Mechatronics aids in embedded system design
December 05, 2016
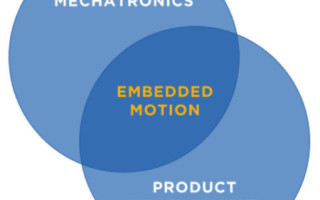
By looking at embedded systems from a different perspective, a mechatronics perspective, systems can be improved while saving cost. Over the last few...
By looking at embedded systems from a different perspective, a mechatronics perspective, systems can be improved while saving cost.
Over the last few years, a lot has been written about the future of computing as centered around “big data” algorithms running on servers in data centers. However, embedded systems are also becoming more and more prevalent in our everyday lives. Yet the skills needed to design and develop robust and stable embedded systems are quite different than those needed for the latest cloud infrastructure products. Similarly, the field of mechatronics is not all about industrial automation, and the skills needed to develop devices with deeply integrated mechatronics differ from those required to integrate commercial off-the-shelf (COTS) motion components into an industrial machine.
One of the hottest features of today’s consumer products is wireless connectivity, as demonstrated by the explosion of interest in the Internet of Things (IoT). Connectivity requires embedded computation which enables an always increasing product feature set. The first generation of connected IoT products has mostly led to connected sensors and remote displays. However, consumers are no longer satisfied with the limited interaction with the physical world that these devices provide.
The next step forward for connected consumer devices is the ability to directly affect the local environment. The best-known example of this type of connected product is the Google Nest thermostat. Nest has taken the thermostat from a very basic device that uses a mercury switch to turn a furnace and/or air conditioner on and off to a computer-controlled, Internet-enabled “killer app” IoT product. The benefits of this device go well beyond just keeping your home at a comfortable temperature. Energy companies are working with consumers and their Nest thermostats to help manage electrical grid infrastructure. As IoT devices gain the ability to affect the physical world, incredible new possibilities can be realized.
The most useful interactions with the physical world require the ability to move something around (warm air, coffee, M&M’s, you name it), and that requires a mechanism. Let’s look at some key approaches and components that create and define these systems.
The engineering field that brings together the mechanics of motion, motor drive-electronics, and computer control is known as mechatronics. The computing field ranges from cloud applications running on industrial server farms to 8-bit microcontrollers (MCUs). The terms “embedded computing” and “embedded systems” have been useful to the industry to differentiate application-specific software running on MCUs from their big-iron brethren.
In a similar manner, mechatronics runs the gamut from industrial applications, such as automated factories and complex projects like automobiles, right down to consumer devices like inkjet printers. To help differentiate the mechatronic systems embedded in consumer products from their industrial cousins, we’re using the term “embedded motion.”
As we examine our parallel between embedded systems and embedded motion, we ask the question: who does embedded motion engineering? Aircraft and automotive manufacturers are structured around major subsystems like engine, transmission, chassis, etc. However, product development companies tend to be structured around individual products, with sub-teams grouped by engineering discipline.
Unfortunately, the product development industry’s team structure tends to have a blind spot with respect to mechatronic systems engineering. It’s common to have a senior or lead engineer that partially fills the role, but this is typically a secondary responsibility. We believe there are significant benefits to allocating dedicated resources to embedded motion.
Benefits of embedded motion
Embedded systems engineering is a cross-disciplinary field that’s proven its value to the product development community. The best embedded systems engineers have a skill set that spans both the analog and digital realms of electrical engineering as well as computer science. When bringing up a new PCA, this skill set allows one embedded-systems engineer to do the job. With skills that cross traditional boundaries, the engineer can be more efficient in their job and develop solutions that would otherwise not exist.
The same logic holds true for the embedded motion engineer. With a skill set that touches on mechanical and electrical engineering, as well as control systems and computer science, the embedded motion engineer brings together everything needed to get a motion control system up and running correctly.
In my work with various product development companies, I’ve found that they benefit greatly by having an engineer dedicated to the embedded motion system in the product. With the proper training and experience, the embedded motion engineer brings two major benefits to the design, namely balanced and optimized design and specialized knowledge.
Balanced and optimized design
The embedded motion engineer has ownership of the overall design margin for the embedded motion system. Figure 2 shows how power flows through a motion system, as well as across design disciplines. Not shown is the additional interaction with the product owner who will define the product performance specifications, thereby driving the load’s motion profile.
The embedded motion engineer has the visibility to design margin and cost built into the power supply, motor drivers, motor, and mechanics. In addition, this engineer owns the system control and related performance requirements. Thus, the embedded motion engineer is well situated to drive the effort to balance margin across the system, and trade off performance versus cost, providing the overall optimal cost/performance ratio for the product.
Specialized knowledge
The engineering curriculum is extremely dense. Colleges and universities struggle to cover engineering fundamentals and introduce a variety of discipline sub-topics in four years. A student that chooses to focus their engineering electives on cross disciplinary courses related to motion and control systems brings additional tools to the job.
An embedded motion engineer should have training and/or experience in topics such as advanced control systems (beyond PID), digital electronics, analog electronics, computer science and mechanism design. This range of skills lets the embedded motion engineer correctly specify or select components in each of the blocks in Figure 2, as well as sensors and the feedback control system firmware needed to bring everything together.
To illustrate the benefits that an embedded motion specialist provides, here are several real-world examples that demonstrate how designs were significantly improved when a mechatronics design was applied to the heart of the following embedded motion systems.
Consumer ink-jet printer motor
Today’s printers have motion embedded at the heart of their design. In one case, a mechanical design engineer was given the job of selecting the motor to drive an ink-jet printer cartridge carriage on top of the system’s full mechanical design. Without the proper experience, the engineer relied on the motor supplier for support. The supplier provided three conservative options. The engineer tested all three, and selected the best. In the production volume of roughly 100.000 units per month, this motor cost about $5.
With access to the full system design, our embedded motion engineer performed a more detailed analysis of the system than the supplier could. It was determined that the originally selected motor was larger than necessary. The engineer specified a correctly sized motor which the supplier provided for $1.50, saving the company roughly $700,000 over the product’s two-year production life.
Consumer ink-jet printer power
Like all good, conservative engineers, an electrical engineer in charge of the power-supply design for an ink-jet copier was forced into a large, but underutilized power supply. The system had a wide difference between the average and peak power draw due to a condition where both the bed scanner motor and the ink cartridge carriage motor acceleration overlapped by about 50 ms. Lacking the visibility to the system design, the engineer had no other choice than to address the shortcoming with a larger power supply, leading to a significant cost increase.
When the more experienced embedded motion engineer assessed the situation, he found that he could modify the firmware to lock out simultaneous acceleration of the two motors. This drastically reduced the peak power draw, allowing a smaller and cheaper supply to be used. In addition, the embedded motion engineer’s analysis showed that the required 50-ms acceleration delay in one of the motors only occurred roughly once every 50 pages, so there was no measurable impact to copy speed.
A tale of two drives
In the design of a high-volume laser scanning system, the client needed extremely precise control of the laser scan rate. The scanning was controlled by a brushless DC (BLDC) motor. The original design used a once-per-revolution optical sensor signal to control speed, and drove the motor with field-oriented control (FOC), and advanced and very smooth BLDC drive technology. Unfortunately, the math required necessitates a relatively high powered microcontroller, adding about $10 to the system cost.
Here, the experienced embedded motion engineer proposed an alternative. Instead of using a single reflective stripe per revolution, the line count was increased to 25, yielding 50 position measurements per revolution. Coupled with a customized control algorithm, the velocity control was measured to be within a few parts per million of the FOC design, while only adding $1 to the system for the modified reflector, for a savings of $9 per unit.
Buzzkill
In the design of a high-volume drive train, a small dc motor was attached to a sheet metal mounting plate. The design was fully tooled and close to the ship date when it was discovered that, at a particular drive speed, the motor’s cogging torque signal hit the resonant frequency of the mounting plate. This caused an audible hum, which was a significant issue for the customer.
In this design, the embedded motion engineer augmented the standard PID control loop that he had used with a controller based on the internal model principle (IMP). IMP is an advanced technique where a model of the system disturbance can completely cancel out the disturbance. In this case, the disturbance was the sinusoidal motor commutation torque signal. By implementing an IMP controller, the torque ripple from the motor was completely cancelled, thereby eliminating the motor plate vibration. This removed the need for a tooling change, thus saving the schedule.