materials, and so on; even different colors if that’s what the customer desires.
Lower the Risk of New Product Development
Another option is to join forces with a trusted technology partner like WINSYSTEMS. They understand the challenges of bringing new products to market. Working together, the OEM would have better luck sourcing components thanks to the WINSYSTEMS managed supply chain and planned purchasing strategies. This refers to the practice of looking beyond the immediate short-term need and buying components to support production cycles that may be a year or two out, ensuring uninterrupted production and steady product supply. It also mitigates unforeseen supply chain issues and geopolitical risks.
Designed to a COM Express Type 10 Mini form factor, the COMeT10-3900 SBC industrial module is suited for industrial IoT applications thanks to its high performance and integrated TPM hardware security.
An example of one of the company’s hallmark products is the COMeT10-3900 industrial COM Express Type 10 Mini module. The low-power module is designed with an Intel Atom E3900 processor. The small form factor module is a great example of what can be accomplished through proper prototyping, as it contains just the necessary features and I/O in a small form factor. Its features include up to 8 Gbytes of LPDDR4 system memory, on-board discrete TPM 2.0 hardware security, and a rugged design that operates in the -40ºC to +85ºC temperature range. I/O options include four PCIe lanes, eight USB ports, and Gigabit Ethernet.
In many cases, COMs are a good option to help speed product development, due to the flexibility that they offer. Different modules offer differing levels of compute performance, carrier cards can be standard or custom, and they can certainly hasten the prototyping process. WINSYSTEMS has the expertise to help guide OEM design teams in selecting the optimal embedded technology to enable their designs. Faced with getting to the prototype stage faster than ever before, make sure that you make the right choices along the way and lower the risk of bringing new product to market.