Programmable Power Management in the World of IoT
December 14, 2022
Blog
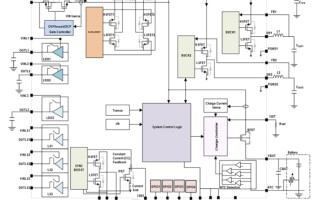
IoT devices have proliferated, with around 13 billion installed globally today, and that figure is expected rise to nearly 30 billion by 2030, according to Statista [1]. In terms of market value, that’s over a trillion US dollars in 2022.
There are a few drivers to further acceleration in adoption, such as better interoperability between disparate devices and mobile apps by using the new ‘Matter’ protocol, now overwhelming supported by all tiers of manufacturers. Another driver is ability to function on batteries for a useful period of time – some of the advantages of IoT are lost if devices need local AC mains to operate or need batteries replaced regularly, especially in industrial and commercial applications where installation and labor costs are counted. For devices with ethernet connections, Power over Ethernet was a solution, but with wireless communications now the norm for cost savings, this option has receded. Power consumption needs to be managed such that an installed battery will last the expected device lifetime, ten years being an accepted figure. To put a scale to this, if the device is powered from a single Li-Ion AA battery with a typical capacity of 2Ah, it needs to draw an average of less than 12µA or 43µW from the 3.6V cell for a ten-year life.
For other personal applications, such as wearables, charging or replacing a battery may not be such an imposition, but often only button cells with their low capacity can be used because of size constraints, so again, power draw must be minimized and run-time maximized to make the device attractive.
Power Reduction Schemes
A typical IoT device comprises a processor, interfaces to sensors, memory, and a wireless module. For processors, various techniques can be employed to reduce power, one being the ability to initially configure the component to activate just the minimum number of functions necessary for the particular application and thereby minimize the number of active core gates. Energy used is generally reduced by using configurable hardware extensions to the CPU and also by lowering clock frequency. This could limit functionality, so dynamic CPU clock frequency changes are implemented ‘on-the-fly’ according to processing demand. Additionally, ‘idle’ or ‘sleep’ modes can be implemented when no processing is required. ‘Light sleep’ mode might suspend the CPU and internal clock while ‘deep sleep’ might disable everything except perhaps a real-time clock and circuitry to react to a ‘wake-up’ call.
Similarly, a lower CPU supply voltage results in lower dynamic and static leakage losses, but also decreases processing speed, so active schemes to apply ‘Dynamic Voltage Scaling’ are used to tailor voltage to the functionality required.
Memory in the IoT device consumes power, which can be traded against energy used by the wireless function. With the increased implementation of ‘edge’ computing for IoT in industry (IIoT), where pre-processing and aggregating of data is performed at the IoT device, fewer transmit/received cycles are needed for central processing, typically in the ‘cloud’. As the transceiver module is usually the most power-hungry element, the overhead of a little extra power in local RAM during read/write cycles in local processing is worthwhile. Memory power can be minimized again by implementing sleep modes and scaling supply voltage dynamically to the minimum necessary.
The transceiver module could use a variety of protocols from 3/4/5G to Wi-Fi, Bluetooth, Zigbee, and several more. Data throughput is generally traded against power consumption, with LoRA/LoRaWAN and NM-IoT for 1+ km range generally being the lowest, but with data rates less than 1 Mbps. For short range, Bluetooth LE and Zigbee are favored for their lower power consumption compared with Wi-Fi for example. Figure 1 shows some comparative figures for Bluetooth, Bluetooth LE, Zigbee, and Wi-Fi modules, data taken from [2] and [3] values depend on exact configuration of the devices but give an indication of the differences in power consumption.
Figure 1: Relative power consumption of popular network technologies
Generally, limiting transmission activity to aggregated data and limiting ‘push’ notifications is recommended to reduce power. For example, data could be sent when a change is detected rather than continuously, such as motion detection triggering a security camera to record.
Complicating all of the mechanisms to reduce power is the number of rail voltages required, typically from sub-1V for a CPU core, 1.8V for I/O, 3V for Flash memory and perhaps 5V for the transceiver module.
Power Management is Necessary for Long Battery Life
To achieve the appropriate generation of supply rails with enabling, sequencing and dynamic scaling in an IoT device optimized for low power, a new component class has appeared, the ‘PMIC’ or Power Management IC. An example is the ACT81460 from Qorvo [4] (Figure 2).
Figure 2: A Power Management IC optimized for low power IoT devices, Qorvo part ACT81460
The Qorvo device includes four DC-DC converters with integrated power FETs, three low-dropout regulators (LDOs) and three separate load switches. Two of the DC-DC converters are step-down buck regulators, one is a step up/down buck-boost regulator and the fourth is a high voltage step-up boost regulator capable of providing up to 20V. Each regulator can be configured for a wide range of output voltages through an I2C interface. The supply to the ACT81460 is 4V - 5.5VDC or alternatively from a Li-Ion battery at 2.7V - 4.5V. The PMIC controls charge to the battery using an Active Power-Path Linear Charger (APLC) which can provide up to 0.8A using battery temperature and voltage feedback for an optimum charge profile. Trickle, pre-conditioning and fast charge modes are also featured for different initial battery charge states. Current consumption from the battery can be as low as 2.1µA with the switching regulators disabled, while still having internal references and monitors enabled. With all regulators and load switches enabled but unloaded, quiescent current is 6µA. The part includes four general-purpose GPIOs, is highly configurable, and supports dynamic voltage scaling through its I2C interface. The ACT81460 is available in a tiny 3.33 x 3.28 49-ball WLCSP package to fit into the smallest of applications, which include low-power battery-only IoT nodes as well as higher powered portable devices that can be connected to chargers when convenient.
For an even smaller package but with higher output current ratings, Qorvo also offers their ACT88420 device (Figure 3).
Figure 3: The Qorvo ACT88420 PMIC
In a package just 2.693mm x 2.693mm, the part includes four buck converters with ratings up to 4A, two LDOs, which can be configured as load switches and eight configurable GPIOs. In full shutdown, supply current is typically 0.1µA and typically only 10µA in standby, sleep or deep sleep modes. External inductors are required for the buck converters but these are very small, each 470nH, due to the high switching frequency, up to 2.25MHz. As with the ACT81460, the ACT88420 is highly configurable through its GPIOs and I2C interface and is also supported by the Qorvo “ActiveCiPSTM” dongle which, when connected to the device evaluation board, allows user configuration and monitoring through an intuitive GUI without any special software or firmware. When default parameters are chosen for a particular end-system, the user can upload the configuration to Qorvo, who then ship parts pre-programmed with the desired functionality. With high output current capability, the part is targeted at higher-power IoT components such as solid-state drives, FPGAs, computer vision systems, and portable audio/video. However, with its ultra-low standby consumption, it is also suitable for lower powered products with life-time battery power.
Conclusion
As IoT devices have spread into all areas of our lives, their value and effectiveness are increasingly defined by how long their batteries last. Attempts to manage power consumption with discrete solutions inevitably result in standing losses that are too high and occupy significant board space. However, use of PMICs solves the problems with micropower consumption and footprints that fit the smallest of applications.
References
[1] https://www.statista.com/statistics/668996/worldwide-expenditures-for-the-internet-of-things/
[2] International Journal of Internet of Things 2017, 6(1): 9-13, DOI: 10.5923/j.ijit.20170601.02
“Comparative Study of Communication Interfaces for Sensors and Actuators in the Cloud of Internet of Things”; Olaide O. Kazeem, Olubiyi O. Akintade, Lawrence O. Kehinde
[3] https://www.raytac.com/product/ins.php?index_id=31
[4] www.qorvo.com