Application Highlight: Enclustra Mercury+ XU8 Drives High-End Applications
June 17, 2024
Sponsored Story
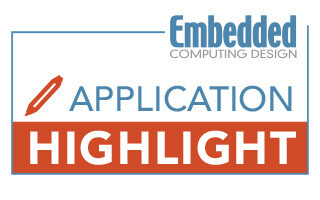
It’s easy to see that the future of embedded computing is entwined with computer vision, image processing, and other optical sensing and computational tasks. Everything from data collection to AI-driven facial recognition is reliant upon high-end embedded systems to manage the processing of those data and outputs, whether in the cloud, at the edge, or inside on-prem servers.
There are dozens, if not hundreds, of key parameters in these systems, depending on the application to which they’re applied, but these days nearly every vision system will be measured against its latency. And low is the only metric that matters.
To achieve the kind of low latency optics that are desired, if not demanded, by end users, one solution uses a purpose-built System-on-Module that can bring latency down to near-real-time levels even in the most critical of applications.
Application Use Case
Medical imaging is becoming a requirement across almost every healthcare discipline. Nurses are using it for remote assessments and care, surgeons are performing operations by looking at magnified live-feed images instead of into patients, and even researchers are making good use of computer vision for anomaly detection and inspections.
One of the major applications is in noninvasive diagnosis and treatment procedures like endoscopy. Doctors can use these compact cameras to identify and locate lesions and other diagnostic markers, and manufacturers are constantly looking to increase the resolution of endoscopes, now often to 4K. In addition, fluorescence and 3D technologies are now able to be incorporated to improve diagnosis and actively enable laparoscopic and other procedures.
Image latency in these applications is a critical factor. In fact, most endoscopic procedures only allow as little variance and lag as between 50 and 150 milliseconds, but surgical endoscopy is required to operate in real-time, or near real-time, and simultaneously perform image correction, color noise restoration, edge enhancement, scaling, and more. Surgeons need the terminal to be as small as possible to save room in the operating theater, while still having 4K definition, 3D, fluorescence, and support for SDI/HDMI interfaces.
All these requirements mean that the processor needs to manage at least three camera feeds, allocate core board resources, and facilitate data transfer and processing rates, all while maintaining algorithmic efficiency in near-real-time.
It’s not only for medical uses, either. The Leica CityMapper-2 is an advanced airborne solution for urban mapping, and it uses an FPGA module solution to speed up the development of its highly complex system that combines optics, mechatronics, high-speed electronics, and software, to create high-precision 3D maps of cities from airborne oblique imaging and LiDAR.
The Leica CityMapper-2 is specifically designed for airborne 3D urban mapping, creating 3D digital twins of cities with images and LiDAR data taken from an aircraft. To capture the images, Leica uses the newly developed Leica MFC150 optical system. The sensor is equipped with two nadir (RGB/NIR (near-infrared)) 150 MP cameras, four oblique 150 MP (RGB) cameras, and a 2 MHz pulse rate LiDAR (Light Detection And Ranging). All the camera modules are assembled in the 58 kg pod and connected via PCIe to the host PC running Windows 10. With an operator console, the recording can be monitored and controlled.
Every camera module of the Leica MFC150 contains an image sensor that is connected to an FPGA SoM. The shutters of all sensors are precisely synchronized, and the images are pre-processed and stored in the SDRAM. Afterwards, the host PC transfers all images to four SSDs, which are plugged into the host PC with an average data rate of almost 2 GB/s. At the end of the mission, the SSDs can simply be unplugged from the Leica CityMapper-2 and plugged into the desktop PC to process the data and generate the 3D maps.
Enclustra’s Mercury+ XU8 FPGA manages image capture for both of those use cases, and more, and its SoC module performs signal processing to allow the necessary real-time 4K video streaming and data management. Let’s see how.
Enclustra Mercury+ XU8
The Enclustra Mercury+ XU8 system-on-chip (SoC) module combines Xilinx's Zynq UltraScale+ MPSoC-series device with DDR4 ECC SDRAM, eMMC flash, quad SPI flash, dual Gigabit Ethernet PHY, and dual USB 3.0, and all together, amount to a complete and powerful embedded processing system ideally suited to any number of complex applications like imaging.
Mercury+ XU8 offers everything needed to execute these advanced applications, right out of the box, so engineers don’t need to build custom MPSoC hardware for each new use case. Obviously, this reduces development effort and redesign risk, but it also speeds time-to-market for any embedded solution, Enclustra says. When paired with any Mercury+ base board, the XU8 SoC module makes prototyping quick and easy so application development can get rolling. The company has also made its Build Environment available so users can more easily get started setting up and running Linux on any Enclustra SoC module, choose desired targets, and download all required binaries, like bitstream and First Stage Bootloader. The environment downloads and compiles required software such as U-Boot, Linux, and BusyBox-based root file systems.
Key Features:
- Built around Xilinx's Zynq Ultrascale+ MPSoC
- Two independent memory channels for PS (DDR4 ECC SDRAM) and PL (DDR4 SDRAM)
- 64 MB QSPI flash and 16 GB eMMC flash
- ARM quad-core Cortex-A53 (CG models: dual-core)
- ARM dual-core Cortex-R5
- Mali-400MP2 GPU (only for EV models)
- 16nm FinFET+ FPGA fabric
- Up to 504,000 LUT4-eq
- 236 user I/O and 122 FPGA I/O
- Up to 28.8 GB/sec memory bandwidth
- Offers PCIe Gen3 x16, PCIe Gen2 x4, 2x USB 3.0 and 2x Gigabit Ethernet interfaces
- Three 168-pin Hirose FX10 connectors with 236 user I/Os
- 100 MGT signals (clock and data)
- 5 to 15 V single supply
- Available in an industrial temperature range
- Linux BSP and toolchain available
- Small form factor (74 × 54 mm)
Additional Resources:
- Product Page: https://www.enclustra.com/en/products/system-on-chip-modules/mercury-xu8/
- 3D Model (Download): https://www.enclustra.com/assets/scripts/download.php?f=Mercury+_XU8_3D_Model.pdf
- Order Form: https://www.enclustra.com/en/order/#Mercury+%20XU8