Creating a Resilient Bill Of Materials
June 02, 2022
Blog
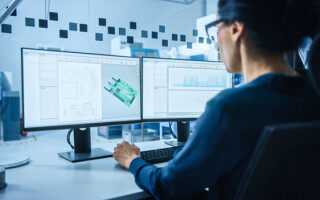
A resilient bill of materials (BOM) starts at the beginning design stages of a printed circuit board (PCB). In these times, it’s not enough to create a list of form, fit, and function drop-in replacements for your Approved Components List (ACL). Multiple strategies need to be invoked upfront, using data from agnostic sources, in making sure the BOM is robust in MPNs, and the parts are procurable. A solid BOM can help ensure a PCB is manufacturable and will have the resilience to help you mitigate disruptions.
A siloed design scenario cuts off a designer’s ability to see ahead in terms of parts availability, redact alternate components, and manufacturing information. By connecting and making transparent the value chains involved —design, supply, manufacturing— designers can drive efficiency and manage production risk.
There are four key ways to help ensure you’re creating a resilient BOM:
- Design with visibility
- Utilize historical data
- Source alternate parts
- Understand your risk tolerance
Designing with Visibility - Use an API
You need to see the broadest spectrum of available components and potential alternate parts right at the beginning of your design. In other words, design with visibility. Most designers will integrate APIs from their approved list of suppliers into their design tool to ensure the component data they need such as prices, availability, and lifecycle status is available as they’re designing. You can use singular APIs with one data feed per supplier. However, using multiple APIs from different sources can end up being clunky with you ultimately having to go through many steps just to ensure you’re getting up-to-date and accurate information.
For a significant boost in efficiency, a one-to-many resource like Nexar’s agnostic API delivers over 280 data feeds and is updated in real-time. When you design with a robust database inside your design solution, your chances of respinning a board are decreased because you’re making informed decisions throughout the design stage using the most up-to-date information on pricing, availability, technical, and compliance data.
Historical data - Looking backward while looking forward
Looking at historical procurability is another way you can help ensure the resilience of your BOM. Choosing parts based on current availability won’t help you determine if they’ll still be available once your design is sent to manufacturing.
Unpredictable elements can influence a part’s future availability at any time. It’s important that we also understand a part’s supply and demand history to help us to see more trends over time. There are many tools to help you understand historical trends. Adding the procurability of manufacturer part numbers (MPNs) to your decision-making calculus will ensure a much better chance of keeping the production lines moving.
Alternate Parts
In today’s environment, making informed decisions with limited information won’t suffice. One needs to be proactively reviewing your bill of materials to ensure availability, and that enough alternative parts are chosen, in anticipation of production issues. As you’re selecting parts, utilizing all the available component data to validate and specify multiple part alternatives can help you mitigate supply chain risk before the design is sent to manufacturing. When supply issues occur, you won’t always find alternate parts that meet the form, fit, and function of your current component selection; you may only find two of the attributes.
But by using tools like the Nexar API for identifying potential alternate parts from Octopart, you can also see what components are available. This helps to select which alternates to use at the beginning of your design process.
Those Who Fail to Learn From History are Doomed to Repeat it
When you look back in time and you either look at your specific supplier or all authorized suppliers, you’re actually able to paint a realistic picture for yourself of what’s to come. For example, a prime contractor once paid a $7 million dollar penalty to the government because they didn’t meet Defense Federal Act Regulations (DFAR). The product wasn’t manufactured on time because some of the parts they selected for their boards weren’t available by the time they were sent for manufacturing.
What went wrong?
Well for starters they didn’t look back. They didn’t look at the historical procurability of each part, which would tell them the best and worst parts to add the BOM. They didn’t take advantage of this information to figure out their risk tolerance and unfortunately, that cost them a major contract along with a hefty penalty.
Understanding Your Risk Tolerance
You need to figure out a bit of math for each component on your BOM so that you can understand the level of risk involved with the amount of product you need and when you plan on making a purchase.
Difficult? Time consuming? There are efficient solutions. A few businesses offer services to help make more informed decisions. For example, the Spectra Supply Chain Resilience report will utilize over a decade of data from nearly 300 different data sources to show you the supply chain risk for each part in your BOM. But no matter what service you use, knowing the risks associated with your parts will help ensure your BOM is resilient, and your product will be built well into the future.
Parametric matches aren’t everything! A new way to look at parts: Procurability. Is equal to the number of days that your parts were sitting on a shelf ready-to-buy, in volumes equal to what you consume annually, divided by 365 days in a year. This tells you what % of the year you could acquire stock over a calendar year. This info helps anyone identify if a part is a disaster waiting to happen, once you ask your Buyers to bring in an alternate to keep the production moving along… Sorry, the part hasn’t been available for 8 months. Huh? What will we do? Not respin another board!
Bringing it all together
A resilient BOM is probably your most important weapon against disruption and delivers the ability to quickly recover from supply chain interruptions without significant impact on operations and customer timelines. Supply chain interruption remains an unpredictable and problematic concern for the electronic design and manufacturing industry. Taking these three things into consideration will help you navigate potential supply chain issues, avoid respinning boards, and ensure the manufacturability of your designs, both in the present and future.