Industrial Metaverse Blueprints, Part 3: System Interoperability Requirements
December 06, 2022
Story
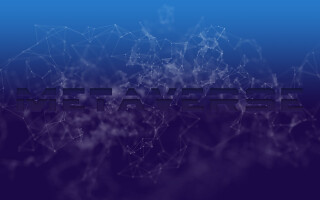
The third article in our metaverse series focuses on conceptual and metadata models that enable interoperability among connected digital twins in an industrial metaverse.
The concept of digital twins, taken to its ultimate potential, can create digital representations of nearly everything. Yet, much of the value of digital twins depends on the ability of distributed, heterogeneous systems to interoperate.
For context, a 2015 McKinsey report estimates that achieving interoperability in IoT would unlock 40 percent more value in the total available IoT market (Figure 1).
[Figure 1. Interoperability is projected to unlock almost 40 percent more value from the IoT (Source: McKinsey Global Institute).]
The Open Group Architecture Framework (TOGAF) defines interoperability as the ability to provide and accept services from other systems, and use those exchanged services to help the systems operate more effectively together. This definition can apply to interoperability between digital twin, cyber-physical, and autonomous systems.
The TOGAF methodology provides a common enterprise architecture and terminology for effective cross-discipline execution of key business objectives. But zooming out, a key challenge is enabling system interoperability across different industries since each has its own environments and use cases. Common conceptual models can help simplify cross-domain interoperability.
A Model-based Approach to System Interoperability
A conceptual model is an abstract representation of a system that uses concepts to model its structures and behaviors. Conceptual models are critical to understanding systems and how they interoperate with other systems.
Within the Levels of Conceptual Interoperability Model (LCIM) developed by the Virginia Modeling Analysis and Simulation Center, conceptual interoperability represents the highest level of interoperability that supports composing a system of systems (Figure 2). The LCIM has been successfully applied not only in the domain of modeling and simulation, but more generally to model-based interoperability challenges. Thus, a common conceptual model is required to support system of system composability and interoperability.
[Figure 2. Conceptual interoperability is the highest abstraction of system interoperability according to the Levels of Conceptual Interoperability Model (LCIM) (Source: Virginia Modeling Analysis and Simulation Center).]
Developing a common conceptual model for a composable and interoperable system of systems requires a high level of abstraction utilizing top-level concepts. It requires a universal metamodel for interoperability that can be applied simply to all system models, regardless of data type and without sacrificing any of the information they contain.
When all systems share a common metamodel for encapsulating internal behaviors, capabilities, and purpose, they become inherently interoperable.
A Top-Level Ontology for an Industrial Metaverse
While a metamodel is a model in which concepts and relationships are represented in a prescriptive way, an ontology is a descriptive model representing reality by a set of concepts, their interrelations, and constraints. An ontological metamodel for system design can lead to more cohesive and structured modeling efforts with an overall increase in scalability, usability, and unification of pre-existing models.
To realize the true potential of the industrial metaverse, industry consortia must properly align their data models, ontology concepts, and terminology with the goal of defining a top-level ontology (TLO) that provides a common core (Figure 3). Promising work on a TLO is evolving from collaborating members of the Digital Twin Consortium, Industry IoT Consortium, TM Forum, and Airport Council International. In many aspects, this work is a continuation of the distributed system architecture discussed in the Cross-Industry Semantic Interoperability article series that tied event-driven services to a TLO.
[Figure 3. Aligning Business and Device Interoperability consortia.]
A TLO describes the relationship between several metamodel concepts, starting with the core concepts of class and attribute (Figure 4). All other concepts are a type of class with unique attributes.
[Figure 4. A Top-Level Ontology (TLO) for systems of systems Interoperability in the industrial metaverse.]
Each class can represent a category of like things or objects that can be uniquely identified. Attributes are based on data types that are primitive (e.g., number) and compound (e.g., temperature), with units of measure associated with quantitative data types. A class or subclass can be defined to reflect the attributes unique to its objects (instances), and attributes can describe value restrictions and relationships between classes.
The relationship between several of a TLO’s top-level classes – including assets, parties, contracts, places, offers, and events – can support cross-industry commercial ecosystems and enable the simulation and optimization of virtual systems of systems within an industrial metaverse. While it is likely impossible to anticipate every concept that may be represented within the industrial metaverse, a TLO can define a standardized set of “primitive” concepts through a collection of top-level classes. A hierarchy of subclasses can then be used to create any of the more specific concepts that might be needed for a given industry or environment.
However, most models and libraries produced by industry consortia do not claim to be based on a formal TLO and have instead been developed pragmatically over years and validated through practice. The Metaverse Standards Forum formed in June 2022 to align the requirements and priorities of different standards development organizations (SDOs) developing and deploying metaverse interoperability standards. For example, consortia can leverage the Forum to conduct pragmatic, action-based projects that speed adoption of common conceptual models and TLOs, which can be achieved by abstracting and decomposing disparate data models within guiding principles like the seven key concepts of the Digital Twin Consortium’s System Interoperability Framework (outlined in Part 1).
Describing Services Using Common Capability Models
Before autonomous or digital twin systems can interoperate, they need the ability to understand the capabilities of their services and dynamically connect based on the current context. As defined in the OASIS Reference Model, a service can be considered an access mechanism to a capability, but a service can also be “described” based on its capability.
The concept of capability can be defined as “the ability to do something”. Although simple, it is a powerful concept, as it can be used to provide an abstract, high-level view of a product, system, or organization, offering new ways of dealing with complexity. It has been widely adopted in many areas, including in system engineering, where capabilities are seen as a core concept. The concept is considered particularly relevant for the engineering of complex systems-of-systems, which relies on the combination of different systems for achieving a particular emergent capability.
Within a metamodel, a capability can be defined by associating an action (e.g., sense or sensing) to a concept (e.g., temperature). This is described in Figure 5.
[Figure 5. A Capability class consists of an Action verb or noun and Concept.]
For example, sensing capability (provided by a sensor) offers the ability to sense an aspect of the physical world in the form of measurement data. Information from sensor observations may be provided to other systems via an information transfer capability, allowing other systems to use their capabilities to manage and analyze the information. An actuation capability, provided by an actuator, offers the ability to actuate a change in the physical world as directed by a control capability.
Beyond a set of top-level actions, a class hierarchy can create any of the more specific actions that may be needed for any given industry or environment. Each action comprises a unique set of attributes (aligning with the Action concept of Schema.org). For example, a sense action can comprise a value range (minimum, maximum) and precision (step). A capability (e.g., sense temperature) inherits the attributes of its action (Figure 6).
[Figure 6. A class hierarchy can comprise a range of actions, each with their own set of attributes to meet the requirements of any given industry or environment.]
A service can be described by applying specific values to the inherited attributes of its capability. For example, a temperature sensing service may have a sensing range from -10 to 60 degrees Celsius, with a precision of 0.5 degrees. These “features” and limitations can be described using a “model” for a sensing capability.
When these capabilities are defined and modeled by a standards organization, every service based on these standard capabilities becomes inherently interoperable and interchangeable. These standardized capabilities can be offered as services by multiple systems and enable the composition of an interoperable system of systems comprising services tailored to its specific requirements.
A system can comprise multiple capabilities, and each capability can be offered as a service to other systems in exchange for some value. In ArchiMate, a service is defined as a unit of functionality (capability) that a system exposes to its environment, while hiding internal operations, which provides a certain value.
Composing a Dynamic System of Systems
In the industrial metaverse, systems will dynamically connect and interact in real-time, forming and re-forming interdependent and interoperable systems of systems. Each “constituent” system is “independently operable” but can be dynamically connected when needed to achieve a certain higher goal.
Complex systems-of-systems rely on the combination of different systems for achieving an emergent capability. These systems need the ability to connect based on current context and understanding of their own capabilities. This requires a “matchmaking” mechanism enabling both information and value exchange that does not rely on prior knowledge.
Utilizing a universal metamodel for system interoperability, all capability-based services can be described through a system’s metadata, which can be shared and understood by other systems. These services can include primary capabilities (e.g., temperature sensing) as well as supporting capabilities (e.g., data communication, money transfer) enabling both information and value exchange.
Complementary to the concept of capability is the concept of intent, which specifies what a system, or the party it represents, wants to achieve. Intent allows a system to express requirements to other systems that may be capable of fulfilling those requirements.
For example, System Y may have a requirement for a temperature sensing capability offered as a service by another system. System Y can express its requirement as an intent, which includes the values and value ranges of the primary and supporting capabilities it requires. A matchmaking (or composition) service can identify a participating System X within a network (or marketplace) with capabilities that best match the requirements (Figure 7).
[Figure 7. A digital service marketplace can enable system intent to be matched with constituent system capabilities.]
Systems must be able to express requirements in a way that recognizes capabilities but does not involve details on how those capabilities are realized, enabling constituent systems to understand and act on them. It must allow dynamic changes in the requirements and separate the required capabilities from their realization.
When a service initiates a connection between two systems, metadata from each system, including service attributes, can be shared to define a contract. The contract between the connected systems, and their responsible parties, specifies the rights and obligations associated with services of each system and establishes parameters for interaction (Figure 8).
[Figure 8. Provider, requester, and Service data schemas enable interoperability between systems requesting and delivering services.]
A multi-level system of systems, based on intent and capability matching, can enable frictionless dynamic interactions and information sharing for optimal decision-making and actions that drive high-value outcomes.
Real-Time Insights and Reactions through Event Sharing
Systems can be composed of event-driven services that allow for real-time communication, enabling information to be exchanged in the form of events. These events reflect object state changes that can be synchronized between systems.
Today, event data from smart products and automation systems is currently stored and communicated in many different formats and lacks semantic information to provide adequate context. Without context, a time-consuming normalization effort is required before that data can be utilized by advanced systems to effectively generate value.
To be universally understood, contextual events should be coupled to a clearly defined, standardized, and federated ontology for distributed systems. A universal event format can provide a “lowest common denominator” for distribution of system and object state changes.
Each event within a universal event format can represent a state change of a single attribute, which enables one event format to be utilized across any ontology class. The schema can include traditional time series elements (time and value) and metadata identifiers for ontology elements (attribute, class, and object) as shown in Figure 9.
[Figure 9. A commom event schema should include time-series and metadata elements for each ontology class being represented.]
A universal event format coupled with a common ontology can effectively support the semantic heterogeneity of events in large and open implementations, including supply chains, smart cities, and an industrial metaverse. It provides event consumers with the minimal information necessary to react to any state change occurrence.
This design pattern can support an overall architecture that is simple, scalable, and sustainable.
Optimizing Outcomes in Real and Virtual Worlds
In the evolution of the industrial metaverse, the virtual and physical worlds will seamlessly interact to optimize business operations and deliver immersive customer experiences.
As an executable virtual representation of the physical system, the digital twin system consumes learnings and experiences from real-world processes to update the digital twin model, intelligently connecting it to the cyber-physical system in real-time. Properly abstracted, a universal TLO and common event-driven services can support real-time information exchange between interoperable digital twin systems in a virtual world, cyber-physical systems in the real world, and distributed edge-to-cloud systems bridging both worlds (Figure 10).
[Figure 10. Common event formats can allow digital twins to reflect the current state of and invoke changes to cyber-physical systems in the real world.]
Together with digital twins, all contextualized event data can be aggregated and expanded to enable total simulation of the system of systems that represent an entire virtual environment. This allows visualization and testing of how the individual parts of complex systems work together and can eliminate risks prior to physical system implementations.
This approach to solution design will enable smart product OEMs and solution providers to differentiate through intelligent services built on a foundational layer of conceptual interoperability. When integrated with intelligent services, these interoperating systems have the potential to create optimized outcomes within an industrial metaverse.
In part 4, we will explore how a metamodel for composability and interoperability is utilized to compose a digital-twin powered smart airport.
References:
- The Levels of Conceptual Interoperability Model: Applying Systems Engineering Principles to M&S (arxiv.org)
- Automation Support for Security Control Assessments. Volume 1: Overview (nist.gov)
- Cross-industry semantic interoperability, part one - Embedded Computing Design
- “Digital Twin System Interoperability Framework”, Digital Twin Consortium, December 2021.
- Creating autonomous networks with intent-based closed loops - Ericsson
- A Framework for the Composition of IoT and CPS Capabilities - NIST
- Future of Applications: Delivering the Composable Enterprise (gcom.cloud)
- (PDF) Modelling Capabilities as Attribute-Featured Entities (researchgate.net)
- The Industrial Internet Reference Architecture v1.10, Industry IoT Consortium, November 2022
- Debate:"Are vendor platforms creating roadblocks for interoperability and realization of the digital engineering vision?", Digital Twin Consortium, November 2021
- An ontological metamodel for cyber-physical system safety, security, and resilience coengineering, June 2021
- An ontological metamodeling framework for semantic simulation model engineering, June 2020
Marcellino Gemelli is Director of Business Development at Bosch Sensortec GmbH. He received the ‘Laurea’ degree in Electronic Engineering at the University of Pavia, Italy while in the Italian Army and an MBA from MIP, the Milano (Italy) Polytechnic business school. He is currently based in Sunnyvale (CA) USA, responsible for business development of Bosch Sensortec's MEMS product line. He is also responsible for Bosch’s regional Automotive Electronics unit. He previously held various engineering and product management positions at STMicroelectronics from 1995 to 2011 in the fields of MEMS, electronic design automation, and data storage. He was contract professor for the Microelectronics course at the Milano (Italy) Polytechnic from 2000 to 2002.
Brian Harrison is Senior Director of Software Product Management of Digital Twins for Omniverse. He's been with NVIDIA for over 10 years, working in a variety of areas involving the manufacturing market and tech marketing, in addition to his work with the Omniverse team. Prior to NVIDIA, Brian worked for a number of software companies in the CAD arena: CADKEY, PTC, and SOLIDWORKS.
Andrew Macleod is Senior Director of Technology Communications at Siemens. He has more than 20 years of experience across the semiconductor, EDA, and industrial software industries, with expertise in applications engineering, new product development, and global market strategy. He earned a 1st class honors engineering degree from the University of Paisley in the UK, and lives in Austin, Texas. Follow him on Twitter @Macleod_DISW.
Doug Migliori is Global Field CTO at CloudBlue, an Ingram Micro subsidiary and global enabler of Everything-as-a-Service (XaaS) marketplaces and ecosystems. Doug has over 20 years of IT consulting experience, applying innovative strategies to digital transformation that leverage digital twin, IoT, AI, mobile, DLT, and cloud/edge native technologies. As an interoperability thought leader, Doug developed an ontology-based event-driven architecture (OBEDA) for highly distributed, real-time systems. He is co-author of the System Interoperability Framework whitepaper published by the Digital Twin Consortium.
Curt Schwaderer has served as Embedded Computing Design’s Technology Editor for more than 25 years and is a veteran of the networking and embedded systems industries. With a track record of identifying disruptive technologies and their timely application to solving real-world problems, he has led software architecture, design, and implementation teams at Wind River, RadiSys, Microware, and IP Fabrics, a company he co-founded that was later acquired by Yaana Technologies where he currently serves as Vice President of Engineering.
Brandon Lewis is Editor-in-Chief of Embedded Computing Design where he guides content strategy and community engagement across the property’s print, digital, and events ecosystem. With more than a decade of experience in the electronics media industry, he has published countless technical articles and news stories while also launching well-known multimedia platforms such as Dev Kit Weekly, Embedded Toolbox, and the Embedded Insiders podcast.