Electronic Parts Shortage: Why the Automotive Industry Took the Worst Hit
June 15, 2021
Blog
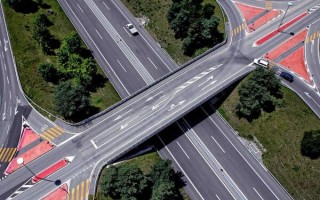
It feels like déjà vu — only this time, the tables have turned. Back in 2009, the global demand for products in the automotive industry crashed.
New vehicle sales fell by around 40%. Employment also declined by 45%. Big automakers like Chrysler and General Motors eventually filed for bankruptcy until the government bailed the industry out.
Fast-forward to over a decade, and the automotive sector seems to be in a crisis once again. Reason: electronic parts shortage.
How Bad Is It?
To be clear, the shortage of electrical components (from semiconductors to chips and sensors) is not an exclusive problem for automakers. Still, the industry, according to experts, seems to be the worst hit.
Speaking with Reuters, Stellantis — which has Alfa Romeo, Fiat, Chrysler, and Peugeot as its subsidiaries—mentioned that the lack of available chips had only gotten worse over the last three months of 2020. So far, it has achieved a strong performance because of high prices, but common sense dictates that this is unsustainable in the long run.
Meanwhile, other carmakers tried to be more “innovative” by downgrading their vehicles’ amenities. Nissan, for instance, may be removing navigation systems for models that should have them. Intelligent rearview mirrors may also be missing in the future RAM-1500 pickups.
Some want to be more optimistic about the possible availability of the much-needed electronic parts. But others like to be more realistic, saying it may take until 2022 or around 18 months before the industry can balance supply and demand.
But perhaps it is also essential to address the elephant in the room: why is there a chip shortage in the first place? It turns out many factors are at play.
1. COVID-19 Pandemic
Expectedly, the COVID-19 pandemic dampened the already-declining new vehicle sales, at least in the United States. According to the National Automobile Dealers Association (NADA), retailers sold only 14.46 million units — over 15% lower than in 2019 and a far cry from the pre-pandemic estimate of 1% to 2% fall.
The point is, there should be lesser demand for chips, right? The industry got it wrong because these components became crucial for other sectors like appliances and tech devices, such as mobile phones, PCs, laptops, gaming consoles, and tablets.
All these have become necessary during the health crisis. In fact, the need is so high that buying a new laptop became more difficult in 2020. This increased demand attracted chip suppliers to shift their production from catering to the automobile industry to making chips for consumer electronics sectors.
2. Political sanctions
US sanctions against countries like China are nothing new. Sanctions such as these have been around since the Tiananmen Square Massacre. During Trump’s administration, the then-president imposed tariffs on primary construction materials, such as steel and aluminum.
Before the pandemic, the country hit China again after accusing Huawei of using backdoor equipment for espionage, eventually forcing the Red Dragon to blame the situation for the shortage.
But there’s more to the story. Others are saying that these sanctions are now compelling Chinese companies to stockpile semiconductors and other electrical components if the tension eases.
Moreover, the ongoing problem is forcing developed nations to begin or increase domestic production. However, it can be costly. The European Commission, for example, plans to expand its global chip manufacturing to 10%. But to achieve that, it needs to spend over £30 billion.
Developing Resilience Like Toyota
For businesses in dire need of parts, they can consider using sites like OEMsecrets.com, which has a broad database of distributors and prices. This process gives companies access to available supplies domestically and internationally.
Note, though, that fixing the electronic parts shortage isn’t as simple as increasing its production. It demands a multi-pronged approach that includes strengthening diplomatic ties, improving global economic policies, and finding the delicate balance between supply and demand in light of growing industries that need these electronic components too.
But every company can also learn from the Toyota disaster plan. To understand the context, Toyota, one of the world’s biggest carmakers, experienced a massive parts shortage when a 2011 earthquake and, later, a tsunami hit Japan.
Some reports suggested that the company suffered a production loss of 300,000 domestic vehicles and 100,000 more overseas from mid-March to April. By the end of April, revenues declined by a whopping 69%. All these because Toyota’s domestic production was more established than the overseas facilities.
Because of this, the business, which also popularized the just-in-time (JIT) model, changed its strategies. One of its primary methods is the Reinforce Supply Chain under Emergency (RESCUE) system. Under this, the business created a database of over 600,000 supplier sites, assessing their parts information and vulnerabilities.
It also introduced the 60/20/20 supply model. The company that provides 60% of the components becomes Toyota’s leading supplier. However, if it fails to meet the requirement, two more vendors can step up to close the gap.
While Toyota still keeps up with JIT to reduce waste and production costs, it also learned to generate more reserves for more in-demand or critical components, such as semiconductors.
Nobody knows how long this chip shortage will last; but if there’s one thing that businesses can derive from this problem (and even from this pandemic), resilience can help one tide over. Just look at Toyota.
Dan Dooley is professional applications engineer since 2015 with a passion for technology, IoT, DIY and sports. He provides a mix of tactical advice, education, and networking services to engineers and their businesses. You can follow Dan’s work here: https://www.electronicscomponents.co.uk/