IoT, IIoT and a lot of noise
July 26, 2016
Blog
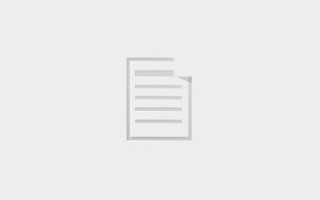
It is easy for a small or medium-sized business to be overwhelmed with all the noise you hear about the Internet of Things (IoT), Industrial Internet...
It is easy for a small or medium-sized business to be overwhelmed with all the noise you hear about the Internet of Things (IoT), Industrial Internet of Things (IIoT), Big Data, machine learning, algorithms, analytics, and artificial intelligence (AI). This further extends to concepts such as digital disruption, digitization, automation, and servitization. We add to these pieces the various technical components of the IoT value chain such as sensors, gateways, MCAT-1 and the hundreds of platforms to feed into a data analytics or actionable information scorecard to influence behavioral change. While the analysts, big company forecasts and futurists proclaim a world of trillions of sensors and a trillion-dollar economic shift in the next twenty years, it’s easy to be overwhelmed in the day-to-day of running your business. There are elements that resonate with you strongly, yet it’s difficult to decipher and distill how to engage in this changing business landscape and make it relevant to you.
To begin, it’s important to understand the changing competitive landscape. Your business, whatever it may be, is to provide a product or service to a customer. If you can provide a better product or service, you are providing more value to your customer. For example, there are plenty of products that have been around for 100 years without changing much at all. By adding connected capability, you can provide alerts to service, replace, or repair before costly downtime or high maintenance costs. This connected capability can create a new service revenue stream, differentiate from competition or just make your customers more satisfied. All industries are experiencing the impact of digitization, and you must move forward to stay relevant.
What’s recommended is to think big but start small. Identify the products that are high enough in value or maintenance costs are high enough to warrant “connecting” them to inform the broader group of requisite people about their health and service schedule. Think pumps, water meters, industrial valves, precision agriculture, farm management, heavy industry, or manufacturing plants. These products may be remote or located on the shop floor or manufacturing plant. It is clear that connected remote products and assets provide optimized route schedules and reduce lengthy downtime, but connected products in the factory or shop floor can connect beyond the local operator to the supervisor or local maintenance technician.
Focus on improving customer service through measurement or monitoring your product and acting on that data. You want to change behaviors, not conduct a science experiment. Think of the entire project from doing an internal audit, deployment and a long-term service integrator of the initiative and not on fancy technology or the latest and greatest gadgets. Convince your leadership and employees that this is to improve customer retention and differentiation, not to replace field, service or factory employees. When you embrace change, it is not just noise – it’s exciting and meaningful.