Are Smart Factories Flexible? How to Boost Flexibility in Production Using IoT
August 13, 2024
Blog
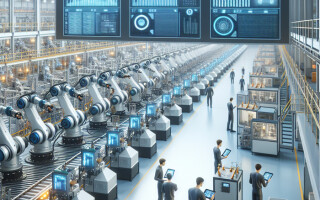
Production has long mastered Flexible Manufacturing Systems (FMS), which grant up to twice the time and cost savings when there is a need for repurposing. Comprising a central control computer, production machine, and material-handling system, FMS works cohesively to reprogram to support dramatic changes in product type and quantity.
However, traditionally, only large-scale enterprises focused on metal-based components production could extract this value, while flexibility has long been a coveted trait in the diversified realm of manufacturing. This is where IoT comes into play.
The IoT ecosystem is saturated with ever-traveling data flows from multiple production equipment, which opens up new dimensions of flexibility to help manufacturing of any type and scale adapt at the moment when facing changes. Moreover, it unlocks a new level of strategy planning in responding to economic and political fluctuations, and a space where innovations are fostered through digital twins. Why is a ‘gold mine’ hidden in this case and how to reveal it? Let’s have a detailed expert look.
Ways the IoT Enables Flexibility on a Smart Factory
IoT-based Intellectual production systems drastically surpass the FMS, as well as other approaches aimed at flexibility surge, such as cellular manufacturing, for a range of reasons. First, they embrace the whole enterprise by having machines, shops, and floors connected with sensors and united under a single IoT supervision platform. This lifts availability for every node of the smart factory system and simplifies automation control. Second, they don’t require cost-intensive re-equipping of manufacturing, since they overlay the assets, including legacy. This is what we call ‘bridging physical and digital worlds’. Third, they promote a paradigm shift by extending to machines, processes, people thinking, and production philosophy. This challenge turns into lucrative opportunities when adapting promptly.
Thus, if an enterprise is ready to inaugurate IoT from essentials, it will be able to ‘bear’ flexibility for all the production aspects enabling instantaneous and cost-effective operations for:
- Machines reprogramming of any type and scale
- Adjustments for the material handling approach
- Production process control agility
- Horizontal and vertical scalability potential
- Efficient re-organization of staff operations
Individually, the IoT component for each of these directions promotes a tangible boost in flexibility, but the real potential is revealed when a business allows IoT to alter the total production approach, which touches every process down the chain. It results in cohesive and interoperable processes aimed at the core production goal completion. Yet today, they have all the instruments to bring this idea to life at great efficiency.
Use Cases for Making the Production Flexible
It has been proven many times that successful IoT transfer is goal-dependent, which brings strategy building to the forefront, starting from business planning to legacy migration management. Understanding the full toolset IoT can offer helps navigate the goal setting and methods on how to enhance physical-digital interactions. The following practices are proven to increase transparency, predictability, and manageability to help make the business processes more flexible.
Remote Access to Smart Factory Control
As a rule, FMS reprogramming, maintenance, or quality control require technicians with specific knowledge onsite. Remote access to the manufacturing fleet dramatically alleviates this challenge by making specialists more available and reducing the time required for operation. When connected to the central server, production equipment reports its crucial data while the IoT platform promotes multi-level access for all the stakeholders involved for relevant and efficient supervision and task completion. Moreover, it becomes much more convenient to respond to incidents and provide system updates OTA. Ultimately, the management board is always up-to-date on process performance to make relevant decisions.
24/7 online access can be successfully provided via production-compliant network protocols, such as Wi-Fi, or Zigbee. When production involves difficult-to-reach areas, it is worth considering mesh networks to enable continuous data transfer in poor signal conditions or through multiple obstacles, such as walls.
Data-Driven Automatic Reprogramming
AI + IoT tandem is a breakthrough in the automatic reprogramming of machines and production lines since it instantly triggers intelligent reactions based on production and parameters collected. These integrated systems can analyze data on machine status, inventory levels, production rates, historical data, and environmental conditions to generate optimal production schedules, thus eliminating bottlenecks, reducing downtime, and increasing the general availability of the entire smart factory. By moving to the Edge, AI-based systems can enable hard RTOS to eliminate latency in time-critical applications. The early adopters of automatic production planning have yet to gain their benefits. For instance, automatic data analysis might also hold inventory control and make automatic orders to support the urgent need for repurposing.
This level of automation ensures the smart factory is always operating at peak efficiency, without the need for manual intervention.
From Planned to Predictive Maintenance
Scheduled maintenance is not only a rigid but resource-intensive approach that doesn’t guarantee 100% availability of the equipment until the next maintenance. By equipping the crucial machine components with sensors you can track the performance indicators in real-time to establish condition-based maintenance first. By involving AI to analyze the collected data, upcoming failures can be detected much in advance to establish predictive maintenance. For instance, vibration sensing is highly valuable in predicting the deterioration of rotating equipment parts by analyzing misalignment, imbalance, or loss issues. Thus, maintenance can be planned at a convenient time to avoid costly downtimes and forced reactive maintenance, as well as expenses on unnecessary maintenance of the operable equipment.
Basically, why do we hear about predictive maintenance so often? The hype of PdM is backed by the fact that it is the most proven success case of IoT adoption in general. It naturally pushed evolution for multiple IoT trends, and now we can talk about plug-and-play PdM tools, AR-based repair, and PdM-as-a-service offerings. Each one unties ‘hands’ to maintenance personnel and the executive board in more informed and efficient maintenance management.
Safety & Security Compliance Control
IoT systems take on safety & compliance management by establishing 24/7 monitoring of hazardous areas, detecting physical presence, gas leaks, and excessive heat, and monitoring the correct working task execution. When potential threats are detected, your IoT system can immediately trigger alerts, enabling swift response and mitigation efforts. Biometric authentication, remote lockdown capabilities, and real-time video monitoring ensure that only authorized personnel and materials gain access, minimizing the risk of security breaches or unauthorized activities.
Thus, implementation of forward-looking worker safety IoT solutions promotes standards compliance freeing up resources on key tasks of a smart factory.
A Room for Experiments with Digital Twins
A digital twin of a production system is exactly what helps save on market testing and real-world experiments when defining the better option for components’ configuration or material handling. It provides precise analysis and data-driven forecasts to help create virtual prototypes. By modifying the Digital twin of the product or its part, it becomes easier to navigate drawbacks and predict the demand. Moreover, ongoing IoT monitoring coupled with advanced analytics enables real-time process and machine drawback identification and suggesting features to enhance the existing product.
When developing a flexible manufacturing system, Digital Twins helps comply with the required production parameters. It becomes easier to showcase and prove the concept to justify the significant investment that the production system usually requires.
Smart Factory Flexibility – Who Benefits?
Every market player has their reasons for innovating for higher agility, which makes us expect a more intelligent production landscape in general.
Although corporations do not financially suffer from the need to introduce new functionality or product types in manufacturing, they are sensitive to global economic and political alterations that may instantly bring dramatic financial losses. Thus, supply chain disruptions or a need for reshoring may force higher automation, and flexibility is most welcome.
SMEs are sensitive to both global and local fluctuations. The ability to rapidly respond to new environments, repurpose, or expand production affects their business perspective and frequently comes to a matter of existence. The latter is especially relevant for medium enterprises that supply specific products for corporations since they become heavily reliant on their “big” partners. Flexibility enables them to produce diversified orders. Being flexible for highly specialized manufacturers is also of crucial importance since their high-end and valuable products still aren’t protected from a drop in demand.
Whatever the reasons, companies tend to upgrade the existing powers with IoT instead of completely substituting the equipment fleet.
Taking Stock on Smart Factory Agility
Agility is what is being fought for now because it gives freedom and variability of actions in critical decision-making. IoT is what can be gifted without re-equipping the existing fleet.
- IoT promotes machines, production lines, processes, and people’s work flexibility by creating an ecosystem of connected devices with greater transparency and manageability.
- Continuous monitoring, AI-based reprogramming, predictive maintenance, and digital twins are the most promising use cases to elevate agility within a smart factory environment.
- IoT incorporation is expected to grow among every type of manufacturer since it enables affordable production customization.
- To make the most out of a flexible environment, enterprises should master IoT from the essentials by involving it in strategy planning concerning every production process.