Why Next Generation Embedded Command, Control, and Data Interfaces Are Key to the Success of Future IIoT Devices
December 09, 2021
Story
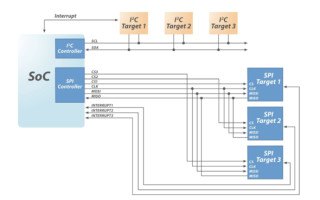
Ever since the creation of the first modern industrial factory systems in the 1770s, industrial manufacturing processes have been subject to continuous innovation, quickly adopting the latest technologies to ensure greater efficiency, productivity, and product quality. This trend continues today with the adoption of connected Industrial IoT (IIoT) solutions into the next generation of industrial processes, driving a step change in productivity across all large scale, repetitive, process-driven manufacturing industries such as automotive, chemicals, electronics, food and beverage, and pharmaceutical, to name a few.
Industry analysts are forecasting that the IIoT market will grow from USD 76.7 billion in 2021 to over USD 106.1 billion by 2026, driven by factors such as technological advancements in semiconductor and electronic devices, increased use of cloud computing platforms, development of 5G connectivity, advances in robotics, adoption of artificial intelligence/machine learning, and government financial stimulus.
Embedded command and control interfaces are at the heart of all Industrial IoT devices
In this article we look at key trends in IIoT device design – particularly the need for higher data bandwidth and ever lower power consumption, and the drive toward miniaturization – and we consider whether current embedded command, control, and data interfaces meet these challenges, or whether a transition to newer interfaces is required.
Example IIoT Devices
All industrial IoT devices, including advanced robots on a manufacturing line, smart tools used by assembly workers, automated guided vehicles in a warehouse or simple monitoring devices that track the condition of materials in a supply chain, are built using microcontrollers, sensors, actuators, cameras, displays, and other basic electronic components. Of equal importance to these basic building blocks are the embedded command, control and data interfaces that link these components together providing the fundamental internal connectivity between peripheral devices and their associated host microcontrollers.
Embedded command and control interface challenges
Many present day IIoT devices use interfaces such as I2C (Inter-Integrated Circuit), SPI (Serial Peripheral Interface), and UART (Universal Asynchronous Receiver-Transmitter), which, over the past 30 years, have become the "go-to" interfaces in the embedded hardware engineer’s toolkit.
Example I2C and SPI Configurations
These interfaces have served the embedded electronics industry well since their introduction in the late 1970s and early '80s. But since that time, several industry advancements, prevalent not only in IIoT but also across the wider electronics industry, have placed increasing pressure on these legacy interfaces:
- Increasing data bandwidths – The total data bandwidth demand on command and control interfaces is being driven up by the combination of two primary factors. First, the number of sensors, actuators, and other peripheral components being built into IIoT devices continues to increase. Devices today not only contain essential components to serve the device's core function, but they also increasingly contain ancillary components to monitor the performance and environment of the device itself to ensure it is functioning properly and performing remote management of the device. Second, the sensors and other peripheral components being built into IIoT devices are becoming increasingly advanced, generating significantly greater volumes of data due to increased sensitivity, accuracy, and sampling rates.
- Need for miniaturization – Compact device designs are essential for many IIoT devices, particularly those that must be unobtrusively accommodated within a pre-existing industrial process. With IIoT devices containing an ever increasing number of peripheral components, it is essential that the number of wires and pins required by the command and control interfaces that connect these components be kept to an absolute minimum.
- Lower power consumption – A key requirement of many IIoT devices is ultra-low power consumption to enable untethered operation from either a battery or other type of constrained power source. It is becoming essential that command and control interfaces are not only power efficient themselves, but are also "smart" – that is, that they can enable the subsystems within a device to power up and down in the most efficient way possible to achieve the lowest possible power consumption by the overall system.
Solving these challenges using industry standardized interfaces
To solve these challenges, developers will need to implement new embedded command, control and data interfaces that provide higher bandwidths, use the minimum number of wires and pins, consume the minimum amount of power, and enable the whole system to minimize its power consumption.
The use of industry standard interfaces, as opposed to proprietary or vendor-led interfaces, can solve these challenges and provide many additional benefits. This has been proven in adjacent industries such in mobile phones, where industry standards for embedded camera and display interfaces have solved similar challenges.
The use of standards in these industries has created economies of scale around interfaces, reducing integration costs and enabling developers to amortize engineering costs over larger volumes of components. Standardized interfaces also promote the availability of enhanced support services such as test and software resources from a wide ecosystem of industry contributors. Standardization also improves technologies more quickly, as vendors develop more efficient ways to implement the specifications – which are then integrated into future releases. Standardized interfaces can also ease ongoing product maintenance and updates, thanks to backward and forward compatibility, while also encouraging long-term developer support.
Most importantly, the use of standards removes the burden of designing (or selecting) a proprietary interface, allowing a developer to focus on “higher value” technologies that sit higher up in the protocol stack and provide product differentiation, such as applications that leverage machine learning and artificial intelligence to provide enhanced product functionality.
MIPI I3C: A next-generation industry standard command, control and data interface
MIPI I3C is the successor to I2C and provides a cost-effective, simple, and flexible two-wire interface that can be used to connect sensors, actuators, controls, and simple UI components to host processors. It provides performance, power, and pin-count improvements over I2C, SPI, and UART implementations. MIPI I3C Basic, which bundles the most commonly used I3C features for embedded developers, is also available under a royalty-free licensing environment for all implementers.
I3C controller with combination of I3C and I2C targets
To meet the key challenges described above, I3C has been developed to provide the following capabilities:
- Supports typical data rate of 10 Mbps with options for higher-performance, high-data-rate modes that provide speeds in excess of 30 Mbps (for single-lane mode).
- Is implemented using complementary metal oxide semiconductor (CMOS) I/O using a two-wire interface to minimize pin counts and the number of signal paths between components.
- Supports in-band-interrupts (IBIs) to negate the need for additional physical lanes for interrupt signals.
- Consumes low amounts of energy per bit transported.
- Offers power-efficient, high-speed batch data transfers and allows components to send infrequent bursts of data while minimizing energy consumption.
- Includes “sleep mode” and IBIs to enable peripheral components to wake host processors only when necessary to conserve power consumption.
- Provides synchronous and asynchronous time-stamping to improve the accuracy of applications that use signals from various sensors.
- Is backward compatible with I2C and allows mixed use of I2C and I3C components within a device.
- Is supplemented by a standard conformance test suite, ensuring interoperability and compatibility between different vendors’ solutions.
I3C is supported by an active industry working group that continues to enhance the specification, seeking to develop ever extended path lengths, reduce power consumption, and realize even lower pin counts for implementers.
I3C and I2C energy consumption and raw bitrates
Conclusion
Embedded command, control and data interfaces are essential building blocks within all IIoT devices. As IIoT devices integrate ever more powerful capabilities, existing command and control interfaces may struggle to keep up with the bandwidth, ultra-low power consumption, and miniaturization demands of next-generation IoT devices. Developers will need to solve these challenges by implementing newer command and control interfaces. Adopting industry standards will not only help developers meet these challenges but also provide many other benefits such as interoperability, backward compatibility, and cost reduction. MIPI I3C is an example of a next-generation industry-led standard for command, control and data interface that meets the challenges of next-generation IIoT devices.
Tim is a hardware engineer with over 10 years of experience working in the semiconductor industry. He is currently a System Architect at Intel Corporation where he works to create and enable standards for industry advancement. In 2020, Tim was elected as chair of the MIPI I3C Working group (formally called the MIPI Sensors Working Group) where he leads a cross industry group of MIPI members who develop and maintain the MIPI I3C and I3C Basic interface specifications.
Tim holds a BS degree in Electrical and Computer Engineering from Oregon State University.