Enabling Industrial Devices to Speak Multiple Fieldbus Languages Without Hardware Translator
March 27, 2023
Blog
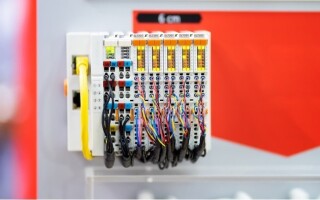
In the early years of industrial process control, industrial devices (sensors and actuators) were individually connected to a programmable logic controller using dedicated wires that carried analog (4-20mA) current signals. However, the number of required inputs and outputs increased as processes became more complex, making cable routing complicated and unwieldy and fault debugging increasingly tricky.
As a result, industrial digital Fieldbus networks (Figure 1) were developed to reduce wiring by enabling multiple control and measurement signals to be transported over a single cable (bus).
While this presented a breakthrough, as several other proprietary Fieldbus networks later emerged, a single standard could not be established. This resulted in multiple versions used in various factory settings and industrial devices being compatible with some versions of Fieldbus but not others.
Some of the most common Fieldbus networks currently include:
- Profibus
- Modbus
- CANOpen
The protocols differ in the number of devices they support, their language syntax, and the physical interfaces used. More recently, several incompatible real-time Fieldbus networks (whose operation is based on Ethernet) have been developed, including:
- EtherCAT
- Profinet
- EtherNet/IP
One of the major decisions for a manufacturer is which Fieldbus network to target for their device. The conventional approach has been to source a third party communication module to allow the device to communicate on that network (Figure 2).
Figure 2: Block diagram showing how an industrial device communicates with a Fieldbus using a communication module.
While this is a low-risk and convenient solution, it brings several less apparent disadvantages. The most obvious (and significant) limitation is that it restricts the device to only communicating with the version of Fieldbus implemented by the module, narrowing the potential market to customers using that version of Fieldbus in their factories. Enabling the device to operate on other Fieldbus networks requires repeating the process and sourcing a different module for the new version of Fieldbus. Since communication modules come in different packages and are not pin-compatible, this redesign can be expensive and time-consuming.
Using dedicated hardware also makes it more difficult to add extra features and functions to the design of a device. Furthermore, manufacturers have no control over their supply chain since a communication module can usually only be sourced from its manufacturer. This can lead to unexpected production downtime if supplies are unexpectedly interrupted. Another hidden cost of this approach is that some module suppliers require royalty payments, resulting in an unavoidable overhead that persists over a product's entire lifetime.
Shaking Off the Hardware Shackles
A new paradigm that allows manufacturers to break from this accepted model is to use a software stack running on their device microcontroller that will enable it to join a Fieldbus network. Completely removing the requirement to use a costly communication module, thereby lowering the bill of materials, this approach brings several other advantages. It dramatically increases flexibility in product design because a software stack can be easily modified to provide customized features and functionality. Furthermore, manufacturers can take full ownership of their supply chain since they no longer need to source hardware from a third party.
Additionally, by modifying the code in the software stack, a device can be quickly retargeted to communicate with a completely different Fieldbus, making it possible to bring a new product to the market much faster than a hardware redesign. A software-based approach also makes it easy to add innovative and customized features to higher-end product offerings by modifying the code in the stack.
Proven Fieldbus Stacks
U-Phy from RT-Labs is an example of a software-based approach that enables devices to communicate quickly over multiple industrial Fieldbus networks with Profinet and EtherCAT. This pre-certified software stack runs on an open hardware design, eliminating the need for proprietary hardware without requiring additional royalty payments.
Fieldbus industrial communications bring many benefits to industrial process control systems in factory environments worldwide. However, the conventional approach to allow industrial devices to communicate on Fieldbus networks has been to use an 'off-the-shelf' communication module. While this provides a low-risk solution, it has several disadvantages, including high cost, lack of flexibility in product design, and potential supply-chain interruption. Using a Fieldbus software stack is an alternative approach that reduces material costs, enables more flexibility and innovation in product design, and mitigates risk by allowing manufacturers to control their own supply chains completely.