Single Pair Ethernet Steps Onto the Factory Floor
April 07, 2023
Blog
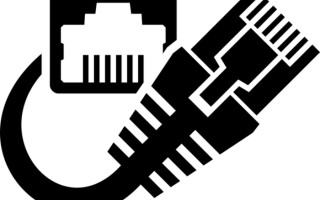
Increasing data rates are usually the primary focus when new data communication protocols are developed. However, many of the countless sensors and actuators operating in industrial and building automation applications need more than fast data rates to work correctly. These edge devices are currently interconnected using a myriad of legacy multidrop protocols, which increase the complexity and cost for original equipment manufacturers (OEMs) in supporting them.
With this in mind, the IEEE established a task force to study how a short-distance networking technology could deliver a data rate of 10 Mb/s over a single pair of Ethernet (SPE) cables to serve the needs of industry 4.0, automotive, and other markets.
Figure 1: Industry 4.0 brings new requirements for industrial networks
This culminated in the 2019 release of the IEEE 802.3cg standard, which now brings the benefits of SPE to the edge.
Setting the Scene for Industrial SPE
While there already existed point-to-point types of single-pair Ethernet that could quickly provide (and surpass) the data rates needed for industrial applications, existing multidrop types could not provide the determinism required by moving robots and actuators to respond to inputs in near real-time. This is because they use carrier-sense multiple access with collision detection (CSMA/CD) to arbitrate access to a shared medium (cable) in a multidrop network.
CSMA/CD exhibits random latencies caused by data collisions, making it impossible to guarantee that a device can transmit and reliably communicate with a receiver within a defined time interval. To address this shortcoming, a new way to regulate medium access control was developed for use in 10BASE-T1S, a network protocol designed to enable multidrop data communication at rates of up to 10Mb/s over cables up to 25 meters in length.
Physical layer collision avoidance (PLCA) guarantees maximum latency in a half-duplex multidrop network. A PLCA transmission cycle begins when a coordinator node (Node 0) sends a beacon, to which other network nodes then synchronize. After the beacon is sent, the option to transmit is forwarded to Node 1. If this node has no data to send, the option is passed to Node 2. This process continues until each node has been given at least one transmit opportunity (TO).
The coordinator node then restarts the cycle by sending out another beacon. To prevent a node from blocking the bus, it is only allowed a certain number of transmitted frames per transmit opportunity, governed by the burst mode setting, which defaults to one frame per transmit opportunity (TO), but can be set to 128 frames per TO. No data collisions can occur on the bus, so throughput is not affected.
Figure 2: PLCA medium access control cycle
Cabling was another barrier to the deployment of traditional Ethernet in industrial settings. Standard Ethernet cables have four pairs of wires, which increases their cost and makes them difficult to install. 10BASE-T1S was developed to work using a single pair of wires, which are smaller, easier to work with, and significantly less expensive.
Apart from real-time performance and determinism, working reliably in harsh and electrically noisy environments is a key requirement for an industrial network. While older Ethernet standards were not designed for electromagnetic compatibility (EMC), 10BASE-T1S was designed with these harsh environments in mind. The result is that 10BASE‑T1S exhibits outstanding EMC performance compared to other industrial networks.
Using 10BASE-T1S, it is possible to design systems that meet Class 3 IEC61000-4-6 EMI requirements (10 Vrms common-mode noise injection) even using unshielded single-pair cables. PLCA is a key contributor to this improved electromagnetic immunity because removing collisions enables a physical layer transceiver to employ advanced techniques that can recover a signal even in the presence of high levels of electrical noise.
SPE at the Industrial Edge
Industrial equipment OEMs and industrial facility operators stand to benefit substantially from 10BASE-T1S in many ways. In factory settings, many communication technologies traditionally connect devices (RS-485, UART) at the physical layer (PHY) and various Fieldbus protocols at the data link layer. These nodes connect everything from temperature and pressure sensors, robotic and HVAC actuators, fans, voltage monitors, power converters, and other modules back to control cabinets at low data rates.
The multidrop capability of 10BASE-T1S allows these devices to be connected to a single shared cable, meaning they can be removed (or replaced) without affecting overall network performance or causing process downtime, thereby greatly simplifying and reducing the cost of network maintenance. Replacing legacy multidrop industrial networks with 10BASE-T1S also eliminates the requirement for large switches, gateways, and protocol translators with the extra wiring and power required to support them.
2-in-1 MACPHY Transceiver
Typical 10BASE-T1S Ethernet PHY controllers only provide the physical layer functions required to transmit and receive data over an unshielded single-pair cable and support communication with a MAC via a standard media independent interface (MII). The NCN26010 (Figure 3) from onsemi is an IEEE 802.3cg compliant Ethernet Transceiver that has been designed to eliminate this two-tiered approach by integrating a Media Access Controller (MAC), a PLCA Reconciliation Sublayer (RS) and a 10BASE−T1S PHY in a single package.
This means it can provide all the physical layer functions required to transmit and receive data over a single unshielded twisted pair and communicate with a host MCU via the Open Alliance MACPHY SPI protocol. Integrating the PHY and MAC on a single MACPHY device allows Ethernet to be used with sensors and other industrial devices with mid- to low-end MCUs that do not have an integrated MAC. This significantly reduces complexity and provides the flexibility to reconfigure nodes after the initial system installation.
Figure 3: The NCN26010 10BASE-T1S transceiver from onsemi
Cloud-to-Edge Connectivity
Ethernet has evolved considerably from its formative years, when it was primarily used to connect computing devices, into its many current guises that allow it to meet the speed and distance requirements of different applications. 10BASE-T1S completes the missing link required for multidrop, deterministic applications on the factory floor and other edge applications.