Semiconductor Manufacturing Survey Reveals Insights to End Chip Shortage
September 07, 2022
Blog
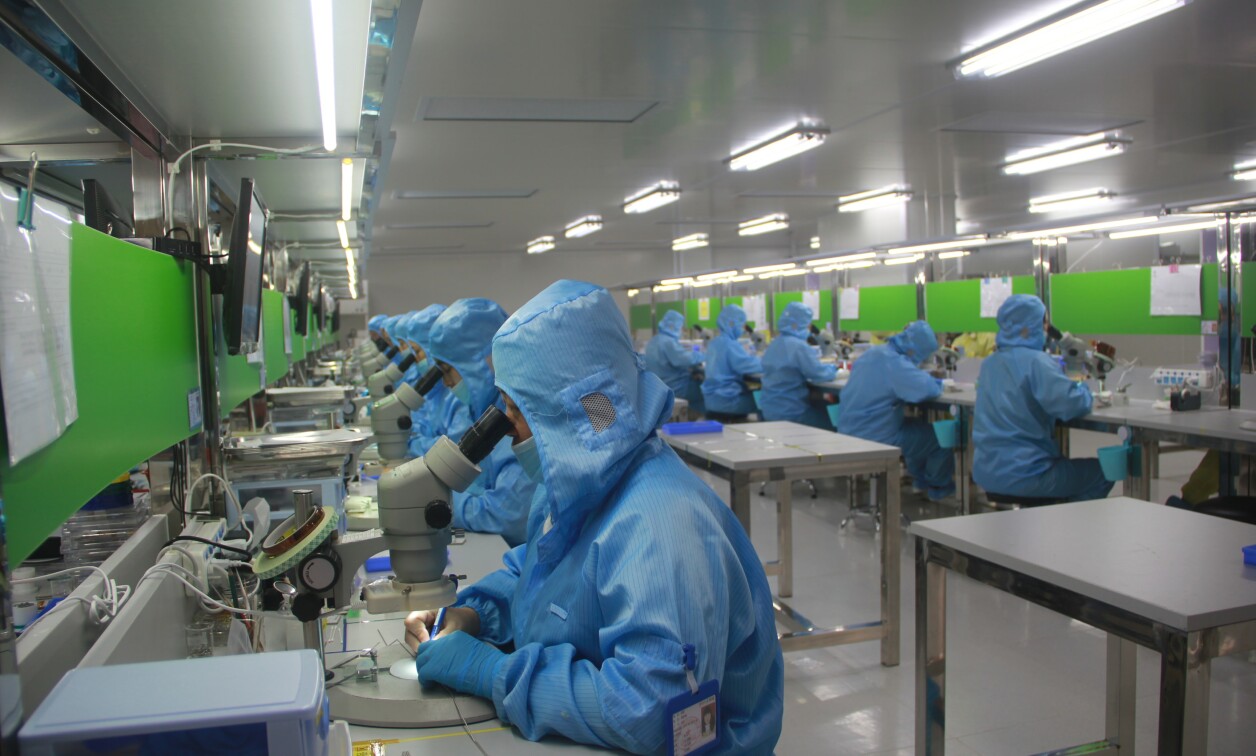
The global chip shortage has become front-page news thanks to a tenuous supply chain exacerbated by a worldwide pandemic. While the semiconductor industry has always intensely focused on ways to increase efficiency, precision, and yield, the urgency to find new and better ways to ramp up productivity has never been higher.
Today, there’s a chorus of voices clamoring for improvement. According to participants in a recent survey conducted by Gigaphoton Inc., professionals in the semiconductor manufacturing chain are also seeking change.
Among the most promising approaches for achieving higher yield within the semiconductor industry is an improvement in advanced analytics capabilities, including cohesively integrating fragmented and siloed processes that inhibit progress. To this end, semiconductor professionals want tools that are easier to use, more intelligent, able to support all their equipment, capable of automated reporting and alerts, and verifiably secure.
The Problem: Siloed Data
Currently, when manufacturers attempt to integrate equipment monitoring performance in search of improved data consolidation and analysis, the results can be lackluster. Even though equipment manufacturers spend millions developing software to support their tools—and chip manufacturers spend equal amounts purchasing software from third-party vendors—neither solution provides a “one size fits all” answer. Instead, chip manufacturers have resorted to creating software solutions themselves and piecing together solutions on multiple, often incompatible platforms. This approach is labor-intensive and time consuming.
As the resources available to any given manufacturer are limited, it can take months to install new features and enhancements that benefit the production line. Even after repeated requests, often the new software capabilities never actually appear. With solutions from multiple vendors in place, the onus is on the manufacturer to contact each individual vendor, update all of the software at play on the production line, and then hope that everything is compatible and works seamlessly together. Using multiple platforms with proprietary code bases only creates barriers to getting the required analytics capabilities and intelligence when needed, which is increasingly “right now.”
(Fig. 1: The Gigaphoton survey provides insights into the current challenges facing the semiconductor manufacturing industry.)
Survey participants have identified another barrier to progress: most of the analytics tools accessible to semiconductor professionals offer basic descriptive and diagnostic features, but they don’t effectively address predictive and prescriptive maintenance.
Predictive maintenance uses statistical and modeling techniques to determine what may happen in the future based on historical data and attempts to determine when a machine needs servicing.
Prescriptive maintenance, while less prevalent and well developed, takes analysis a notch higher. It not only predicts equipment failure events, but it can recommend actions. In the future, prescriptive analytics powered by artificial intelligence (AI) could even assist maintenance teams by providing detailed instructions that improve the manufacturing process in real-time.
Only a small number of chip manufacturers surveyed have software capable of performing the most advanced predictive (14%) and prescriptive (12%) analytics. Moreover, the effort it takes for engineers to pull data, clean it, and analyze it is incredibly costly and time-consuming, leading to less uptime. Even when chip manufacturers have multiple software solutions in place, the majority do not have access to advanced analytics capabilities that could increase efficiency and improve yield in meaningful ways.
(Fig. 2: The four levels of possible insights provided by analytics tools range from descriptive to prescriptive.)
The Solution: Integrated Insights and Industry Collaboration
Semiconductor manufacturers may operate using a variety of proprietary processes, but today’s industry professionals share a common goal: they want accurate analytics on a single, user-friendly platform that can standardize and unify all data from all vendors.
It's a tall order, but it’s not impossible. One solution that would allow for both enhanced integration and industry collaboration would be a single, open software platform that would allow chip manufacturers to streamline data analysis and collaborate with equipment vendors on secure, custom solutions. If such a platform could ensure that vendors’ intellectual property (IP) would be inherently secure, the platform would allow cross-vendor equipment monitoring and analysis to be performed while enabling each vendor to solve for their specific problems.
An open platform should be equipped with significant security features so that users could create custom solutions and keep vendor-specific IP secure. It would also require an agnostic approach to programming languages, easily accommodating all or most of them. Such a platform would allow chip manufacturers to apply analysis and AI-based solutions to any group of processes or equipment in the production line. It could also be fully customizable, from the dashboard to data management to analytics and intelligence. The result would be efficient, seamless workflows that are tailored to the unique needs of each chip manufacturer.
This open platform solution concept would serve the semiconductor industry in multiple ways:
- Eliminate the need to rely on products from multiple sources by streamlining data management and analysis on one platform
- Reduce downtime and service calls by leveraging prescriptive maintenance
- Increase efficiency and yield by putting AI models to work
It is conceivable that an open platform, such as the recently released Fabscape, could ultimately become an industry standard for monitoring analytics in the semiconductor industry. An open platform could become a secure collaborative solution to give a community of users and chip manufacturers the ability to leverage the experience of others who have solved similar problems.
(Fig. 3: A rendering of Fabscape, a new open platform concept that aims to bring together streamlined data monitoring, management, and analytics across the production line.)
Conclusion
The semiconductor manufacturing industry currently suffers from a fragmentation of monitoring and analysis. This fragmentation hinders the industry’s ability to respond to supply chain challenges in a timely manner, and further complicates the internal goals of semiconductor professionals by forcing them to rely on incomplete analytics and siloed software solutions.
To increase productivity on an industrywide scale, semiconductor manufacturing would be well served by a platform where all analytics, fault detection, optimization, and communication occur in a single place and with the depth of insight that only vendor-specific intelligence could provide. An open monitoring and analytics framework could go a long way toward integrating insights and fostering a spirit of collaboration that benefits the entire industry.
About the Author:
Yuji Minegishi is the General Manager at Gigaphoton Inc., a manufacturer of light sources for semiconductor lithography processes. He is responsible for the company’s Digital Transformation department where he leads the engineering and development efforts responsible for launching Fabscape®, one of the semiconductor industry's first truly open software platforms for developing manufacturing factory equipment monitoring, maintenance, and data analysis applications.