New technologies reshape production lines
August 22, 2016
Blog
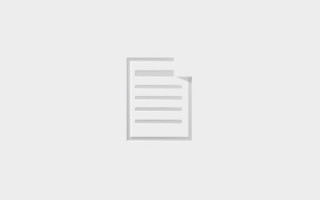
Whether people call it Industry 4.0, Industrial Internet of Things (IIoT), or networked production, they are all talking about coming changing paradig...
Whether people call it Industry 4.0, Industrial Internet of Things (IIoT), or networked production, they are all talking about coming changing paradigms in the industrial network.
Today there are several single-task workstations, manned by humans or robots, which are connected to a higher-level enterprise resource planning (ERP) system. However, that hierarchy is on the cusp of changing massively in the near future to accommodate newer, more intelligent technologies spanning multiple segments of the production line. A single robot or workstation today will no longer be fully locally controlled and just report progress or results (success/fail) of the production step to the overarching ERP system. Instead, it will be connected to the adjacent and other production cells in order to form a part of the complete production process, depending on and responding to the results of the previous production steps. As result, the overall architecture of these systems and the entire production line will need to change, as well as the related interfaces.
The new architecture still consists of the production cells at the bottom, but above this you will find a super-controller that orchestrates the interaction of the different cells, analyzing and acting upon the production step outcome to provide a complete product at the end of the production line, making necessary adjustments in the process to rectify previously undetected or ignored errors that may lead to scrap product. Interconnects here are transitioning to Time-Sensitive Networking (TSN), replacing older field buses in the coming years with Ethernet-only shared media that provides both real time and normal IP connectivity on the same wire and infrastructure. The result is a lower-latency workflow and a significant reduction in manual rework and inspection, which leads to a more efficient manufacturing process.
[Figure 1 | Traditional production line consisting of self-contained cells (e.g., electronics assembly)]
Above the super controller there is a production line controller, which is already found in some of today’s production lines, communicating to the existing ERP system. This controller also takes over the role of today’s simplistic IoT gateway products, as well as cloud functions, to move the data created in the production process to a local entity for analysis rather than a remote cloud. Alternatively, the controller can act as a secure cloud gateway to connect to an offsite cloud, supporting cross-site analysis and the use of Big Data capabilities of external service providers if desired.
With moves towards high-bandwidth interconnects and interconnected production lines that before were arrays of single-step appliances, a change is coming in the industrial production space. Maximizing system processing performance, active use of video to monitor intermediate production results, moving from varieties of different field buses, incorporating load balancing and switching, and the management of multiple APIs and open standards are all part of the system design and integration expertise that vendors with a history of building standards-based communications platforms are delivering to reshape industrial production lines for the IoT.
[Figure 2 | New, interconnected architecture of industrial applications and orchestration.]
Artesyn Embedded Technologies
www.artesyn.com
@ArtesynEmbedded
LinkedIn: www.linkedin.com/company/artesyn
Facebook: www.facebook.com/artesynembedded
YouTube: www.youtube.com/user/artesynembedded