3D Printed Fastening Part 2: Attachment Without Inserts
September 03, 2020
Blog
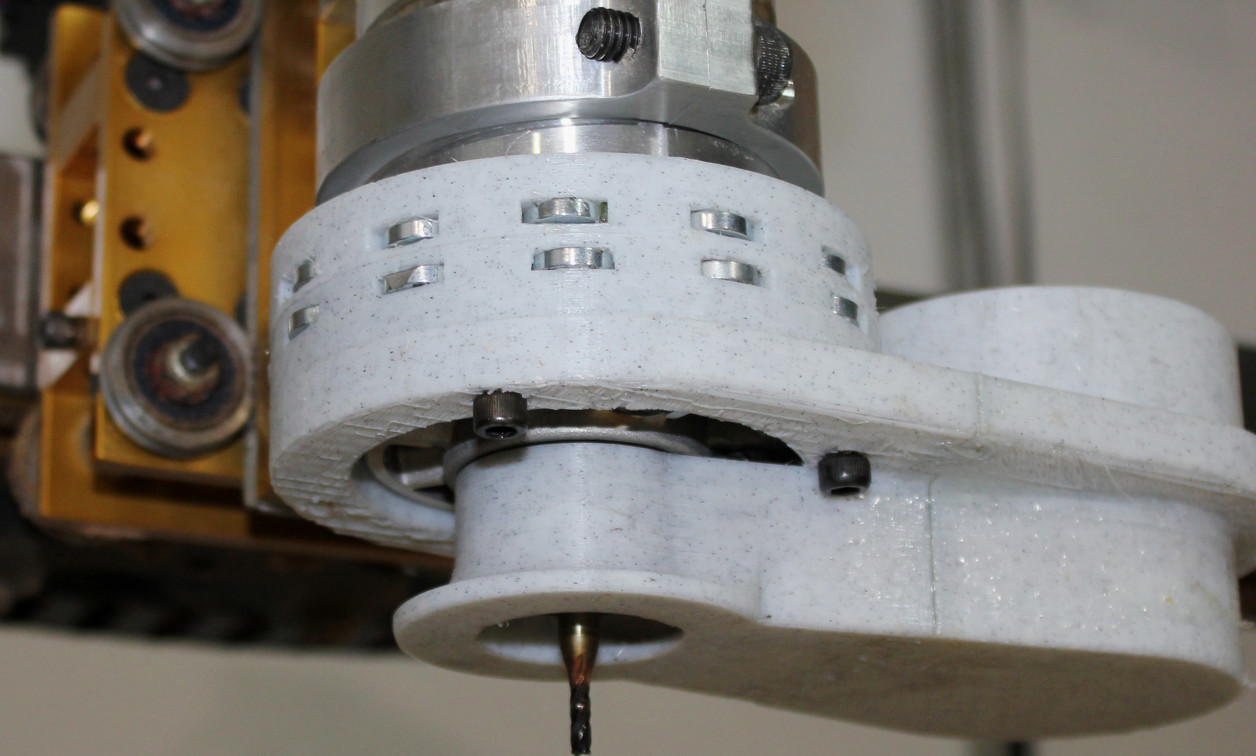
Whether you need high strength, ease-of-printing, or the ability to slide your part back and forth after linking, there are a wide variety of techniques available to finish off your print.
Tapped holes help attach this dust collector to the router
In my previous 3D-printed fastener post, we primarily discussed different insert options for screw attachment. While popular, I have yet to use such techniques, instead opting to form threads and other attachment accommodations into the print itself.
Tap Threads
As noted in the last post, it’s possible to form threads with a screw and an undersized printed hole. I instead normally opt to cut the threads as needed with a tap. While I haven’t tried letting the screw form its own thread, I would guess that the tap gives you a bit more leeway as to how wide the screws can be. One would also assume the strength is different, but which is better would seem to be an open question.
Taking this a few steps further, why bother with creating threads after the fact at all?
Model Threads
FDM printers are amazing pieces of equipment, but are limited in the fine details that they can print. Because of this, I never really considered printing threads until I had trouble properly tapping a relatively large ½ -13 blind hole as seen in the preceding video. Fusion 360 provides accommodations for modeling threads directly according to spec, but you’ll need to select modeled instead of cosmetic so that it actually prints properly.
The potential problem with this is that Fusion360 doesn’t compensate for any extra plastic that your printer extrudes when it converts things to an STL, meaning that your screw may be too tight. One possible solution is to stretch the X and Y axes (or otherwise account for this) in your slicer software, though you’ll need to ensure that this doesn’t unacceptably distort the rest of the model. Another alternative is to model threads directly using a helical sweep operation, though this takes a bit more calculation to get things worked out correctly.
Depending on the size and quality of your print, you may also find it beneficial to tap a thread after printing in order to clean things up.
Zip Ties
While often used to clean up wiring, don’t rule out using a zip tie to attach things together. With modeled holes and slots, I’ve mounted Raspberry Pi computers to two types of fixtures, one of which uses zip ties on the print to allow it to slide back and forth on a wire rack. Another design in the video above uses zip ties to hold two pieces of a Dyson Vacuum support accessory together. This configuration also allows for some horizontal adjustment.
Press Fit, Snap-In, and Print-In-Place
Just snaps in the back like so. Very satisfying that it worked on my first try printing it! pic.twitter.com/GrEwdeIkvN
— Jeremy Cook DIY ? (@JeremySCook) December 11, 2019
When you don’t need a lot of strength, consider either printing something in such a way that one part presses against another when pushed in, forcing it to stay in place. This can be great for box tops or other such items that need to be accessed only once in a while. Another idea is to design tabs into your print, which flex outward during installation, then snap back to keep an item in place. As seen above, I was able to use this with a Particle Internet Button, which I was happy to find worked on the first try!
One final technique, for those that are fairly advanced 3D printing-wise, is to design something to “print-in-place.” This technique designs parts in such a way that when it is printed, several sections are automatically linked together. The Flexi Rex is one example of such a design, and creating this type of a device can be an interesting challenge.
Whether you need high strength, ease-of-printing, or the ability to slide your part back and forth after linking, there are a wide variety of techniques available to finish off your print. What’s presented here gives you several options, and there are certainly other methods waiting to be discovered!
https://twitter.com/JeremySCook/status/1204800785470644226
Jeremy S. Cook is a freelance tech journalist and engineering consultant with over 10 years of factory automation experience. An avid maker and experimenter, you can follow him on Twitter [https://twitter.com/JeremySCook], or see his electromechanical exploits on the Jeremy S. Cook YouTube Channel! [https://www.youtube.com/c/jeremyscook]