Design Considerations and Solutions for Autonomous Mobile Robots
September 25, 2023
Blog
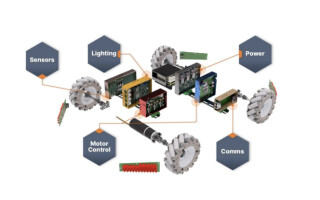
Autonomous mobile robots (AMRs) are becoming increasingly common across many industries, including manufacturing, logistics and warehousing, agriculture, retail, hospitality and more. They provide several benefits, like higher efficiency, increased productivity, and safer work environments.
This article discusses applications for AMRs and requirements for the various components used in their construction, including motors and controllers, sensors, lighting, and communications interfaces. It also suggests suitable solutions from onsemi to quickly address these multiple requirements.
Figure 1: Solutions for an autonomous mobile robot (AMR) based on onsemi products
AMR Applications and Benefits
In factories, AMRs can be used for transporting goods and to assist with implementing quality control procedures. AMRs can assist with loading and unloading goods in logistics and warehousing. Some benefits AMRs bring to farmers are more precise crop monitoring and soil analysis, resulting in increased productivity.
The retail and hospitality sectors enjoy the advantages of being able to offer better customer service by using AMRs to deliver orders and guide guests around venues, freeing up staff to interact with customers. The applications and sectors where AMRs are deployed will continue to grow as their underlying technology develops.
Motors and Motor Control in AMRs
Motor-driven actuators are critical in AMRs, enabling arms, lift platforms, and wheels to move. Selecting an actuator involves evaluating components like brushless DC (BLDC) motors, motor controllers, MOSFETs, universal controller boards (UCB), and gate drivers. BLDC motors are highly efficient, generate little noise, and require less maintenance (thus making them more reliable). For these reasons, they are popular in AMRs.
Due to their high torque-to-weight ratio, motor controllers can manage the motor’s speed and direction with a precise movement profile. These can be fully integrated (with an embedded control algorithm) or use a dedicated microcontroller unit (MCU) to implement the control algorithm.
Three-phase BLDC motors, common in AMRs, are driven by three high-side and three low-side power transistors connected across the windings of the motor such that they can energize these coils and create magnetic fields that spin the rotor. Commutation algorithms are used to generate pulse width modulation (PWM) signals that are applied to these switches in order to turn them on and off. Some examples of commutation schemes are sinusoidal, trapezoidal, and field-oriented control.
The motor control switches used in AMRs are typically silicon-based as the BLDCs used in AMRs are normally 48V and less. For fast AMR development, onsemi offers several BLDC motor control solutions, including the 24V to 600V, ECS640A ecoSpin™ ARM Cortex BLDC motor controller with integrated 3-phase gate drive, integrated precision sense amps (4x), and integrated bootstrap diodes. onsemi also offers the NCD83591 5V to 60V 3-phase BLDC gate driver, as a low-cost solution.
onsemi’s power boards are also compatible with the Xilinx Zynq Universal Control Board (UCB), which is based on the Xilinx® Zynq®-7000 SoC for BLDC. This UCB is ideal for applications requiring precise control and can also be used to implement artificial intelligence (AI) functions.
For high-performance motor applications in AMRs, onsemi offers a range of medium voltage (MV) MOSFETs. It’s latest T10 silicon MOSFETs are based on shielded gate trench technology with lower on-resistance (RDSon), lower gate charge, and an inherent snubber-like functionality to reduce overshoot and minimize ringing. onsemi’s 40V and 80V T10 MOSFETs have industry leading RDSon at 0.42mΩ and 1.5mΩ respectively. They also offer lower gate charge and best-in-class soft recovery for reduced voltage spikes. Contact onsemi for more information on NTMFS0D4N04XM, NTMFWS1D5N08, and the rest of the MV MOSFET portfolio.
Sensors for AMRs
AMRs need to monitor and interact with their environment, requiring different types of sensors to gather relevant data. Sensors commonly deployed in AMRs, include temperature, image sensors, LiDAR (for 3D mapping), rotational movement, and visual light communications (VLC) sensors.
Image sensors and image signal processors enable visual perception, allowing an AMR to navigate its environment by detecting and recognizing objects and then taking an appropriate course of action. onsemi offers global shutter and rolling shutter image sensors ideal for this application.
For example, the AR0234CS image sensor is based on an innovative global shutter pixel design optimized for accurately capturing fast-moving scenes (120 frames per second) in full resolution, producing sharp images for machine vision, or scanning barcodes. Position sensors measure the rotation of a robot’s wheels or other moving parts, allowing it to track its position and orientation accurately. Ultrasonic and infrared sensors measure the distance to remote objects, enabling an AMR to detect obstacles and avoid collisions.
onsemi’s NCS32100 is an industrial rotary position sensor which combines accuracy and speed. It features a 38mm sensor and delivers +/-50 arcsec accuracy at 6,000 RPM. For lower-accuracy applications, it can support speeds up to 100,000 RPM. This new device uses a patented approach to inductive position sensing which is ideal for industrial and robotic applications.
Powering an AMR
Power supply and Power Tree technologies are critical components which impact an AMR’s battery life and operational capability. When selecting an AMR’s power system, important performance characteristics and parameters include energy density, voltage, current requirements, efficiency, and solution size. Lithium-ion batteries' high energy density and long life make them a common choice in AMRs.
Power management units regulate power flow from the battery to other components while Power Trees consisting of switching converters and voltage regulators ensure they receive the appropriate voltage and current levels.
As an example, the FAN65008B Synchronous PWM Buck regulator achieves a peak efficiency of 98%, stepping down a 48V Input to a 28V output, while supplying a constant 10A DC load.
The NCP1632 Power Factor Controller (PFC), NCP1399 LLC controller and NCP4307 Synchronous Rectifier Controller (SRC) work together to optimize efficiency when converting from AC to DC in power supplies up to 1kW.
onsemi’s EliteSiC silicon carbide MOSFETs are ideal for AC-DC and DC-DC power conversion in high power applications typically > 3kW. In order to charge the battery of an AMR, a residential or industrial AC supply must be converted to a usable medium-voltage DC output. Both the AC-DC front end and the primary side of the DC-DC converter can benefit from EliteSiC FETs. The secondary side of the DC-DC converter can use switching optimized onsemi trench MOSFETs.
Lighting
The importance of lighting technologies, like light-emitting diodes (LEDs), is that they enable AMRs to navigate, communicate, and operate in various environments. Lighting is also used for signalling and to indicate an AMR’s status or direction. When selecting lighting technology for an AMR, performance characteristics and parameters to consider include brightness, color temperature, and power consumption. LED controllers and drivers are critical components which monitor the amount of current flowing in LEDs enabling them to emit light of a specific intensity and wavelength.
LED driver circuits use high-side and low-side power MOSFETs to switch on and off the LED current and protect against overvoltage and overcurrent conditions. They also ensure the stability of the LED driver circuit. The onsemi’s NCV7685 LED linear current driver and the NCL31000 are intelligent LED drivers ideal for AMR lighting applications.
The NCV7685 has twelve linear programmable constant current sources with a common reference, allowing 128 different PWM-adjustable duty cycle levels. The NCL31000 features a high-efficiency buck LED driver that supports high-bandwidth analog and PWM dimming (down to zero current), two auxiliary DC-DC converters, and diagnostics to monitor input and output current and voltage, LED temperature, and DC-DC voltages.
The NCL31000 supports Visible Light Communication (VLC) which uses visible light as a carrier for transmitting unidirectional data up to 10kb/s. VLC allows an AMR to securely communicate with other devices and humans. Since visible light spectrum is 430 THz to 790THz, VLC will not influence nearby wireless technologies like Bluetooth® Low Energy (Bluetooth LE), Zigbee, UWB, and Wi-Fi. VLC is secure because it is inherently limited to line of sight.
AMR’s navigating in warehouse applications benefit from UWB, Bluetooth LE (AoA/AoD), and Wi-Fi Indoor Positioning Systems (IPS). But sometimes RF congestion or interference can compromise IPS.
To mitigate against this, VLC can be used to complement existing RF IPS by installing VLC into the ceiling luminaire grid, where each ceiling luminaire transmits a unique ID#. If the AMR contains a floorplan database containing each luminaire position and unique ID, the AMR can self-navigate with a simple photodiode facing the ceiling as depicted in Figure 2 below.
Figure 2: AMR’s using VLC for Indoor Positioning Systems (IPS)
Communication
Wireless communication technologies are vital for AMRs, enabling them to communicate and interact with other devices and systems by transmitting data and receiving commands. When selecting communication technologies for an AMR, performance characteristics and parameters to consider include operating range, data rate, power consumption, and security.
The operating range must adequately communicate with other devices and systems in its environment using an appropriate data rate. Power consumption must be sufficiently low to preserve battery life for as long as possible, while security is critical for protecting AMR data and commands from being accessed or compromised.
Bluetooth Low Energy is a wireless communication technology designed for low power consumption, making it ideal for battery-powered devices. It supports a range of data transfer rates for transmitting sensor data and control signals between an AMR and other devices. Bluetooth LE can also be used in indoor positioning systems, allowing AMRs to navigate dynamic environments.
onsemi’s RSL15 is a Bluetooth 5.2 certified transceiver for easy-to-implement Bluetooth LE wireless applications, supporting AOA (Angle of Arrival) and AOD (Angle of Departure) key features to enable accurate Indoor Positioning Systems (IPS). The highly integrated radio system on chip (SoC) optimizes system size and battery life. It features an ARM Cortex-M33 processor and a 2.4 GHz transceiver, which supports Bluetooth LE 5.2 and 2.4 GHz custom protocols.
Individual AMRs also require internal wired digital communication for real-time control between the on-board central computer and individual motor controllers, lighting controllers, and sensors. CAN (2Mbps) or CAN-FD (5Mbps) have been the typical protocol of choice over the years. Both protocols communicate across UTP (unshielded twisted pair) cable, and individual nodes can be configured in a daisy-chain, multi-drop typology saving cable weight and cost.
The Ethernet Alliance recently introduced 10BASE-T1S (10Mbps), an Ethernet IP-based digital communication protocol also capable of communicating across a daisy-chain, multi-drop, typology, with a minimum of 8 nodes across a minimum of 25 meters of UTP, or Single Pair Ethernet (SPE).
The main advantage of 10BASE-T1S over CAN and CAN-FD, is faster data rates, and an all IP-based Ethernet communication protocol domain from the brain to edge node, facilitating Artificial Intelligence (AI) and Machine Learning.
onsemi
Conclusion
Applications for AMRs continue to grow across diverse industries. However, they are complex systems that require integrating multiple disparate technologies to operate autonomously, reliably, and safely. Their success depends on selecting the best technology choices at the design stage.