Easing the Design Challenge of Developing more Efficient Motor Drive Solutions
April 30, 2020
Story
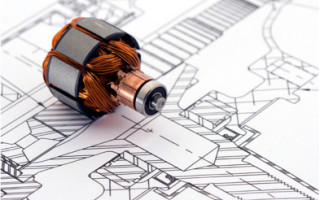
In a highly industrialized economy, automation plays a critical role. As consumers, and manufacturers, we are collectively more aware of the environmental impact this level of automation can have.
In a highly industrialized economy, automation plays a critical role. As consumers, and manufacturers, we are collectively more aware of the environmental impact this level of automation can have. Our dependency on automation is well established, so the necessity for more efficiency is now providing the stimulus for invention in the area of motor drives and controls.
Across the industrial sector there is a concerted effort to adopt efficiency, often enforced through legislation and enabled by standards approved by governments. A recent example here is China's standard GB 21455-2019, which applies to room air conditioners. In order to comply, the motors must either be electrically commutated or in some other way capable of variable speeds. The need for variable drive speeds is becoming increasingly common across all applications and it typically requires at least six switching devices to implement it effectively. For high power applications the switching devices will need to be robust and capable of handling high currents and voltages. In this case, IGBTs have emerged as the technology of choice.
While consumption remains high for all types of motors, semiconductor manufacturers are seeing strong demand for integrated solutions that are optimized for driving Brushless DC Motors (BLDCs). This demand is coming almost entirely from manufacturers eager to exploit the energy efficiency of BLDCs, who are now using them to displace less efficient motors, predominantly brushed DC motors.
This trend comes with challenges, however, as the energy efficiency gains offered by BLDCs are not entirely free…the drive stages are considerably more complex. The opportunity for the semiconductor industry is to simplify this complexity, which is not a trivial task because the drive stages for BLDCs require six power transistors, rather than just one for a Brushed DC. Orchestrating the operation of six transistors is only part of the challenge, in most cases the end applications will also need to accommodate the BLDC and its drive circuitry in the same size, space and weight envelope currently occupied by the Brushed DC.
Compounding this, in some applications the number of power transistors may need to be doubled to 12 because the application requires higher power than a single transistor can handle. Paralleling up power transistors is an alternative to using larger and more expensive transistors in these situations.
Clearly this puts even greater pressure on the transistor's design, both in terms of its electrical performance and physical profile. ON Semiconductor has addressed these issues by developing power transistors that feature the industry's lowest on-resistance, Rds(on), while at the same time migrating its technology to the latest packaging profiles, such as the SO-8FL PQFN package which measures 5mm x 6mm.
In order to accelerate the migration to more efficient motors, as well as help manufacturers meet stringent new legislation, the trend within the semiconductor industry is towards higher levels of integration. In practice, this means putting the gate driver in the same package as the IGBTs and encapsulating them in a way that complies with the application's needs and meets legislative requirements.
ON Semiconductor's response to this need includes an already wide portfolio of Intelligent Power Modules, or IPMs and the development of new power modules covering both Converter-Inverter-Brake (CIB) and Converter-Inverter (CI) topologies. Often the industrial environment can present a challenge for modules of this type, as they are not always hermetically sealed against ingress. Here, again, ON Semiconductor has demonstrated its innovation by developing a package that uses transfer molding, or TM. As well as being hermetically sealed, the TM-PIM family offers three times the power cycling capability and 10x the temperature cycling of a comparable gel-filled, non-hermetically sealed power module.
Transfer-Molded Power Integrated Modules (TM-PIM)
The demand for motor drive solutions is increasing, both through natural expansion and the wholesale migration to more efficient topologies, such as BLDCs. ON Semiconductor is addressing this through the development of innovative products such as its large portfolio of Super Junction MOSFETs, offered in a variety of packages with an operating voltage range of 600V to 800V and an Rds(on) from 23mΩ to 1400mΩ. ON Semiconductor is also a leader in IGBT technology, covering 650V and 1200V devices, as well as SiC MOSFETs and associated isolated/non isolated gate drivers. The introduction of the TM-PIM further extends ON Semiconductor's portfolio of integrated power modules able to address an even wider range of motor drive applications, offering higher integration and extended power/temperature performance.
1200 V SiC MOSFETs
ON Semiconductor continues to develop its portfolio of motor drive solutions because there is sustained and growing demand from the end markets it serves. With little evidence of this demand relenting, ON Semiconductor will continue to innovate and extend its offerings.