Overcoming the Technical Challenges of Electrochemical Gas Sensing: Part 2
December 31, 2019
Story
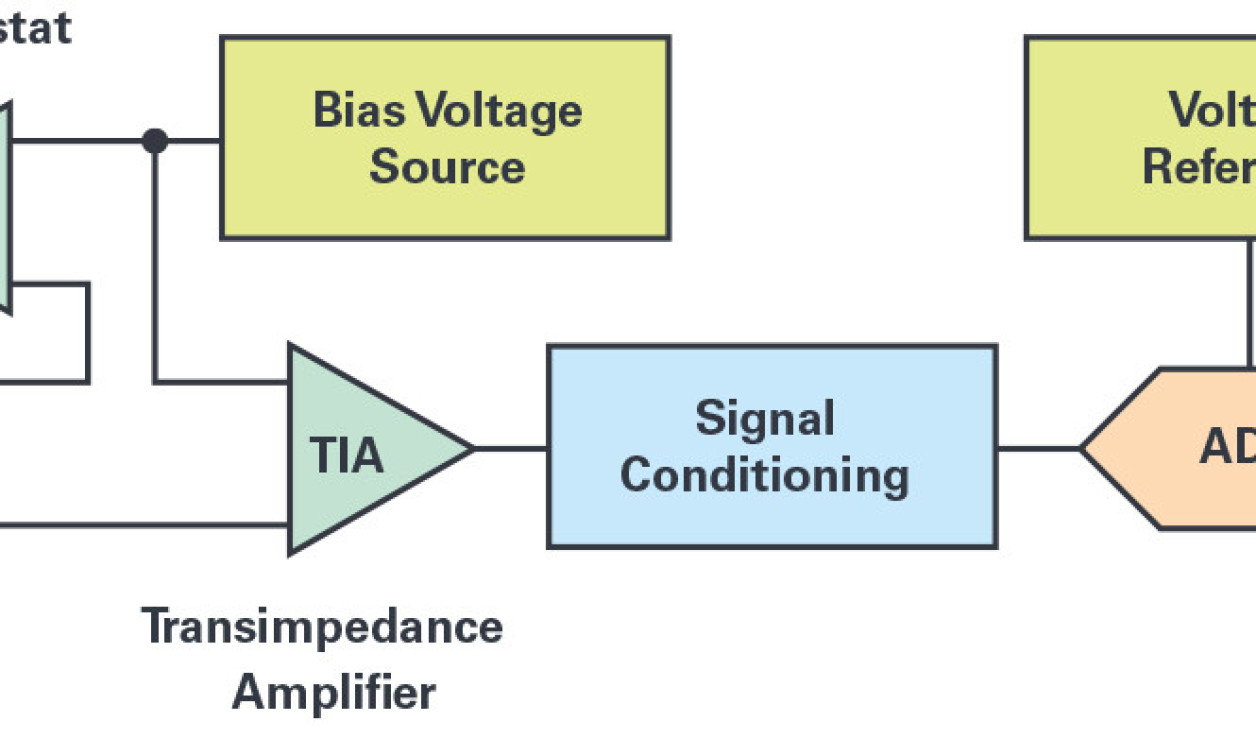
While signal chain integration is a significant step forward, on its own it does not address the fundamental disadvantage of electrochemical gas sensors?deteriorating performance over their lifetime.
Sensor Deterioration and Diagnostics
While signal chain integration is a significant step forward, on its own it does not address the fundamental disadvantage of electrochemical gas sensors—deteriorating performance over their lifetime. Understandably, this is happening as a result of the sensor’s working principle and construction. Operating conditions also contribute to the performance loss and accelerate sensor aging. Sensor accuracy decreases until it becomes unreliable and no longer suitable to fulfil its task. The usual practice in this case is to bring the instrument offline and inspect the sensor manually, which is both time consuming and expensive. Depending on its condition, the sensor then can be either recalibrated and used again, or it might have to be replaced. This incurs considerable maintenance costs. By utilizing electrochemical diagnostics techniques, it is possible to analyze sensor’s health and effectively compensate for the performance changes.
Figure 1. Typical electrochemical gas sensor signal chain (simplified).
Figure 2. Dual-channel integrated gas sensing signal chain (simplified).
Figure 3. The correlation between sensor sensitivity (left graph) and impedance (right graph) during accelerated lifetime test in low relative humidity.
Common factors contributing to the performance deterioration include excessive temperature, humidity and gas concentration, or electrode poisoning. Short exposure to increased temperatures (over 50°C) is generally acceptable. However, repeatedly stressing the sensor in high temperatures can cause electrolytes to evaporate and inflict irreversible damage to the sensor, such as causing an offset in baseline readings or slower response time. Very low temperatures (below –30°C), on the other hand, significantly decrease the sensitivity and responsiveness of the sensor.
Humidity has by far the greatest influence on the sensor’s lifetime. The ideal operating conditions for an electrochemical gas sensor are 20°C and 60% relative humidity. Ambient humidity lower than 60% causes the electrolyte inside the sensor to dry out, affecting the response time. On the other hand, humidity higher than 60% leads to water from the air being absorbed into the sensor, diluting the electrolyte and influencing sensor’s characteristics. Additionally, water absorption can cause the sensor to leak, potentially leading to corrosion on the pins.
The aforementioned deterioration mechanisms influence the sensor even if their magnitude is not extreme. In other words, the electrolyte depletion, for instance, occurs naturally and contributes to sensor aging. The aging process limits the sensor life regardless of the operating conditions, although some EC Sense gas sensors could be operating for time periods exceeding 10 years.
The sensor can be analyzed using techniques such as electrochemical impedance spectroscopy (EIS) or chronoamperometry (pulsing the bias voltage while observing the sensor’s output).
EIS is a frequency domain analytical measurement made by exciting an electrochemical system with a sinusoidal signal, commonly a voltage. At each frequency, the current flowing through the electrochemical cell is recorded and used to calculate the impedance of the cell. The data is then presented as, most commonly, Nyquist plots and Bode plots. The Nyquist plot shows the complex impedance data, where each frequency point is plotted by the real part on the x-axis and imaginary part on the y-axis. The major shortcoming of this data representation is losing the frequency information. The Bode plot shows impedance magnitude and phase angle vs. frequency.
Experimental measurements have shown a strong correlation between declining sensor sensitivity and change the results of the EIS test. The example in Figure 3 shows the results of an accelerated life test where an electrochemical gas sensor was stressed in low humidity (10% RH) and increased temperature (40°C). Throughout the experiment, the sensor was periodically pulled out from the environmental chamber and allowed to settle for an hour. A baseline sensitivity test with a known target gas concentration and the EIS test were then carried out. The test results clearly demonstrated the correlation between sensor sensitivity and impedance. The disadvantage of this measurement might be its length, as obtaining measurements at low, sub-Hz frequencies is very time consuming.
Chronoamperometry (pulse test) is another technique that can aid with sensor health analysis. The measurement is done by applying a voltage pulse superimposed on the sensor bias voltage, while observing the current through the electrochemical cell. The pulse amplitude is generally very low (for example, 1 mV) and short (for example, 200 ms), so that the sensor itself is not disturbed. This allows the test to be performed quite frequently, while maintaining normal operation of the gas sensing instrument. Chronoamperometry can be used to check if the sensor is physically plugged into a device, and also as an indication of change in sensor performance, before performing the more time-consuming EIS measurement. An example of sensor response to the voltage pulse is shown in Figure 4.
Figure 4. Example result of chronoamperometry test.
The previous sensor interrogation techniques have been used in electrochemistry for decades. However, the equipment required for these measurements is usually expensive and bulky. From both a practical and financial perspective, use of such equipment is simply not viable for testing a large number of gas sensors deployed in the field. In order to enable remote, built-in sensor health analysis, the diagnostics features must be integrated directly as part of the signal chain.
With the integrated diagnostics, it is possible to autonomously test gas sensors without the need of human interaction. If the gas sensors are characterized in production, the data obtained from a sensor can be compared to these characterization datasets and provide insight into the current condition of the sensor. Smart algorithms will then be used to compensate for loss in sensor sensitivity. Furthermore, recording the history of the sensor might then enable end of life prognosis, alerting the user when the sensor needs replacement. Built-in diagnostic features will, ultimately, reduce maintenance needs of gas sensing systems and prolong the operating life of a sensor.
System Design Challenges of Industrial Applications
Especially in an industrial setting, safety and reliability are paramount. Strict regulations are in place to ensure that gas sensing systems meet these requirements and maintain reliable, full functionality when operating in harsh industrial environments such as chemical factories.
Electromagnetic compatibility (EMC) is the ability of different electronic devices to function properly, without mutual interference, in a common electromagnetic environment. Tests involved in EMC are, for instance, radiated emissions or radiated immunity. While the emission testing studies the unwanted emissions of a system to help reduce them, the radiated immunity test examines the system’s ability to maintain its functionality in the presence of interference from other systems.
The construction of an EC gas sensor itself has a negative impact on EMC performance. The sensor electrodes act like antennas that can pick up interference from nearby electronic systems. This impact is even more notable in wirelessly connected gas sensing devices, such as portable worker safety instruments.
EMC testing is usually a very time-consuming process that might, eventually, require iterating the system design before the requirements are finally met. This testing contributes significantly to the cost and time invested into product development. Both time and cost expenses could potentially be reduced by using integrated signal chain solutions that have been pretested to meet EMC requirements.
Another serious consideration, and also a technical challenge, is functional safety. By definition, functional safety is the detection of a potentially dangerous condition that results in activation of a protection or correction mechanism to prevent any hazardous events. The relative level of risk-reduction provided by this safety function is then defined as the safety integrity level (SIL). Functional safety requirements are, naturally, captured in industrial standards.
The importance of functional safety in industrial gas sensing applications relates most frequently to a safe operation in environments, where the presence of explosive or flammable gases is possible. Chemical plants or mining facilities are a good example of such applications. To comply with the functional safety standards, a system must be qualified as functionally safe at a satisfactory safety integrity level.
Single-Chip Electrochemical Measurement Systems from Analog Devices
To address the aforementioned challenges and enable customers to design smarter, more accurate, and competitive gas sensing systems, manufacturers are integrating sensor interfaces and other functionality into microcontrollers. For example, the ADuCM355 from Analog Devices is a single-chip electrochemical measurement system targeted at gas sensing and water analysis applications (see Figure 5). It integrates two electrochemical measurement channels, an impedance measurement engine used for sensor diagnostics, and an ultra low power, mixed-signal 26 MHz ARM Cortex-M3 microcontroller for running user application and sensor diagnostics and compensation algorithms. Other important capabilities of a sensing microcontroller are integrated ADC, DACs for generating the bias voltage for electrochemical cells, low power and low noise potentiostats with TIA amplifiers, and an integrated temperature sensor.
Integrating analog hardware accelerator blocks (i.e., waveform generator, digital Fourier transform block, digital filters) also simplifies sensor diagnostic measurements such as electrochemical impedance spectroscopy and chronoamperometry. The system can be run compensation algorithms, store calibration parameters, and run user application, all on the same MCU. MCUs should be designed with EMC requirements in mind and be pretested to industry standards, such as EN 50270.
Figure 5. Simplified functional block diagram of the ADuCM355.
The availability of two measurement channels supports not only the most common 3-electrode gas sensors, but also the 4-electrode sensor configuration. The fourth electrode is used either for diagnostic purposes, or, in case of dual gas sensors, as a working electrode for the second target gas. Any of the potentiostats can also be configured to hibernate to decrease the power consumption, while maintaining the sensor bias voltage, thus reducing the time sensors might need to settle before proper operation. For applications where an integrated microcontroller is not necessary, there are front-end only chips available, such as the AD5940.
As a result of technological innovation, we now have all the necessary knowledge and tools to effectively deal with the technical challenges that have, up until recently, prevented electrochemical gas sensors from entering the era of ubiquitous sensing. From low cost, wireless air quality monitors to process control and worker safety applications, signal chain integration and built-in diagnostic features will enable widespread usage of these sensors, while reducing the maintenance needs, improving the accuracy, prolonging the sensor lifetime, and lowering the cost.
About the Author
Michal Raninec is a systems applications engineer in the Industrial Systems Group within the Automation and Energy Business Unit at Analog Devices. His areas of expertise include electrochemical gas sensing and wireless sensor networks. Michal received his M.Eng. degree in electronic engineering from Brno University of Technology, Czech Republic. He can be reached at michal.raninec@analog.com.