Efficiently Power Your Industrial Motors, Today and Beyond
July 27, 2023
Sponsored Story
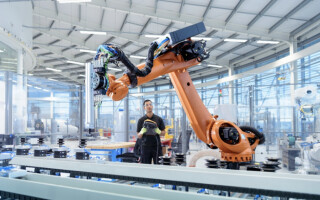
Motor control for industrial applications has been a discussion topic for as long as motors have existed. The biggest reasons for that never-ending discussion have to do with the need to drive them more efficiently, meaning that we want to do more with less power, while maximizing the up time of those motors. In many cases, we are referring to “always-on” power, where a system is required to run 24/7/365.
Adding on that seemingly never-ending motor-control discussion, we have a relatively new trend, adherence to Industry 4.0. Industry 4.0, which is considered to be the integration of digital and automation technologies into manufacturing processes, brings in its own set of challenges related to motors and power control. In addition, Industry 4.0 relies heavily on the seamless communication and connectivity between various devices and systems, often multitasking between those systems.
Industry 4.0 also means having a modern production facility that will require cloud connectivity, an array of actuators (both analog and digital), and of course, significant processing capability. A key reason for that connectivity is to provide for updates on the software side, which goes hand-in-hand with ensuring that there is a large enough memory footprint, yet not too large. This is the mechanism by which manufacturers will future-proof their systems.
The Brain of the Industrial Platform
One device well suited to manage this application is Infineon’s 32-bit XMC7000 MCU that’s based on an Arm® Cortex®-M7 processor core (see a demo of the XMC7000 controlling a robotic arm). Because it’s aimed at industrial applications, the part is equipped with peripherals such as CAN FD, TCPWM, and Gigabit Ethernet, as well as support for hardware security. Single- and dual-core options are available, and both are supported by a Cortex-M0+ core so designers can optimize their end products to meet the specific conditions required for the application. It offers low-power modes down to 8 µA.
Block diagram of Infineon’s 32-bit XMC7000 MCU key features that are optimized for industrial applications.
The XMC7000 MCU can operate in harsh environments with a temperature range of -40°C to +125°C. Four package/pin types are available, with 17 part number variants to meet just about any industrial design requirements. In addition, the MCU can be bundled with extensive software solutions that enable sophisticated motor and power control, including ModusToolbox™ software for a common development experience across platforms. Provided as a collection of development tools, libraries, and embedded runtime assets, ModusToolbox software is architected to provide a flexible and comprehensive development experience.
Connecting It All Together
In the context of motor and power control, connecting all the motors, drives, controllers, sensors, and other components to a local network is key. Ensuring reliable and secure communications between these devices can be a challenge, particularly when dealing with legacy systems or heterogeneous equipment from different manufacturers.
Developers must consider that motor and power control systems often come from different vendors. Hence, they may use different communication protocols and standards. Achieving interoperability between these systems can be a challenge, as it requires developing standardized interfaces, protocols, and data formats that enable seamless integration and communication across different devices and platforms. It could also be that multiple systems are operating concurrently. The result is an obvious need to maintain that high level of performance throughout the network of systems as well as the need for customization, with a quick set-up time.
Helping to Secure the Industrial Platform
And of course, with increased connectivity and data exchange within the manufacturing and automation environments, the risk of cyber threats and attacks becomes more prevalent. Motor and power control systems are potential targets for cyberattacks that can disrupt production processes or compromise sensitive data. Adding robust cybersecurity measures, including encryption, access controls, and intrusion detection systems, is crucial to protect against these threats.
Timers and PWMs
Timers and pulse-width modulators (PWMs) are also key components in the industrial realm. For example, the timers are used for scheduling and sequencing of mechanical and electronic components, as well as for process control. When it comes to monitoring, timers are used to track the duration of various processes or events, which can then be used for diagnostics purposes.
PWMs generally control the amount of power that gets delivered to a load, such as to DC or three-phase AC induction motors. By varying the duty cycle of the PWM signal, the average voltage applied to the motor can be adjusted, thereby controlling its speed. The PWMs also have a say in energy efficiency by regulating the amount of power sent to the mechanical device.
The latest machine-learning techniques provide a pathway towards predictive and proactive maintenance within the platforms. System down-time can be costly, so anything that can eliminate or mitigate that condition is welcome.
Overcoming all these challenges requires a comprehensive approach that addresses technical, operational, and organizational aspects, as well as collaboration among various stakeholders in the industrial ecosystem. Infineon’s XMC7000 is at the forefront of that industrial pathway.
To learn more or to get started with Infineon’s XMC7000 family, visit www.Infineon.com/XMC7000