Improving Supply Chain Visibility
October 05, 2018
Blog
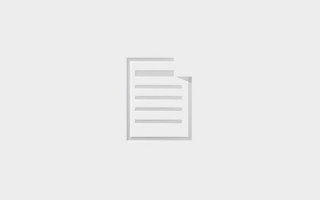
For manufacturers, overcoming daily supply chain challenges in the effective management of inventory, and more specifically, having real-time visibility into their supply chain is imperative.
Today, the complexities of most supply chains involve a large number of supplier networks and stakeholders. At the heart of creating an effective supply chain is the understanding that data from these parties – and collaboration of that information – is vital. For manufacturers, this means overcoming daily supply chain challenges in the effective management of inventory, and more specifically, having real-time visibility into their supply chain. A lack of collaboration with manufacturers’ suppliers can mean shortages, excess inventory, longer cycle times and often, higher costs.
This was the case for Yanfeng Automotive Interiors India (YFAI) as they found themselves struggling with some of these very challenges. YFAI designs, develops and manufactures automotive interior components for numerous automotive brands. In addition, as autonomous driving technologies advance and gain momentum, YFAI aspires to become a leading supplier for autonomous vehicle interiors into the future.
Headquartered in Shanghai, YFAI has manufacturing plants and technical centers around the world. The YFAI India plant started as a small operation, serving one major automotive company, and managed most of their supply chain activities manually due to a lower volume of supplier requirements. As the business grew, so did the number of suppliers along with all the accompanying supplier needs.
YFAI India began experiencing issues with inventory control overages, shortages and fluctuating customer order timeframes that led to higher freight costs. This was due to a lack of communication between YFAI India and the 22 suppliers it works with on an ongoing basis. Procurement was still performed manually as well as the management of schedules and materials. YFAI India and its community of suppliers were in need of a supply chain management software upgrade as the traditional way of doing things was no longer sufficient.
Real Time Communication Leads to Community
Improving supply chain software visibility involves leveraging today’s cloud-based technology to create better data visibility and break down divided silos of information among suppliers and manufacturers. YFAI India determined that implementing a cloud-based supply chain management portal would be the ideal solution to their supplier management needs. With this approach, YFAI would be able to facilitate real-time communication across the supply chain by extracting key inventory, order and related data and making it visible to suppliers via secure internet access. The solution integrates with any ERP whether the manufacturer or suppliers are cloud-based or on-premise. YFAI India’s supplier portal works as a data-poller, which pushes data to and from the ERP. Suppliers access the supplier portal using a browser and have self-service for invoices, bills of material, specifications and other types of documents. With the solution, suppliers can access PO and invoice information, goods received notes and rejections – all in real time, in easy to use formats.
Metrics that Matter
YFAI’s supplier portal has enabled them to furnish their suppliers forecasts and rolling plans live in real time. This reduces lead times and maximizes the shipment process. What’s more, YFAI India can now better manage inventory delivery and quality issues from suppliers, enabling both YFAI and their suppliers to more proactively optimize the performance of their production schedules. Overall, YFAI India realized the following:
- 25 percent reduction in inventory and the elimination of shortage and overage problems
- 90 percent reduction in missed deliveries
- A drop in premium freight costs from 1-2 shipments per month to only two in eight months
- Faster payments and adherence to credit terms with streamlined invoicing processes
With a cloud-based supplier portal management technology, manufacturers can see a reduction in inventory investment, order and shipment costs, procurements costs and an elimination of many of the errors that were a result of manual processes. Overall, it can lead to a huge improvement in the visibility of their supply chain as well as the mitigation of risks. Manufacturers can communicate purchasing and replenishment requirements to their suppliers as soon as customers’ demands change.
Terry Onica is director of automotive, at Santa Barbara, Calif.-based QAD, Inc. (NASDAQ:QADA/QADB), a leading provider of enterprise resource planning (ERP) software and services to global manufacturing companies.