The Power of Edge Computing: A Robotic Asset Monitoring Use Case
January 29, 2019
Story
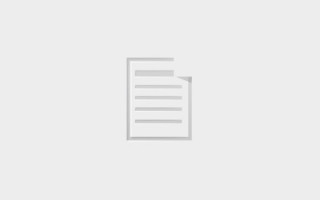
A sophisticated edge computing platform allows manufacturers to collect data directly from any robotic system or controller in real time without the need of an internet connection.
Long before the term “Internet of Things” was ever coined, the technology industry was connecting a series of networked objects to collect and exchange data. Then came Cloud Computing, which gave the industry a place to store all of that data. Enter modern day, and now Edge Computing is here to stay as a part of the picture – taking some of the essential data processing and analytics work from the cloud and bringing it to edge devices. Gartner predicts that while currently only 10 percent of enterprise-generated data is processed at the edge, by 2022 that figure will reach 50 percent. Half of all processing power is expected to slowly shift from the cloud to edge devices, leading to IoT projects that utilize the power of both cloud computing and the intelligent edge to make smart business decisions.
As Edge Computing matures I often share industrial use cases to demonstrate just how powerful an edge computing framework can be for processing and making use of data at the edge. One good example is a customer who manufactures robotic machinery who can reduce downtime and maintenance costs with an edge computing platform.
Robotic asset monitoring is aimed at tracking the uptime and downtime of overall equipment effectiveness (OEE) and service-level agreement (SLA) parameters. Traditionally, plant managers and maintenance professionals have combined many techniques both quantitative and qualitative to identify the potential for failure and mitigate downtime for robotic assets. These poor maintenance strategies can reduce the manufacturers’ productive capacity and cost them millions of dollars each year. Today, companies utilizing robotic assets require the ability to connect, collect, and analyze data to prevent instantaneous costs of failure.
The constant use of robotic systems combined with the nature of an advanced manufacturing plant creates the need for various measures to maintain operations. The instantaneous cost of failure can disrupt an entire plant cycle, resulting in delays and cost-heavy outcomes for both the manufacturer, their partners, and customers. In the past, extremely expensive technology investments have been required to handle the large volumes of data to monitor robotic assets, which limited deployment to only the largest organizations.
Smart, connected technologies have now become attainable in both cost and accessibility, making it possible for a plant manager with limited Industry 4.0 experience to monitor robotic assets and use the information to maintain operations and prevent instantaneous cost of failure. A sophisticated edge computing platform allows manufacturers to collect data directly from any robotic system or controller in real time without the need of an internet connection. The data can then be processed and visualized locally using the platform or, if required, pushed to an IoT Cloud platform, which will display OEE and all of the other required parameters in one centralized and easy to use dashboard.
The solution allows the plant manager to determine the best factors for remote condition monitoring, whether it be temperature, vibration or other parameters specific to their operations. Once the parameters are set, the plant manager receives alerts when issues arise. After analyzing the data over time, the system is able to self-learn and adjust to patterns on the fly and enable a predictive maintenance system to monitor and thus maintain robotic assets.
Edge computing platforms give companies access to the vast amounts of data available from their industrial systems, and then allow them to make sense of the data to drive further intelligent action. They can predict when and where failures could occur, maximizing the efficiency of the manufacturing plant and improving operations over time, while minimizing bandwidth and Cloud costs. Proactive maintenance can increase the lifespan of equipment, decrease downtime, and decrease maintenance costs.
John Younes is the Co-Founder & Chief Operating Officer at Litmus Automation. He is in charge of operations and growth for the company and draws on considerable experience working with start-ups and early stage companies. He has a Bachelors in Management from University of Western Ontario and a Masters in Management with specialization in Global Entrepreneurship from EM-Lyon.