Success Story: On HELLA’s Automotive Assembly Lines, AI is Helping Humans Too
June 08, 2022
Story
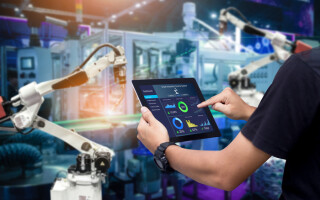
The automotive industry is still working its way back to pre-pandemic levels of manufacturing productivity. But it’s not as simple as flipping a switch. And Gary Jackson, CEO of intelligent automation company Drishti, says that’s because “it is still the case that 70% of all of the assembly work is human dependent, not fully automated.”
[Editor's note: Listen to this story in the Embedded Insiders podcast wherever you get your podcasts or in the embedded player below.]
In other words, the bottleneck is often the human-in-the-loop.
Even in 2022, humans are often far more precise and dexterous than robots, and certainly more capable of adapting to the constantly changing variables of manufacturing environments. So, for now, at least, they’re not going anywhere. And that applies to all manufacturing facilities today, including those with the most advanced AI and most sophisticated automation technology.
“Even in the environments where they are moving as aggressively as possible towards automation, there are some things that robots just can't do,” Jackson says. “Now we see ourselves as supplementing and complimenting that human dependency.”
Drishti specializes in AI-powered manufacturing technology and, more specifically, human-in-the-loop AI. Human-in-the-loop AI helps optimize industrial processes like automotive manufacturing that involve both automation equipment and human factory workers by monitoring the entire workflow for inefficiencies. For example, using AI-powered video analytics, the Drishti platform can identify awkward physical movements that contribute to worker fatigue and ultimately result in factory station slowdowns.
At least that’s how it’s being leveraged at the Dhankot, India production facility of German Tier 1 automotive parts supplier HELLA.
AI-Powered Production Improves Cycle Time
In producing a particular product, human workers at the HELLA plant needed to attach a bolt to a specific part. This involved the worker rotating his or her body 90 degrees to grab a bolt from a bin with their left hand and attaching it while continuing other tasks with their right on the opposite side of the workstation.
It sounds like a trivial operation, but the cumulative effect of performing it improperly resulted in as much as a 10 percent productivity slowdown from operator to operator.
“We were able to identify a situation where operators were not following standard procedures and creating risks for the product and for themselves,” says Huri Mendoza, Head of Operational Excellence Electronics at HELLA. “Then you start finding small, medium, and large problems. But the part that is important is not to find the problems. It’s to fix them.”
Of course, fixing the problems starts with finding them. Drishti custom-built 3D convolutional and spatio-temporal neural networks for action-recognition that analyze video feeds of HELLA’s assembly line. Designed to focus more on humans than machines, the Drishti AI compares the sequence in which steps are meant to occur and the time required for each action being performed at each station on the line.
(Source: Drishti)
“We pre-process the video in a small appliance that sits on premise in the customer site so that we optimize what's being transmitted to the cloud,” Jackson says. “Then we do our analysis of that video feed, and we create our metadata in the cloud. If it's an environment that needs real time or near-real-time alerting as a result of that analysis, it transmits that back down to whatever the appropriate alert or monitoring system is in place at the customer site.”
Plant managers can leverage Drishti’s Live Production platform to determine whether steps are being missed in the process or tasks are being completed on time. When events like these occur, the platform issues real-time alerts to supervisors with stored video data points of the incident so they can follow up on issues like missed procedures, low materials, processes that occur to quickly or too slowly, etc.
(Source: Drishti)
HELLA deployed 12 Drishti video streams running Drishti TRACE and Drishti FLOW, two tiers of software that allow manufactures to assess live and recorded video, as well as utilize AI for continuous monitoring.
“They may or may not have the resources to be able to go and adjust to a real time anomaly.” Jackson explains. “But if they can look at statistics and gather sufficient evidence that an anomaly is persistent and not just a one-time occurrence or that an anomaly is affecting the overall operational effectiveness of the line, then on a daily basis, they can go back and focus in on those things that had enough data elements, enough points of proof to justify the change that they’re asking the team to make.”
With a better understanding of how HELLA used the information, Drishti updated their analytics from daily to periodic reporting that gave plant supervisors better insight into larger trends and key periods within each eight-hour shift. With this periodic reporting, Drishti’s action-recognition algorithms, and seven cameras, HELLA was able to recapture all 10 percent of their lost efficiency on a production line in just three-to-four months.
(Source: Drishti)
But the collaboration didn’t just benefit HELLA. The process of analyzing HELLA’s assembly process provided Drishti with a massive dataset for building and optimizing gesture- and action-recognition algorithms. Usually, one of the more time-consuming parts of the AI model development process, access to these datasets helped Drishti reduce the average cycle time for model creation from months to just 72 hours.
A New LEAN Process with New Results
Before adopting Drishti’s AI technology, HELLA was formerly using state-of-the-art LEAN methodologies in manufacturing, but collecting and processing data manually. Although the company was utilizing cameras and video in production, prior to the partnership, they had no AI technology on the production line.
Drishti’s AI solution changes the way factories use traditional objection recognition by moving away from just 2D imaging and incorporating a third dimension, time. By contextualizing events captured on video within the sequential operations of a production line, plant managers can pinpoint inefficiencies and work toward cycle times that yield better productivity and ultimately faster return on their investments.
In addition to the efficiency gains HELLA was able to recapture, the success in this story is about how the two companies found a way for humans and machines to work together thanks to AI.
And based on the results, it looks like humans are here to stay.