Managing risk and changes in outsourced embedded design
April 01, 2015
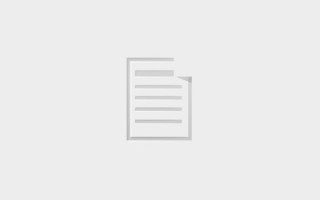
Risk and changes must be carefully managed through any embedded design. Outsourcing embedded design Embedded design is increasingly outsourced in toda...
Risk and changes must be carefully managed through any embedded design.
Outsourcing embedded design
Embedded design is increasingly outsourced in today’s ever-competitive marketplace. To be successful, your own design engineers must focus on their core competency and your company’s unique selling point. Don’t become bogged down in the complex processes involved in converting that key expertise to a physical piece of embedded hardware.
Core competency focus is far from the only motivator, of course; an enthusiasm to reduce cost by paying for expertise per task, rather than have to commit ongoing salary and training to a new employee allows a company to access resource dynamically and efficiently. Additionally, an existing embedded design house allows access to unparalleled industry knowledge that really is worth its weight in gold as gaining an edge on the competition is more critical than ever.
Risk
Outsourcing any part of a project carries risk and as the heart of a product, the embedded design is often the most critical of all – this naturally makes any project manager wary. Your company’s hard-fought brand reputation that you maintain such strict control over is suddenly in someone else’s hands.
To satisfy that natural cautiousness, that Project Manager must first and foremost satisfy himself with the honesty and integrity of the embedded design house. Satisfying your brand’s reputation for quality, punctuality and strict adherence to your provided design specification are all important, but without trust everything quickly unravels.
A project manager assesses the risk based on understanding those fundamentals and selects the operation he feels he can best place his brand’s trust with – now he must strike the careful balance of continuing to manage the delegated task, but without being so involved he perceives it would have been just as much trouble to keep it in house.
Changes
In a perfect world, any design can be defined wholly from its outset and communication prior to an end-of-project review of deliverable vs original design specification unnecessary – but of course this is an impossible dream.
This isn’t necessarily a bad thing, the need to update that design specification can of course be attributed to bad planning, and sometimes is; however, the majority of mid-project design changes are for unanticipated, and positive reasons.
We are all only blessed with the information that is available to us today and, given the complexity of embedded designs, project time-scales can span from months to even years!
Technology and application
Embedded technology is always rapidly evolving and to stay ahead of competitors one must remain at the very forefront of it. Strictly adhering to the original design approach when an alternative now exists to improve performance and/or cut costs, just to avoid ‘rocking the boat’, is rarely a good business decision – though one must exercise some caution chasing new technology, else your product will never be realized!
Technology-based design changes can be driven by the outsourcer, with customers evolving specifications by pushing for new functionality, or even proposed by the design house, having identified new methods to improve manufacturability and drive out unit costs thus increase market competiveness.
Potentially new markets and applications are identified during the project phase, requiring adherence to unanticipated certification requirements – or now that planning has already begun on its successor, introducing new aspects that enable easier migration further down the roadmap.
Parallel mechanical
A new approach to outsourced embedded design, often where the outsourcer’s core competency includes mechanical engineering – is where the enclosure and electronic innards are designed in parallel. This approach is intended to provide a rapid time to market through avoiding serial design processes, but increases risk as the initial specification can look like a high school algebra exam – with X to be defined much later. This requires close integration between mechanical and electronic design engineers, else the constant “stop/start” required due to undefined variables exacerbates rather than expedites progress.
Customer creep
“Customer creep” is a tongue-in-cheek reference describing those making post-specification changes, with the inference of poor initial planning. The reality is such changes should be expected and as long as those changes are managed through an Engineering Change Request system, where design and unit cost alongside effect on time scales are carefully reviewed and approved – the additional success of the designed product is success for all involved.