Use pneumatics to supercharge your next project
May 12, 2016
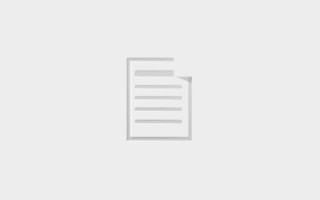
Air-powered, or pneumatic, machinery has long been a staple of automated manufacturing. Able to deliver an incredible amount of force at a high speed,...
Air-powered, or pneumatic, machinery has long been a staple of automated manufacturing. Able to deliver an incredible amount of force at a high speed, these pneumatic cylinders, rotary actuators, and even air logic components are quite useful. They can even be used in specialized situations where electricity would interfere with a process.
Unfortunately, the bar to entry for using these type of devices is higher than using electricity directly. The first barrier is that unlike electricity, compressed air isn’t supplied to us from outlets spaced conveniently around most rooms. One needs an air compressor to produce this type of energy. Though fairly common among serious hobbyists or mechanics, you won’t find one in an average person’s garage. This means that a teenager that purchases an Arduino clone for $10 to experiment with, probably doesn’t have the resources to also spend $100 or more on an air compressor.
The second barrier to entry is component availability and cost. Although you can find components online, such as from Automation Direct or on more general sites like Ebay or Amazon, much of what’s available is generally sold by distributors. Even a cheap system, including solenoid valves, and actuators/cylinders, fittings, and tubing can cost hundreds of dollars when set up correctly. Add in the knowledge required to safely work with air, and the fact that there aren’t as many Makers or even MakerPros working with this technology, and making that transition can be daunting.
On the other hand, those that do decide to experiment with pneumatics technology open themselves up to a huge number of possibilities. One of the more interesting pneumatic Makerpro projects, or rather series of projects, is Kolja Kugler’s One Love Machine Band. This robotic band makes extensive use of pneumatics in its design, as can be seen clearly in the video. In it, you immediately see one of Kugler’s robots pressing down on the frets of a bass guitar with small cylinders controlling each finger. You really need to see it in action.
In a related project, the band Compressorhead uses similar pneumatic actuation. If they seem similar, that’s not a coincidence. The Makers of both bands once worked together, but ended up producing different projects.
While Compressorhead focuses on making music and careful engineering, Kugler’s One Love band focuses more on the artistic side. Kugler sources parts from wherever he can find them, and uses all brands of pneumatics. He also tends to start out with a rough sketch rather than a carefully-dimensioned drawing. As an engineer, both thoughts make me quite uncomfortable, but given his excellent results, perhaps we can learn a lesson from this more improvised technique.
Though they could hardly be considered MakerPros, rather talented engineers willing to make really off-the-wall and excellent projects, Festo, a major German pneumatics manufacturer, could certainly give MakerPros inspiration. Though not all of their projects appear to involve pneumatics directly, their innovations, from 2010 to 2012 in this case, including a robotic bird and a mind-controlled gaming rig, are bound to inspire. If nothing else, these projects, which are reminiscent of their distinct LEGO-like component style, should serve as a reminder that a really great finish can be almost as important as an excellent mechanism!
Jeremy S. Cook is a freelance tech journalist and engineering consultant with over 10 years of factory automation experience. An avid maker and experimenter, you can follow his exploits on Twitter, @JeremySCook.