The Perplexities of Predictive Maintenance: Understanding the Anatomy of a Workflow
February 19, 2019
Story
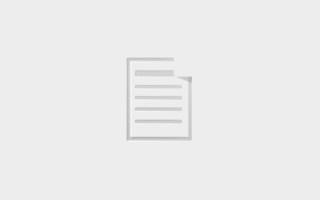
We will explore three common obstacles engineers face when implementing predictive maintenance, and ultimately how to best avoid them, beginning with the fundamental lack of knowledge.
Predictive maintenance enables companies to reduce machine downtime, eliminate unnecessary upkeep, and achieve many other business benefits. However, companies often face challenges around process and data when incorporating the technology into their operations.
This blog series will explore three common obstacles engineers face when implementing predictive maintenance, and ultimately how to best avoid them. We begin with the fundamental lack of knowledge surrounding the anatomy of a predictive maintenance workflow.
Benefit Your Business by Understanding Workflows
Many engineers haven’t been properly educated on predictive maintenance workflows and how to best leverage them. This could be because the company has yet to realize the value of such an investment, is unable to see past the risk of that investment or considers predictive maintenance too advanced for current business needs.
Regardless of the reason, there are concrete steps you can take to minimize risk and get started with predictive maintenance workflows as quickly as possible. The first step to getting started is to understand the five core development stages of predictive maintenance (Figure 1):
- Access sensor data – Data can be gathered from multiple sources such as databases, spreadsheets, or web archives, but must be in the right format and organized correctly for proper analysis. It’s important to remember, however, that large data sets may require out-of-memory processing techniques.
- Preprocess data – Real-world data are rarely perfect; there are outliers and noise that must be removed to obtain a realistic picture of normal behavior. Additionally, because statistical and machine learning modeling techniques are used later in the process, the quality of those models will be dependent on the quality of the preprocessed data.
- Extract features – Instead of feeding sensor data directly into machine learning models, it is common to extract features from the sensor data. While the number of features that can be extracted from data is essentially unlimited, common techniques come from domains such as statistics, signal processing, and physics.
- Train the model – Build models that classify equipment as healthy or faulty, can detect anomalies, or estimate remaining useful life for components. It’s useful to try a variety of machine learning techniques in this step, as it’s rarely clear beforehand what the best type of model is going to be for a given problem.
- Deploy the model – Depending on the system requirements, predictive models may be deployed to embedded devices or integrated with enterprise IT applications. There are numerous tradeoffs to consider here, as embedded devices provide fast responses and reduce the need to transmit data over the internet, while a centralized IT approach makes it easier to update models in the future.
Figure 1. The basic predictive maintenance workflow. © 1984–2019 The MathWorks, Inc.
The Golden Rule: Go with What You Know
Understanding the various development stages of a predictive maintenance workflow is a vital first step toward implementation, yet the idea of fully understanding, developing, and integrating a workflow seems daunting to many. Engineers can quickly and efficiently incorporate predictive maintenance into their daily routine by leveraging existing tools and software.
Tools such as MATLAB have predictive maintenance capabilities that enable engineers to work in a familiar environment. They also provide reference examples, algorithms, and access to technical support, training, and consulting teams. The additional guidance can get the basics in place, so you and your team can be confident that you approach problems in the best way.
Stay tuned for my next blog, which will explore another common predictive maintenance obstacle engineers face: lack of data. I’ll discuss what you can do when information is limited, and ways to access enough data to build accurate models.
Seth DeLand is the application manager at MathWorks for data analytics. Before that, he was product manager for optimization products. Prior to MathWorks, Seth earned his BS and MS in mechanical engineering from Michigan Technological University.