Industrial Metaverse Blueprints, Part 2: The Metaverse Runs on Digital Twins
October 27, 2022
Story
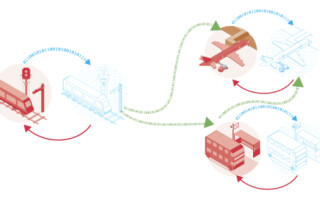
The second article in our metaverse series focuses on defining the industrial metaverse, its building blocks, parallels with model-based systems engineering (MBSE), and examples of how modeling and simulation are being used to empower digital twin ecosystems.
Read part 1 of the Metaverse series here.
Most people define the metaverse as a “virtual reality” with avatars and 3D representations of real objects in spaces that simulate how we interact with the physical world. This part of the metaverse tends to be “consumer oriented,” allowing users to “suit up” in their VR systems and interact with people and things in a virtual world.
While the consumer (or social) metaverse focuses primarily on entertainment value, the industrial metaverse focuses on solving complex industry problems through advanced modeling and simulation. These modeling and simulation capabilities leverage the holistic knowledge and understanding made available by connected digital twins.
Gartner defines a digital twin as “a digital representation of a real-world entity or system.” Within the domain of a single product, this definition is not much different than object modelling or computer-aided design. But the true power of the industrial metaverse lies in the ability of these digital twins to interact with each other. Connecting digital twins can create entire virtualized “systems of systems” where inputs and resulting behaviors of one digital twin can affect other digital twins operating entirely within a virtual space.
The objective of the industrial metaverse is to model digital twins in such a way that they can be interconnected and interfaced to allow larger systems and industrial worlds to understand how to solve complex problems our global society faces today. For example, solving world hunger requires a host of digital twins – from farms and agricultural equipment to distribution centers and transportation systems – to form a virtual system of systems. Through modeling and simulation, the operations of all “constituent” digital twin systems are optimized for the food sustainability goals of the entire system of systems.
As another example, automakers can use the digital twin of a new vehicle design and virtually simulate its performance against various road conditions, gasoline grades, and maintenance timelines to predict gas mileage, reliability, and environmental impact. An industrial metaverse could enable this digital vehicle twin to be inserted into the digital twin of a larger system – a smart city – to assess road impact, emissions, and traffic patterns.
Although simulations and digital twins both utilize digital models to replicate a system’s various processes, a digital twin is actually a virtual environment, which makes it considerably richer for study. The key difference here is largely a matter of scale: while a simulation typically studies one particular process, a digital twin can run any number of useful simulations to study multiple processes. The first version of a digital twin can be a simple representation of only some of the attributes of its real-life counterpart, but over time and as needed the twin can become more sophisticated to match the evolution of the physical system.
A variety of stimulus can be applied to a digital twin to analyze and predict product or system behavior. This allows for design optimization prior to building the physical product or implementing a physical system.
Digital Twins, Cyber-Physical Systems, and MBSE
Once a physical product is built, a digital twin has limited value unless it can accurately synchronize its state with that of its physical counterpart. Cyber-physical systems (CPS) provide a key interface between digital twins and physical systems (Figure 1). These systems are comprised of physical components that can be monitored, controlled, and optimized by smart sensors, software, and actuators.
[Figure 1. Interaction of physical and digital twins through cyber-physical systems.]
In many respects, a CPS envelops both digital twin and IoT technologies to provide a foundation for autonomous systems such as driverless cars. However, digital twins require holistic information sets rather than rudimentary models, and a challenge in the development of a CPS is the large difference in design practices between the various engineering disciplines involved in system creation, such as software and mechanical engineering.
Enter the concept of MBSE, which involves the methodology by which these complex systems can be designed, analyzed, and verified. MBSE provides a design “language” that is common to all the disciplines involved in the creation of the CPS.
The Software Engineering Institute defines MBSE as a formalized methodology used to support the requirements, design, analysis, verification, and validation associated with the development of complex systems. In contrast to document-centric engineering, MBSE puts models at the center of system design.
But MBSE is more than a system model. It is the linkage of models to create a system that understands its boundaries, its contradictions, and can communicate the reasons for its design changes. It is the bridge between requirements and low-level, high-fidelity technical models created by domain specialists.
When rapid innovation is essential, engineers from all disciplines must be able to explore system designs collaboratively, quickly allocate responsibilities to software and hardware elements, then analyze the tradeoffs between them. MBSE can be a driving force behind the development and adoption of digital twins that are indistinguishable from their physical counterparts across the entire system lifecycle.
Optimizing Smart Product Design: The Journey Toward Digital Twin- and MBSE-Driven Lifecycles
Digital twins and CPS are becoming increasingly relevant to systems engineering and, more specifically, MBSE [1, 2]. Their combination enables real-world systems to be analyzed and optimized, but this requires a transformation across the development lifecycle that will enable the adoption of MBSE and digital twin technologies and ensure all their benefits are realized.
For instance, smart products like cars are becoming intricate systems of systems, challenging engineers to harness layers of complexity and data and blurring boundaries between different engineering domains. The digital representation of all facets of a smart product in a comprehensive digital twin is no longer optional to manage the complexity of today’s product development – it has become a design requirement.
To fully leverage digital twin technology, we must first shift our focus towards developing digital twin models that can be utilized across the whole system lifecycle – including product design. A common misconception is that a digital twin is only utilized once its physical counterpart has been created, but “shift-left” philosophies (or the practice of improving quality by moving tasks like testing to as early in the development lifecycle as possible) can also be applied using digital twins to find and prevent defects early in the product or system design process.
“We add on top of that the ability to tie in these virtualized real-world environments … with the semiconductors operating well before going to silicon. That’s a true shift-left environment that enables the OEM to get a level of confidence about the decisions they’re making that is completely unprecedented” – Joseph Sawicki, Siemens
Platforms for Building an Industrial Metaverse
Virtual system design can reduce dependency on prototype hardware and provide all engineers with virtual access to a system at any stage of the product development cycle. Of course, digital twins aren’t just about representing the system – they’re also about evaluating design and operational alternatives that may save time and/or cost by accurately simulating what happens when a change is made.
“The definition of digital twin has evolved from the traditional meaning from the NASA days,” says Jim Tung, a MathWorks Fellow. “It’s not only a digital representation of an asset in operation that reflects its current state. It is also using models of the asset at various stages of its development. For over 20 years, we’ve called that approach model-based design, where you use models to make better design choices, interact with real-time models to validate requirements, combine other models for virtual integration, and generate production code automatically.”
“When those models are then tuned to represent the system as it operates, that reuse is powerful,” Tung continues. “It’s not just to show the current state, it’s also to simulate that system in many possible scenarios. That’s why predictive maintenance is so hot. It involves how the asset would perform in potential situations. So, simulating the system throughout development and in operation is how we think about the value propositions of digital twins.”
Accurately simulating physical behavior can be extremely challenging and requires advanced tools to refine virtual models. MathWorks, for example, provides system modeling and simulation capabilities for digital twins[3]. Their Simulink platform can model, simulate, and analyze complex virtual systems comprised of physical hardware, embedded software, algorithms, and the environment in which the system(s) operate (Figure 2).
[Figure 2. Tools like MathWorks’ Simulink can refine virtual system models to accurately simulate physical behavior.]
To support optimal decision making and actions, digital twin systems require continuous and recursive process refinement through the exchange of information, including the information flow from sensing systems to AI and machine learning systems to actuation systems. Simulation models like those run by Simulink can iteratively refine themselves by considering expanded information sets to explain and predict real-world outcomes. This even extends to the science of Uncertainty Quantification.
Ultimately, smart products will be tested, delivered, and provisioned with a digital twin that connects to other digital twins in an industrial metaverse, optimizing value and minimizing risks to end customers in complex system deployments. NVIDIA Omniverse is an example of a scalable platform for federated, interoperable digital twin ecosystems that operate within the “industrial metaverse.”
Omniverse is a multi-GPU enabled development platform for building and operating 3D simulations. It also supports AI tools that enable the creation of mobile virtual elements that are capable of replicating what is happening in physical reality. Ecosystem software partners can leverage Omniverse alongside NVIDIA’s other various technologies. One example being a recent partnership with Siemens to create a photorealistic, physics-based industrial metaverse; combining Omniverse with Siemens’ Xcelerator and Simcenter tools will form a digital twin platform for industrial use cases.
Omniverse is based on Pixar’s Universal Scene Description (USD) – an open-sourced software framework for collaboratively constructing 3D scenes. USD is extensible so that multiple data sets from physical (like a building, robot, or sensor) or virtual assets can be combined without colliding into one another. This allows for extreme collaboration through design, operation, and maintenance that can be easily updated. The platform also retains calculated state values from within asset simulations so you can playback and mesh engineering data to predict results. For instance, it allows you to determine what happens if an asset is dropped at a moment in time or adjust the force from an impact.
Solving Social and Economic Challenges at Scale
A multi-level system of systems based on a distributed system architecture can enable holistic understanding, optimal decision-making, and effective action. Architectures like this can evolve into scalable mechanisms that support the flow of actionable information produced and consumed by connected, state-based systems.
The National Digital Twin programme (NDTp) run by the Centre for Digital Built Britain (CDBB) is an example of a government initiative to develop an ecosystem of connected digital twin systems that foster better outcomes for society and a national economy. Initial activity focused on aligning industry and government behind a common definition and approach to information management so that data could be shared openly and securely between future digital twins – at scale.
The initiative, which concluded this year, had several working groups spanning technology infrastructure to economic and environmental policy research, all with the aim of using the industrial metaverse to solve the world’s most complex problems (Figure 3).
[Figure 3. Ecosystem of connected digital twins and CPS within an industrial metaverse (Source: CDBB)]
Over the next several years, multiple digital twins developed separately in areas such as urban mobility, energy, environment, disaster prevention, and healthcare will be connected and their underlying data mutually linked. We will then have federated systems in a digital space that allow us to rehearse complex scenarios such as how urban transport and energy supplies could be affected by a large-scale disaster. This would allow us to prepare prompt and appropriate responses to systemic risks. It will also help us simulate the impact of climate change and future pandemics.
Whether you call this an industry paradigm shift or revolution, there is little doubt that the industrial metaverse and connected digital twins are critical components to drive solutions for our most complex industry, economic, and social problems.
In part 3, we will explore models that enable interoperability among connected digital twins in an industrial metaverse. Read part 3 here: https://embeddedcomputing.com/technology/software-and-os/os-filesystems-libraries/industrial-metaverse-blueprints-part-3-system-interoperability-requirements
Marcellino Gemelli is Director of Business Development at Bosch Sensortec GmbH. He received the ‘Laurea’ degree in Electronic Engineering at the University of Pavia, Italy while in the Italian Army and an MBA from MIP, the Milano (Italy) Polytechnic business school. He is currently based in Sunnyvale (CA) USA, responsible for business development of Bosch Sensortec's MEMS product line. He is also responsible for Bosch’s regional Automotive Electronics unit. He previously held various engineering and product management positions at STMicroelectronics from 1995 to 2011 in the fields of MEMS, electronic design automation, and data storage. He was contract professor for the Microelectronics course at the Milano (Italy) Polytechnic from 2000 to 2002.
Brian Harrison is Senior Director of Software Product Management of Digital Twins for Omniverse. He's been with NVIDIA for over 10 years, working in a variety of areas involving the manufacturing market and tech marketing, in addition to his work with the Omniverse team. Prior to NVIDIA, Brian worked for a number of software companies in the CAD arena: CADKEY, PTC, and SOLIDWORKS.
Andrew Macleod is Senior Director of Technology Communications at Siemens. He has more than 20 years of experience across the semiconductor, EDA, and industrial software industries, with expertise in applications engineering, new product development, and global market strategy. He earned a 1st class honors engineering degree from the University of Paisley in the UK, and lives in Austin, Texas. Follow him on Twitter @Macleod_DISW.
Doug Migliori is Global Field CTO at CloudBlue, an Ingram Micro subsidiary and global enabler of Everything-as-a-Service (XaaS) marketplaces and ecosystems. Doug has over 20 years of IT consulting experience, applying innovative strategies to digital transformation that leverage digital twin, IoT, AI, mobile, DLT, and cloud/edge native technologies. As an interoperability thought leader, Doug developed an ontology-based event-driven architecture (OBEDA) for highly distributed, real-time systems. He is co-author of the System Interoperability Framework whitepaper published by the Digital Twin Consortium.
Curt Schwaderer has served as Embedded Computing Design’s Technology Editor for more than 25 years and is a veteran of the networking and embedded systems industries. With a track record of identifying disruptive technologies and their timely application to solving real-world problems, he has led software architecture, design, and implementation teams at Wind River, RadiSys, Microware, and IP Fabrics, a company he co-founded that was later acquired by Yaana Technologies where he currently serves as Vice President of Engineering.
Brandon Lewis is Editor-in-Chief of Embedded Computing Design where he guides content strategy and community engagement across the property’s print, digital, and events ecosystem. With more than a decade of experience in the electronics media industry, he has published countless technical articles and news stories while also launching well-known multimedia platforms such as Dev Kit Weekly, Embedded Toolbox, and the Embedded Insiders podcast.
References:
- [1] Capgemini: Enabling Digital Twins with Systems Engineering. https://www.capgemini.com/gb-en/insights/expert-perspectives/enabling-digital-twins-with-systems-engineering.
- [2] Siemens Comprehensive Digital Twin Enabler Model for Model Based System Engineering (YouTube). https://www.youtube.com/watch?app=desktop&v=JmU5vGl-epI&themeRefresh=1
- [3] MathWorks[A1] : MATLAB & Simulink Solutions. https://www.mathworks.com/solutions/system-design-simulation.html
- [4] Digital Twin: the Future is Now – Joe Sawicki - YouTube
- https://www.youtube.com/watch?v=8wmWYLSnwdQ