Smart Factory Demo to Give University College Dublin Engineering Students Hands-On Experience with Industry 4.0 Principles
January 17, 2019
Story
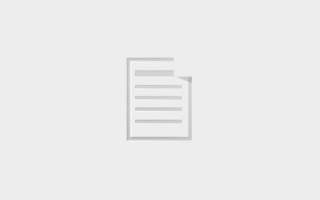
For Maxim, this donation is, indeed, a way to help advance education on the principles of adaptive manufacturing and the industrial internet of things (IIoT) for the next generation of engineers.
Reading about and hearing lectures on complex topics such as Industry 4.0 and adaptive manufacturing provides a good theoretical foundation. But being able to complement this knowledge with a hands-on smart factory platform adds another dimension to the educational process. Students at University College Dublin’s (UCD’s) School of Mechanical and Materials Engineering will be able to have this experience. In December, Maxim donated its soccer ball factory demo—a popular draw at the last two electronica trade shows in Germany—to the school. The university is just a stone’s throw away from Maxim’s Dublin office and the two entities enjoy a strong collaboration.
“Our soccer ball factory has been pivotal in demonstrating the concepts of Industry 4.0 based on the capabilities of our third-generation industrial factory automation chipset that embodies the Go-IO IIoT reference design," said Jeff DeAngelis, managing director, Industrial & Healthcare Business Unit at Maxim Integrated. "We are very happy that we can now pass the factory on to good hands to help educate a new generation of students and prepare them for the technological challenges of the future.”
At the donation ceremony, John Kirwan, vice president of Global Customer Operations at Maxim, noted, “There are simply tremendous commercial opportunities ahead in the field of robotics and to give students the opportunity to experiment and get their hands dirty with a real system is hugely beneficial. We have developed a tremendous relationship with UCD in the last 18 months. We come here first for our engineering interns and graduate hires. The quality of talent has been exceptional. We want to see the students have fun with the soccer ball factory as engineering is often about taking joy from curiosity and satisfaction from solving problems.” Also at the ceremony, Anders Reisch, managing director of Sales Training at Maxim, said, “During our discussions it became clear that both a robot and an open-source PLC platform would be very useful for UCD both for formal teaching activities and research/projects. Maxim’s soccer ball factory is a perfect fit.”
For Maxim, this donation is, indeed, a way to help advance education on the principles of adaptive manufacturing and the industrial internet of things (IIoT) for the next generation of engineers. We now live in a smarter world where everything and everybody is connected. In the industrial world, smart factories play an important role in providing companies with the ability to achieve higher levels of productivity and flexibility. As DeAngelis notes, they also provide countries with a way to compete more equally on a global scale by re-leveling the playing field. In many ways, a smart factory represents the ultimate cyber-physical system, where if you tug or poke on any part of the system, it dynamically reacts and compensates for that force based on a closed-loop type of interaction. This is the power and strength of a smart factory or a smart automation system.
Professor Nikos Papakostas agrees that there are plenty of opportunities in store for the soccer ball factory demo. Papakostas is the director of the Master of Engineering with Business Program and research director at the Laboratory for Advanced Manufacturing Simulation (LAMS) at the UCD School of Mechanical and Materials Engineering. He notes that the school is grateful to have the equipment and will introduce a new robotics and digital manufacturing module utilizing the demo, as well as a lab that will allow students opportunities to play around with different robot configurations. Different academics and researchers also have plans to tap into the factory demo for research projects. Projects in the works that could potentially use some or all elements of the demo include studies around high-payload-capacity robots, advanced industrial communications simulations for human/robot collaborations, advanced robotic automation systems, and modern machine-learning tactics.
Pushing Intelligence Closer to the Edge of the Digital Factory
Starting with regulation-size soccer balls, the soccer ball factory is calibrated to test the balls for weight, air pressure, bounce height, and roundness. An industrial robot handles the balls, and the entire assembly line is wirelessly controlled via an iPad app. With the demo, students will be able to learn—and observe—how a production system can embody a level of flexibility to react to different environmental conditions, product variations, specification changes, or even product options. While the demo is optimized to test size-five soccer balls, it can also be configured on-the-fly to test balls of different sizes. If a smaller ball is inserted at a random point in the production line, the factory can identify the product variation and readjust its different sensor calibrations and the robotic software to process the different size accordingly.
Inside the soccer ball factory demo is an array of industrial communications components. The demo’s backbone is the Go-IO IIoT reference design, which helps move intelligence closer to the edge of the digital factory. Compared to its predecessor, the Go-IO is 10x smaller and consumes 50 percent less power. It is built with Maxim’s new third-generation industrial automation chipset consisting of:
- 12 highly integrated ICs
- 17 IOs supporting multiple digital IO configurations
- A 4-channel IO-Link master to provide a universal IO interface to both analog and digital sensors
- And a robust 25Mbps isolated RS-485 communications channel that provides a reliable, multi-drop data network for uploading time-sensitive health and status information into the cloud
This factory demo exemplifies an Industry 4.0 factory that is controlled locally by a programmable logic controller (PLC) reference design driving a host of intelligent sensors that communicate the factory’s health and status information to enable real-time decision-making to enhance productivity. The beauty of having a small, distributed PLC working in conjunction with smart, IO-Link-enabled sensors is that changes in the assembly line can be affected at a local level and in real time. Notes Papakostas, “You have equipment that is far away from headquarters. Instead of sending an engineer or an operator there every week or every month, you just get information from the signals and you make a decision. It’s a breakthrough technology and it will change a lot.”
Creating Smart Factories of the Future
While the multi-disciplinary demo provides a “working lab” for the students to learn about industrial controls, analog and digital IOs, and sensors, it is also a foundation for more advanced study into concepts such as artificial intelligence (AI) algorithms for new levels of decision-making. There’s plenty of opportunity for the students and professors to improve upon this platform. For example, Maxim has included extra sensors to monitor health and status, but the company has not yet taken advantage of learning about the health and status of each of the ICs in the reference platform. So, notes DeAngelis, the students and professors can go deeper into what’s going on with some of the ICs themselves.
When it comes to the IIot, Papakostas agrees there are plenty of opportunities for advancement. The level of automation and intelligence available also opens the doors for design engineers to gain more insight into how products are actually used, so they can incorporate this knowledge into next generations of products. While some may feel anxiety over increasing levels of automation, Papakostas isn’t too worried. “People think that more automation means less flexibility, but in reality, when you know what you’re doing and what your equipment is capable of, you can come up with flexible solutions with more automation,” he said. “In the end, engineers build solutions for people. Only engineers understand what people need, it can never be a machine. It’s about using information technology and computing power to help engineers do their jobs in a much faster and efficient way.”