Inductive Position Sensors for Industrial and Transportation Markets
August 07, 2024
Blog
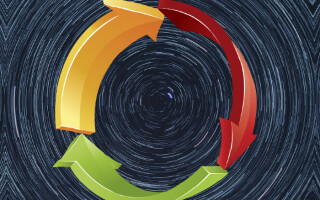
The importance of motion control is increasing as more aspects of our world become automated. To effectively drive a motor, control inputs describing the speed and position are necessary. However, different techniques exist for this sensing, each of which has different attributes and applications.
In this technical article, we will compare the different rotational sensing technologies and discuss why they are chosen. We will then look at some of the latest devices available on the market.
Applications for Position Sensing
The applications for position sensing are growing rapidly as more processes that were previously manual are being automated to achieve higher levels of accuracy, better yield and lower operating costs. In fact, wherever there is some form of motion, there will be a sensor providing position information to a controller.
Industry 4.0 is driving many advances in the sphere of automation in industrial markets. Robotics are becoming more common, allowing for 24/7 ‘lights out’ operation that does not tire or make mistakes – here a sensor is needed for each axis of motion. The same is true for ‘cobots’ that work alongside humans in conventional factories.
These days, many parts are fabricated by machine – either a computer numerical control (CNC) machine, laser cutter or 3D printer. Each of these has moving parts and precise positional control is required to meet quality objectives. Once formed, the materials are often moved by automated material handling or conveyor belts so, again, position sensing is needed.
Outside the factory environment, position control is required for large medical equipment that moves either the patient or the scanner. Also, as robots are now able to perform surgery very precise control is required here.
In the transportation sector, motion is present in every application, and position sensing is found in conventional vehicles such as trains, farm machinery, and construction equipment as well as newer applications such as the autonomous mobile robots (AMRs) found in warehousing – as well as the thousands of drones that are being used.
As passenger vehicles are becoming more electrified, in all forms of propulsion (internal combustion engine (ICE), electric vehicle (EV) and Hybrid) so mechanical control schemes are being replaced with systems such as ‘drive by wire’ and ‘steer by wire’. For these systems to operate the position of the gas pedal (accelerator) has to be communicated to the electronic control unit (ECU), or the steering wheel to the steering control system.
With control spreading to almost all aspects of vehicle operation, position sensing can also be found in suspension components (for leveling and ride control), the powertrain and areas such as electric windows, sunroofs and door locks.
Comparison of Position Sensing Technologies
The three primary technologies available for rotary position sensing are optical, magnetic and inductive – each with different modes of operation, advantages, disadvantages and applications.
Optical encoders are often considered to be the most accurate (although this is not true in all cases) and work by passing light through a disc with holes. As the disc rotates, the light pulses allow motion to be detected.
Typically, these devices are used in applications where the ultimate accuracy is required such as precise robotics and machine tools like CNC lathes or laser cutters. While they are highly accurate and insensitive to magnetic fields, they are sensitive to vibration and dirt on the disc which can render them useless.
Magnetic encoders tend to have lower levels of accuracy and are used mainly in very cost-sensitive applications. They are good where vibration or contamination is present, but they are obviously affected by external magnetic fields, which limits their applicability.
Inductive encoders offer better accuracy than their magnetic counterparts. They are able to handle high levels of vibration and contamination as well as being insensitive to magnetic fields. Other advantages include their repeatability, temperature insensitivity, low component count, small size and the fact that they do not require rare earth materials in the form of magnets.
As automation becomes ubiquitous, there is an increasing need for being able to sense the position of rotary motors. To do this, various technologies exist including optical, magnetic and inductive. Optical offers great precision but is expensive and susceptible to contaminants. Magnetics are low cost but easily influenced by magnetic fields.
Inductive is becoming a preferred choice and with the advent of dual inductive sensors, it is now possible to build sensors that have the capability to deliver optical-level accuracy in a much more cost-efficient manner. For more on inductive motors, visit onsemi.com.