Common Blind Spots in Data Acquisition System Design
July 27, 2020
Story
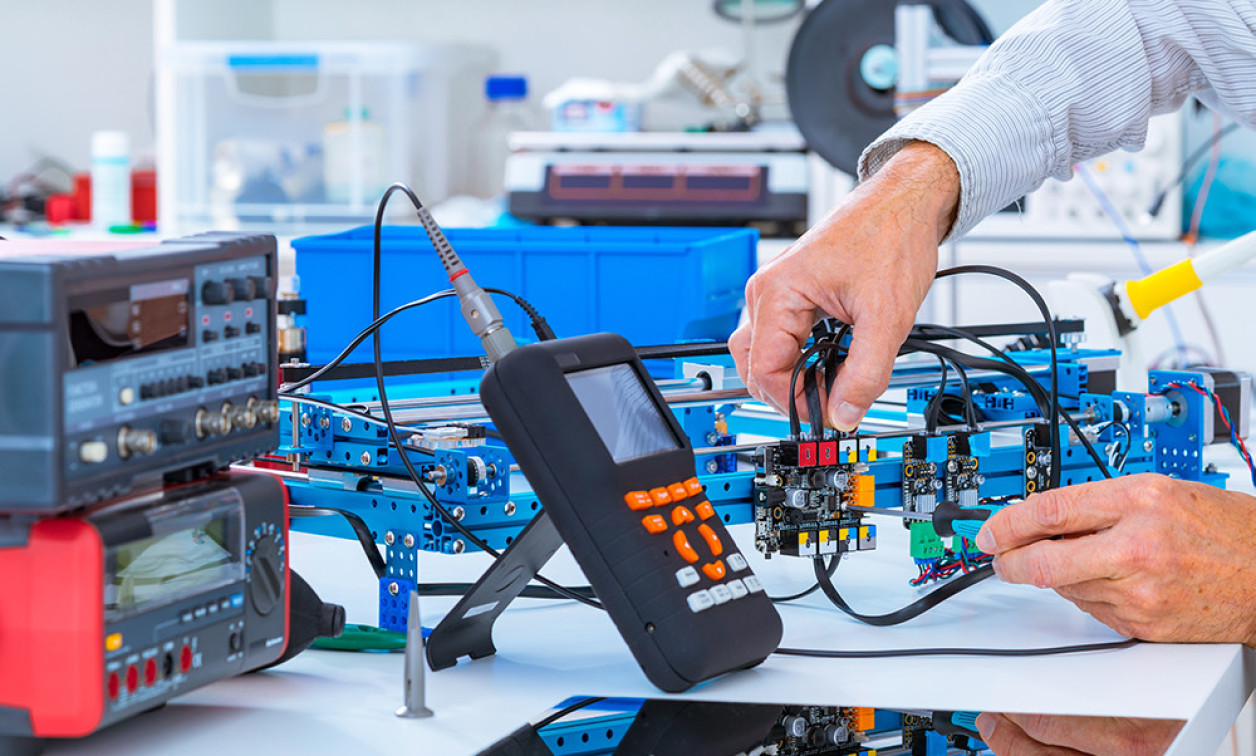
Most data acquisition systems require calibration, sometimes even more than once during a product's lifetime.
Nuvation Engineering has completed hundreds of complex electronic designs over the past 20 years. We asked Mark Bingeman, one of their Engineering Managers, “If you were going to give product development advice to experienced companies, what would you talk about?” Mark posed the question to his senior staff and they identified avoidable issues they have encountered during client projects. This “Blind Spots” article will put a few of these under a magnifying glass and provide some considerations that should be included early on in engineering planning.
Data Acquisition Systems Calibration
Most data acquisition systems require calibration, sometimes even more than once during a product’s lifetime. Precise calibration ensures that a device consistently behaves predictably and with the level of accuracy needed to ensure target outcomes. During the early stages of engineering planning it is important to assess the level of complexity that may be involved in the system calibration process, and the degree of precision required to ensure the outcomes the device must deliver. If this assessment is not performed up front and with sufficient diligence, the result can be that it must be retroactively designed for at later stages of the project. This can lead to an expansion of the project scope and duration, or even require an expensive redesign. At Nuvation Engineering we define system calibration requirements up front during the earlier project planning phases, ensuring that the system architecture includes robust support for calibration.
Understanding the Underlying Physics
Most data acquisition systems consist of one or more sensors that convert an environmental measurement (e.g. light, sound, pressure, temperature, etc.) into an electrical signal that can be conditioned by an Analog Front-End (AFE) circuit and then sampled by an Analog to Digital Converter (ADC). It is important to have a general understanding of the underlying physics of these systems in order to identify the environmental or electrical conditions that can affect the precision, accuracy, and repeatability of the sensor measurements. While a detailed understanding of the applicable area of physics is rarely required, a high-level understanding is very beneficial. Once the fundamentals are understood, strategies can be developed to mitigate environmental or electrical impacts on sensor measurements and performance.
For example, Nuvation Engineering had to understand the electromechanical properties of a flow cytometer device for a life sciences application. The system required a high-speed and high-precision analog front end with a low noise floor. System calibration was essential to meet the measurement performance requirements.
Calibration Procedure
It is important to define the calibration procedure early in the product design phase. This includes asking high-level questions such as:
- Will special equipment be needed to perform calibration?
- Will calibration be performed only in the factory, or also in the field?
- How often will calibration need to be performed?
- Will the calibration require user assistance, or can it be performed internally (i.e. with no user interaction)?
- What measurements need to be performed in the calibration procedure, and how will the product architecture provide access to these measurements?
- How can the calibration results be verified?
- What are the pass/fail criteria for the calibration?
Considering the answers to these questions is the first step in designing the calibration procedure and ensuring that the product architecture can accommodate calibration.
In some cases, the calibration procedure requires special equipment and needs to be performed at the production facility. For example, Nuvation Engineering designed a stereoscopic camera for a retail analytics application. The camera required alignment of the image sensors and lenses to ensure proper stereoscopic imaging. Nuvation developed and provided a calibration test fixture to the production facility, where it was used to perform alignment during volume production.
Calibration Data Handling
In addition to defining a calibration procedure, calibration data handling also needs to be addressed. This includes the calibration process, start-up configuration, run-time operation, post-calibration tracking, and data analytics. During the calibration process measurements are obtained and calculations are performed to obtain run-time parameters for the data acquisition system. The electronic design team must analyze the complexity of these calibration calculations and determine whether they can be performed by the device itself or if they need to be performed by an external computer. If the calculations will be performed externally the design must account for data bandwidth, processing latency, and data encryption and security.
Normal operation of a data acquisition system typically starts with a device configuration stage. During this stage parameters are retrieved from non-volatile memory and used to configure the system. Error-checking and parameter range checking are required to confirm that parameters have not been corrupted in memory.
During run-time operation of a data acquisition system, health-monitoring is required to confirm that the system is operating within expected ranges. Warnings and error-handling procedures must be defined to handle scenarios where internal parameters or environmental conditions exceed their expected ranges. For example, if the internal device temperature changes (relative to the calibration temperature) can the system compensate for this change (e.g. in the analog front-end or in the data processing after analog-to-digital conversion)? At what temperature thresholds should user warnings or error messages be issued? Should the system take preventative steps to try to prevent potential hardware damage if certain environmental or internal parameter thresholds are exceeded?
Nuvation Engineering had to implement critical preventative measures when designing a data acquisition system for a satellite. Although the conditions inside a satellite are different from that of the harshness of outer space, the environment is still considered to be harsh, and high reliability design is a mission-critical requirement. Nuvation’s engineers included extensive self-diagnostic features to ensure the system was continuously operating within the designed operational conditions. If a situation arose that could potentially lead to hardware damage, Nuvation’s designers had the device initiate preventive actions to safeguard the system, such as shutting down sensitive electronics until safe operating conditions had been restored.
In addition to the calibration data usage by the data acquisition hardware, external data handling also needs to be considered. Will calibration results be stored in an external database? What kind of data analytics will be performed on the calibration database? Can the data be used to predict maintenance issues, or to schedule factory re-calibration?
Calibration data can also play an important role in warranty claims. Data acquisition systems can have delicate sensors and other components that require operation within defined environmental or electrical ranges. Operation outside of these ranges can impact performance or cause damage to the hardware. Calibration and health-monitoring data can be used to determine if equipment has been operated outside of specified operational ranges and is therefore not eligible for a warranty claim.
Conclusion
Calibration plays an important role in data acquisition systems. Key factors to consider include:
- Understanding the underlying physics that drive the need for calibration
- Defining the calibration procedure
- Designing the system architecture to accommodate calibration
- Exploring the use-case scenarios for calibration data
Factoring these considerations into the early design phase of an electronic design project ensures that the calibration portion of the data acquisition system development effort does not negatively impact the overall project schedule and budget. With over 20 years of experience in electronic design, Nuvation Engineering has encountered all the common pitfalls of engineering projects and developed processes to ensure they are avoided. This learning has resulted in an impressive track record of First Time Right electronic designs.
About the Author
Mark Bingeman is an electrical engineer with 20 years of experience in FPGA-based image processing, hardware architecture, system design and project management.
He holds a Master’s degree in Electrical Engineering from the University of Waterloo and is currently working at Nuvation as an Engineering Manager.