Enabling machine learning in industrial systems
November 20, 2017
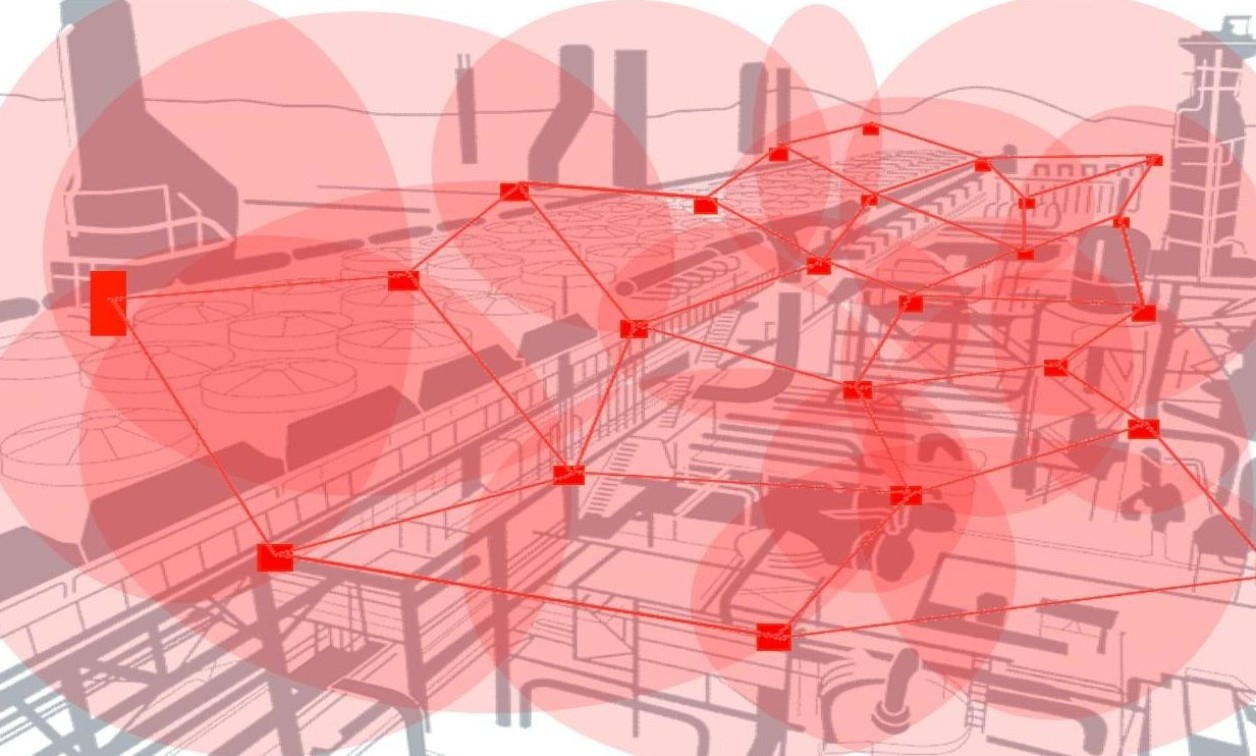
Keep track of multiple sensors distributed within the assembly line, combine their outputs at an overall factory controlling point, and adjust parameters in the assembly line if necessary.
Factory managers are always looking for new ways to improve assembly-line quality, reliability, and efficiency to achieve higher profits and growth. A common way to lower downtimes is to monitor the status of the gears within a robot arm or the motors of a conveyer belt. If it’s detected that for example a gear wears out, a replacement can already be ordered and the gear can be replaced during a scheduled maintenance time. That is why many sensors and cameras are distributed around manufacturing sites in modern factories, collecting large amounts of data.
To make the best use of this collected data, it’s not enough to just monitor a single parameter of a machine and repair it as soon as its gears wear out. The next step is to keep track of multiple sensors distributed within the assembly line, combine their outputs at an overall factory controlling point, and adjust parameters in the assembly line if necessary. That is where machine learning comes into play.
For example, let’s say that due to changing temperatures or other environmental conditions, the mechanical dimensions of a manufactured part are drifting. An application of machine learning would work like this:
- Sensors inside the factory measure the environmental parameters in the factory and the conditions of the motors inside the manufacturing line. This can include vibration sensors that measure the gears’ movements inside the production machine, current sensors to measure the current consumption of the complete motor, and a humidity plus temperature sensor that measures part of the environmental conditions where the motor is operating. All those parameters are then transmitted to a main factory controller.
- After the manufacturing process, a camera inspects every part. The camera sends this image data to the same factory controller, which runs an image-processing algorithm. This algorithm compares the newly manufactured part and its dimensions to a mechanical model which has been created on a computer. Next, the algorithm detects that some mechanical dimensions are out of their tolerances.
- The factory controller now combines the information about the changed environmental parameters and drifting mechanical parameters. A correlation between changing temperature and the mechanical drift is detected.
- To compensate for the drift, the factory controller sends new parameters to the assembly-line controller, which adjusts the manufacturing process. This can be new manufacturing coordinates for the machines in the production line, ensuring that the mechanical dimensions stay within the defined tolerances. It could also be simpler commands, such as controlling the HVAC to regulate temperature and humidity inside the factory. In addition, if the gears are already in bad shape, an order for a replacement part could be placed automatically
- Last, the factory controller stores the correlation between the status of the machines, the environmental conditions, and the changed mechanical parameters. This information can be used to react quickly next time, and to exchange this knowledge with other assembly lines in the same factory.
Texas Instruments offers solutions to enable modern factories and implement machine learning. These solutions include sensing and signal conditioning, control and processing, video, secure communication, and power management. The company also provides in-depth support with evaluation modules (EVMs), application notes, reference designs and more.
More information about machine learning in the white paper, Machine learning powers autonomous industrial systems.