Monitor Your Smart Building to Maximize Equipment Life, Lower Costs
April 25, 2022
Sponsored Story
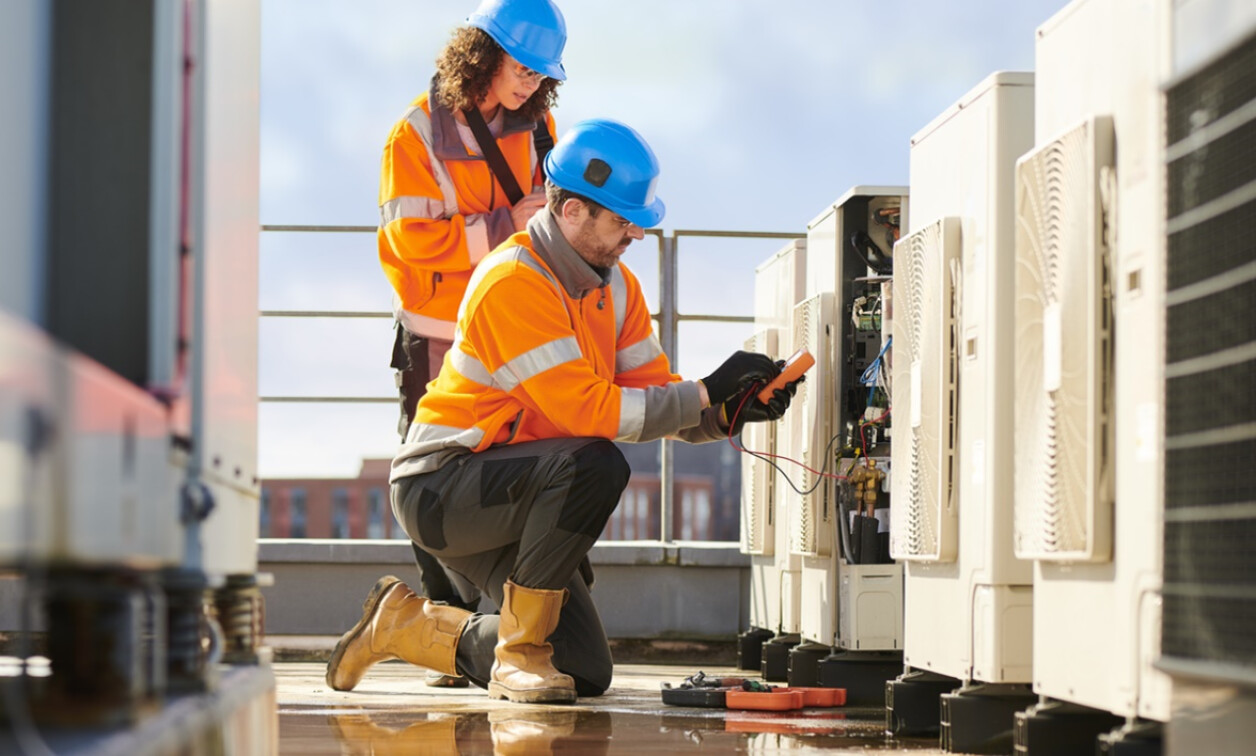
Conditioning monitoring and predictive maintenance are two techniques that can be figurative life savers for building managers and administrators. The terms also apply to the home, the smart home, that is, but let’s start with the description for smart buildings.
There’s nothing secretive or super-complex about conditioning monitoring. It’s pretty much what it sounds like—knowing the condition of your building’s equipment at all times. That means when the equipment is brand new, when it’s been on-line for a while, and when it’s in need of maintenance. In some instances, we’re talking about equipment that’s been in place for many years or even decades. Hence, you could be installing the sensors and controllers for condition monitoring as new equipment is installed, or retrofitting them into current, potentially older, equipment.
Conditioning monitoring is a prerequisite for predictive maintenance. You take in data through sensor fusion, for example, in an HVAC system you would likely look at the filter, how the motor is behaving, and the temperature at various locations. And, in some smart buildings, you could even look at the air quality (learn lots more about the components required for industrial HVAC systems here).
For sensor fusion, an MCU gathers the data and, if needed, performs basic edge-computing techniques to filter data and send to cloud if required. The PSoC™ 6 family of MCUs are suited for this task. They are available with two cores, an Arm Cortex M0+ to manage system security (like Secure Boot or Secure Firmware Updates) and an Arm Cortex M4 that can gather sensor data and perform the edge compute before the data is sent to the cloud.
Conditioning monitoring will also require reliable connectivity if data is being transmitted to the cloud. This can be solved by using a high reliable Wi-Fi SoC like the CYW4373 that offers extended temperature range.
With this data, taken at various points in time, you can implement predictive maintenance. The advantages of such a system include less down time, the ability to manage equipment remotely, and lower overall costs.
The responsibility for condition monitoring falls into multiple domains, including the equipment supplier, the contracted maintenance company, the building operator, the building owner, and/or the user of the equipment. At the end of the day, each stakeholder should see value in condition monitoring and later, predictive maintenance.
Implementing predictive maintenance works best when paired with machine learning, either at the Edge, where the equipment resides, or in the Cloud. There are advantages and disadvantages of each implementation. Keeping everything local is simple if you’re just looking to check stats and figures and manually manage the equipment. In that case, no Cloud connection is needed, which has the added benefit of making the system more secure (more on that later).
Many providers already have a system in place whereby you send them your data, via the Cloud, and they can handle the predictive maintenance (through machine learning) for you. Obviously, there’s a cost involved for this. If you’re dealing with lots of equipment in multiple buildings spread across several locations, this would likely be the optimal way to go. The Cloud would retain your condition monitoring database, so predictive maintenance would be relatively easy.
Infineon can assist in both the condition monitoring, thanks to its extensive sensor line, and the predictive maintenance using the company’s components that are aimed at machine learning, which includes the aforementioned PSoC™ 6. In some cases, the equipment manufacturers design the hardware and software into their equipment before it goes out the door. That’s usually the preferred configuration.
Dealing With Already-Installed Equipment
As we know, the installed base of equipment is tremendous, and the likelihood of smart building owners and managers scrapping their working equipment for new equipment that’s equipped with the latest technology is small. That’s where retrofits come into play.
Retrofitting equipment to handle condition monitoring is relatively simple. For example, you could add a microphone to detect the presence of vibration or harmonics from a bent or dust-contaminated fan blade in an air handler. Attaching those sensors with connectivity, e.g., by Bluetooth Low Energy (BLE) or Wi-Fi to the Cloud is not a daunting task, as the sensor and connectivity vendors have made the process simple though their software.
Note that whenever you add an IoT node to a piece of equipment, you are adding an entry point for a hacker; Infineon offers hardware solutions so the security certificates can be implemented in hardware. Those hardware pieces are then used to authenticate the various pieces of equipment in the field. For example, Infineon employs a service called CIRRENT™ Cloud ID where you download your certificates which get loaded into the equipment and used for authentication in a secure hardware manner.
How Much is Enough?
Obviously, nothing comes for free, and that includes the ability to perform predictive maintenance. So, the operator needs to ask himself, how much will I gain from this technology?
It’s important to know what to expect from your equipment, including its current status and any maintenance or problems that can be predicted ahead of time, like changing filters and lubricating machinery. Then, you need to know what kind of data (and how much data) to collect. This would determine the number and type of sensors that are required.
One way to determine when a filter needs replacing is by measuring and monitoring the air flow at the filter, which can be done by a device like the Infineon DPS368 digital barometric pressure sensor, part of the company’s XENSIV™ line of sensors. The tiny device, 2.0 by 2.5 by 1.1 mm, offers very high precision (e.g., altitude calculations down to ±2 cm from pressure measurements) and low current consumption (1.7 µA on average). It can measure both temperature and pressure, the latter handled by capacitive sensing which results in the high level of precision.
Image Credit: Infineon Technologies AG
Smart Homes Reap Benefits, Too
Smart homes would see similar benefits, albeit on a smaller scale because there’s less equipment to monitor and control. The equipment can work either with set patterns, i.e., set the temperature to a particular time each day or turn the lights on or off at a particular time. Or it can simply follow the behaviors of the users. For example, if the homeowner keeps the thermostat set to a particular temperature, the system would learn that.
The home can be a more difficult environment to control, as more “gadgets” get added to the network, operating with different timelines. For example, your HVAC system may have a life expectancy of ten or 15 years. But some other appliance on the network may have a shorter life. And frankly, some of the newer, less expensive devices are not nearly as accurate. In some cases, the home-based sensors offer many “convenience” features, like alerting a home owner that a filter needs to be changed.
In summary, it boils down to three component groups. First is the sensor technology, which provides the relevant information back to the server. The second is the controllers (MCUs) that are needed to take an action based on the information provided by the sensors. As discussed, that processing can either take place at the Edge of the IoT or in the Cloud with remote connectivity of the device. And the third is the security, both hardware and software.